IBM Tivoli Software Enhances Operating Stability and Efficiency for Major Chinese Automotive Company
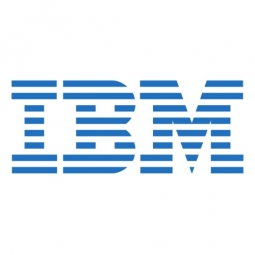
Technology Category
- Functional Applications - Enterprise Resource Planning Systems (ERP)
- Platform as a Service (PaaS) - Application Development Platforms
Applicable Industries
- Automotive
Use Cases
- Leasing Finance Automation
- Material Handling Automation
About The Customer
The customer is a major automotive company based in China. The company manufactures and sells multiple brands of automobiles in mainland China. The company had a large and complex workload with numerous jobs running on multiple platforms. The company was using proprietary scheduling software and largely manual processes for setting job schedules, monitoring job statuses and importing job attributes and dependencies within its SAP ERP, database, Java and IBM InfoSphere® DataStage® software environments.
The Challenge
The automotive company, based in China, was struggling with the efficient scheduling and management of a large number of jobs within multiple software environments. The company had numerous jobs with complex dependencies running on multiple platforms. The limited capabilities of the company’s proprietary scheduling software and the largely manual processes in place for setting job schedules, monitoring job statuses and importing job attributes and dependencies within the company’s SAP ERP, database, Java and IBM InfoSphere® DataStage® software environments posed a significant challenge. The company was in dire need of an automated workload-management solution to increase operating efficiency.
The Solution
The company engaged IBM Software Services for Tivoli to implement a suite of IBM Tivoli workload automation software. Initially, the company replaced its proprietary job scheduler software with IBM Tivoli Workload Scheduler software to schedule jobs across all platforms in the enterprise. Following this, it deployed IBM Tivoli Dynamic Workload Broker software to schedule dynamic jobs and IBM Tivoli Workload Scheduler for Applications software to schedule SAP ERP application jobs in the core production environment. This suite of IBM Tivoli software provided a centralized view of workload schedules and dependencies, enabling the company to run jobs in an orderly and timely way without conflict, while balancing resources and extending sophisticated workload automation to business applications.
Operational Impact
Quantitative Benefit
Case Study missing?
Start adding your own!
Register with your work email and create a new case study profile for your business.
Related Case Studies.
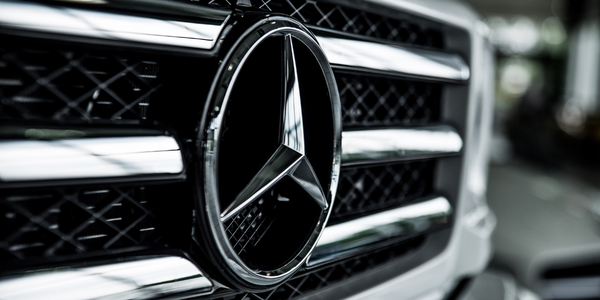
Case Study
Integral Plant Maintenance
Mercedes-Benz and his partner GAZ chose Siemens to be its maintenance partner at a new engine plant in Yaroslavl, Russia. The new plant offers a capacity to manufacture diesel engines for the Russian market, for locally produced Sprinter Classic. In addition to engines for the local market, the Yaroslavl plant will also produce spare parts. Mercedes-Benz Russia and his partner needed a service partner in order to ensure the operation of these lines in a maintenance partnership arrangement. The challenges included coordinating the entire maintenance management operation, in particular inspections, corrective and predictive maintenance activities, and the optimizing spare parts management. Siemens developed a customized maintenance solution that includes all electronic and mechanical maintenance activities (Integral Plant Maintenance).

Case Study
Monitoring of Pressure Pumps in Automotive Industry
A large German/American producer of auto parts uses high-pressure pumps to deburr machined parts as a part of its production and quality check process. They decided to monitor these pumps to make sure they work properly and that they can see any indications leading to a potential failure before it affects their process.