Technology Category
- Analytics & Modeling - Computer Vision Software
Applicable Industries
- Automotive
- Finance & Insurance
Applicable Functions
- Product Research & Development
- Quality Assurance
Use Cases
- Experimentation Automation
- Time Sensitive Networking
Services
- Testing & Certification
About The Customer
The International Centre for Automotive Technology (ICAT) is located in Gurgaon, a rapidly flourishing business hub in North India. ICAT is a division of the National Automotive Testing and Research Infrastructure Project (NATRIP) Implementation Society (NATIS), an independently registered society and an apex body for the implementation of NATRIP for the Government of India. ICAT is an ultra-modern Automotive Testing and R & D centre with a vision to evolve into a state-of-the-art automotive R & D hub. It aims to provide high-end automotive design, test, and validation services to the ever-growing automobile industry in the country.
The Challenge
The International Centre for Automotive Technology (ICAT), a division of the National Automotive Testing and Research Infrastructure Project (NATRIP) Implementation Society (NATIS), is a leading automotive testing and R&D center in North India. ICAT's mission is to integrate advanced automotive technology to support the industry in component development for new classes of vehicles and develop cutting-edge technical expertise to expand upon an impeccable range of automotive services. However, the team faced significant challenges in achieving this mission. Previously, they conducted physical testing of automotive products, a method that risked losing both time and money if the product failed the test. Additionally, the team had to perform complex calculations to solve issues and arrive at accurate designs of products. These issues posed daunting challenges to the team and often turned into time-consuming tasks. To develop ICAT into a Centre of Excellence in component development for the automotive industry, the team needed efficient and validated CAE software tools that would enable them to find appropriate and quick solutions to real-world problems.
The Solution
ICAT invested in Altair HyperWorks, a robust CAE tool that they believed could help them achieve their quality benchmarks and timelines during new product designing and testing phases. ICAT selected HyperWorks during the Government of India’s NATRIP tender process for their CAE lab. Initially, the team worked on a few basic in-house projects. As their requirements grew, they started using HyperWorks for certifications to the bus industry. The ICAT team now uses Altair HyperWorks extensively for simulating automotive industry standards and is currently focused on simulating around 30 standards. They currently use Altair HyperMesh® and HyperCrash® as pre-processors, and Altair RADIOSS® and OptiStruct® as solvers. They use these robust software solutions to work on structural simulations like bus rollover testing, impact and crash simulations, and quasistatic loading applications. The ICAT team also has plans to support OEMs in their product development cycle and is keen to experience the capabilities of Altair NVH Director in the future.
Operational Impact
Quantitative Benefit
Case Study missing?
Start adding your own!
Register with your work email and create a new case study profile for your business.
Related Case Studies.
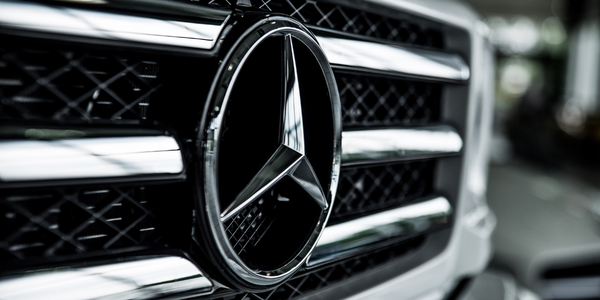
Case Study
Integral Plant Maintenance
Mercedes-Benz and his partner GAZ chose Siemens to be its maintenance partner at a new engine plant in Yaroslavl, Russia. The new plant offers a capacity to manufacture diesel engines for the Russian market, for locally produced Sprinter Classic. In addition to engines for the local market, the Yaroslavl plant will also produce spare parts. Mercedes-Benz Russia and his partner needed a service partner in order to ensure the operation of these lines in a maintenance partnership arrangement. The challenges included coordinating the entire maintenance management operation, in particular inspections, corrective and predictive maintenance activities, and the optimizing spare parts management. Siemens developed a customized maintenance solution that includes all electronic and mechanical maintenance activities (Integral Plant Maintenance).

Case Study
Monitoring of Pressure Pumps in Automotive Industry
A large German/American producer of auto parts uses high-pressure pumps to deburr machined parts as a part of its production and quality check process. They decided to monitor these pumps to make sure they work properly and that they can see any indications leading to a potential failure before it affects their process.