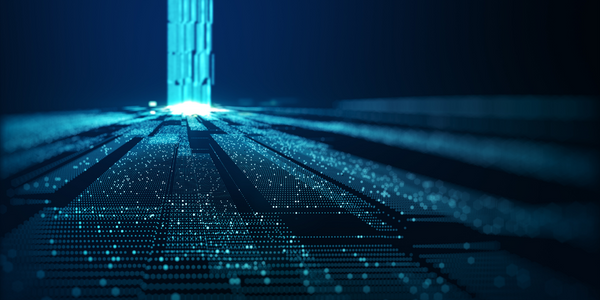
- Infrastructure as a Service (IaaS)
- Platform as a Service (PaaS) - Data Management Platforms
- Electronics
- Discrete Manufacturing
- Factory Operations Visibility & Intelligence
Contextual and background data is often buried and in various formats; Storage and distribution of large amounts of raw data requires considerable compute resources and infrastructure; The cost of installation and maintenance of new computers, servers, and network equipment to collect and distribute data needs to be minimized. GOAL Establish new open environments for future factory operation visualization scenarios, with data upload and simulation capability to augment physical factory equipment; Provide a cloud-based platform that can combine factory sensor and operational data to enhance the visibility and analysis of key manufacturing processes, thereby enabling improvement of operational efficiency.
*This is an IIC testbed currently in progress.* PARTICIPATING MEMBERS Fujitsu Limited, Cisco MARKET SEGMENT Manufacturing of complex, composite products (i.e. IT equipment - notebooks, network appliances, etc). FEATURES Ability to combine, visualize, and correlate diverse data sources that greatly vary in nature, origin, and lifecycles; Available as a cloud-based service; Support for Manufacturing and Repair process control based on priorities in delivery schedules; Extensibility with enhanced visual rendering tools for process status and flow, product tracking, schedules, and machinery status; Plug-in capabilities for analytics and diagnostics. TESTBED INTRODUCTION The Factory Operations Visibility & Intelligence (FOVI) Testbed makes it possible to simulate a factory environment in order to visualize results that can then be used to determine how the process can be optimized. The work on FOVI stems from two separate Operations Visibility and Intelligence applications in two factories in Japan: one for notebook computers and another for network appliances. Both use cases have a lot in common with respect to processing data, analytics, and visualization technologies. Ideally they should use a common software foundation while their future evolution requires a more open architecture. Work on the testbed will be led by Industrial Internet Consortium member Fujitsu Limited with Industrial Internet Consortium founding member, Cisco, collaborating on the in-factory testbed edge infrastructure.
Case Study missing?
Start adding your own!
Register with your work email and create a new case study profile for your business.
Related Case Studies.
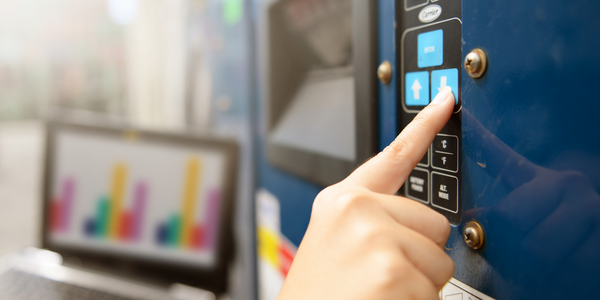
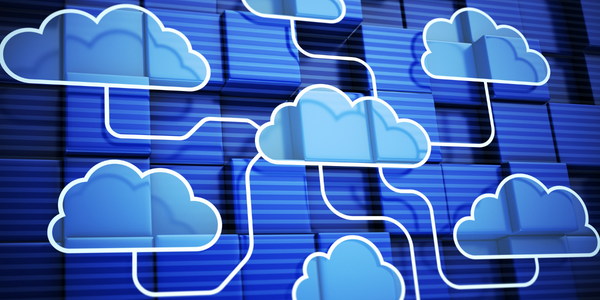
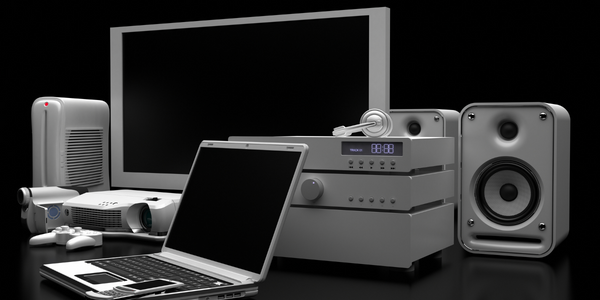