Technology Category
- Sensors - Air Pollution Sensors
- Sensors - Environmental Sensors
Applicable Industries
- Automotive
- Equipment & Machinery
Applicable Functions
- Maintenance
Use Cases
- Manufacturing System Automation
- Predictive Maintenance
Services
- System Integration
About The Customer
Dürr is one of the world’s leading mechanical and plant engineering firms. Its turnkey paint shops, final assembly systems, and machine and robot technology harness digitalization and Industry 4.0 concepts to power manufacturing across the automotive industry. Dürr generates over €3.5 billion in revenue annually, and its paint shops, used by every major automaker globally, have achieved massive energy consumption savings. The company has been a leader in mechanical engineering since Paul Dürr opened his first metal workshop in 1895 in Germany.
The Challenge
Dürr, a leading mechanical and plant engineering firm, faced several challenges in its operations. The company was under pressure to meet customer demand for secure monitoring of production data and self-service predictive maintenance capabilities. There was also a need to avoid painting faults caused by materials or equipment wear. Dürr was also grappling with growing ESG requirements to cut energy use and emissions. The company was in the process of transforming from traditional manufacturing to a digital business, which presented its own set of challenges.
The Solution
Dürr adopted the Cumulocity IoT Platform to address its challenges. The company implemented real-time monitoring for 64 robots, which accelerated customer growth and planned robot purchases. Dürr also co-developed self-service analytics tools for operational engineers, which helped generate new revenue streams from innovative digital services. The system consists of an industrial PC located next to each robotic paint station which has an IIoT edge installation that can control all painting processes, monitor for defects and alert operators to customized triggers. Using self-service predictive maintenance and anomaly detection, air nozzles are now cleaned only when needed to prevent contamination. Defective paint runs due to contaminated shaping air nozzles no longer happen because the new system detects such faults immediately.
Operational Impact
Quantitative Benefit
Case Study missing?
Start adding your own!
Register with your work email and create a new case study profile for your business.
Related Case Studies.
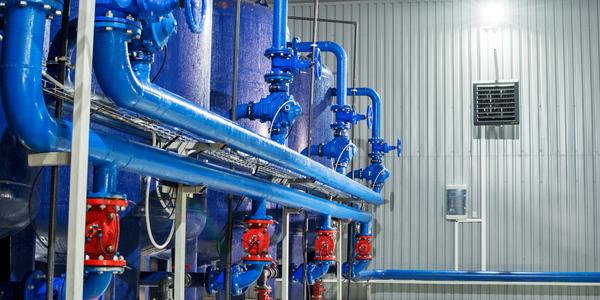
Case Study
Smart Water Filtration Systems
Before working with Ayla Networks, Ozner was already using cloud connectivity to identify and solve water-filtration system malfunctions as well as to monitor filter cartridges for replacements.But, in June 2015, Ozner executives talked with Ayla about how the company might further improve its water systems with IoT technology. They liked what they heard from Ayla, but the executives needed to be sure that Ayla’s Agile IoT Platform provided the security and reliability Ozner required.
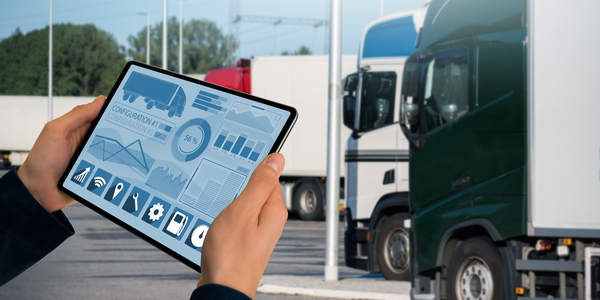
Case Study
IoT enabled Fleet Management with MindSphere
In view of growing competition, Gämmerler had a strong need to remain competitive via process optimization, reliability and gentle handling of printed products, even at highest press speeds. In addition, a digitalization initiative also included developing a key differentiation via data-driven services offers.
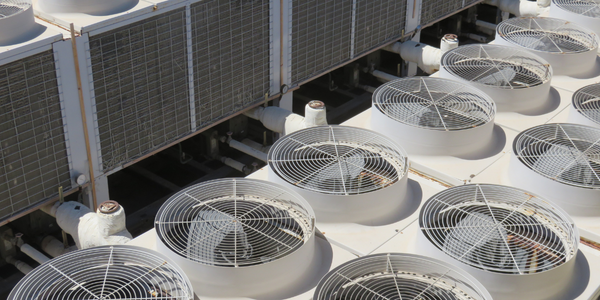
Case Study
Predictive Maintenance for Industrial Chillers
For global leaders in the industrial chiller manufacturing, reliability of the entire production process is of the utmost importance. Chillers are refrigeration systems that produce ice water to provide cooling for a process or industrial application. One of those leaders sought a way to respond to asset performance issues, even before they occur. The intelligence to guarantee maximum reliability of cooling devices is embedded (pre-alarming). A pre-alarming phase means that the cooling device still works, but symptoms may appear, telling manufacturers that a failure is likely to occur in the near future. Chillers who are not internet connected at that moment, provide little insight in this pre-alarming phase.
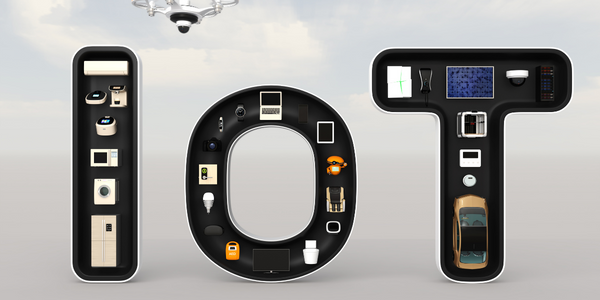
Case Study
Premium Appliance Producer Innovates with Internet of Everything
Sub-Zero faced the largest product launch in the company’s history:It wanted to launch 60 new products as scheduled while simultaneously opening a new “greenfield” production facility, yet still adhering to stringent quality requirements and manage issues from new supply-chain partners. A the same time, it wanted to increase staff productivity time and collaboration while reducing travel and costs.
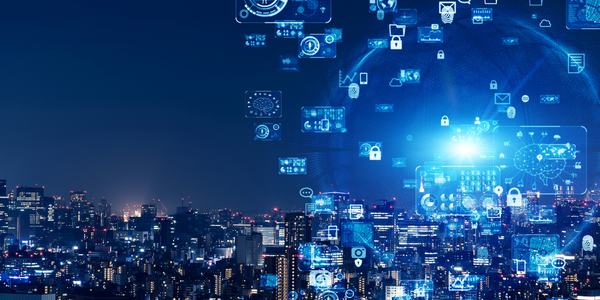
Case Study
Integration of PLC with IoT for Bosch Rexroth
The application arises from the need to monitor and anticipate the problems of one or more machines managed by a PLC. These problems, often resulting from the accumulation over time of small discrepancies, require, when they occur, ex post technical operations maintenance.
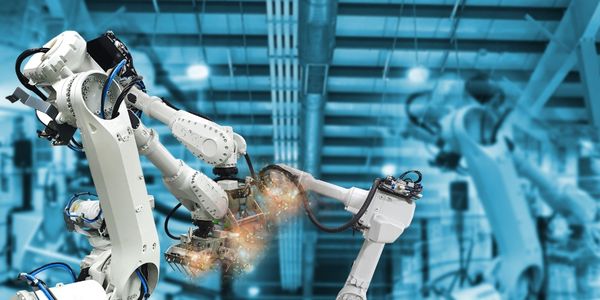
Case Study
Robot Saves Money and Time for US Custom Molding Company
Injection Technology (Itech) is a custom molder for a variety of clients that require precision plastic parts for such products as electric meter covers, dental appliance cases and spools. With 95 employees operating 23 molding machines in a 30,000 square foot plant, Itech wanted to reduce man hours and increase efficiency.