Customer Company Size
Large Corporate
Region
- Asia
- America
- Europe
Country
- Korea
- China
- Czech Republic
- Norway
- United States
Product
- 3DEXPERIENCE platform
- CATIA V6
- ENOVIA V6
- DELMIA V6
Tech Stack
- PLM system
- 3D virtual simulation
- Concurrent engineering
Implementation Scale
- Enterprise-wide Deployment
Impact Metrics
- Productivity Improvements
- Cost Savings
- Digital Expertise
Technology Category
- Platform as a Service (PaaS) - Application Development Platforms
- Application Infrastructure & Middleware - Data Exchange & Integration
Applicable Industries
- Equipment & Machinery
Applicable Functions
- Product Research & Development
- Discrete Manufacturing
Use Cases
- Manufacturing System Automation
- Predictive Maintenance
- Digital Twin
Services
- Software Design & Engineering Services
- System Integration
About The Customer
Doosan Infracore, part of the Doosan Group, began as a shipbuilding machinery plant in 1937. Today, it is a globally renowned player in the industrial equipment industry, and is ranked fifth in the machinery, machine tool, and small equipment construction sector worldwide. It is also the number one manufacturer of mid-size diesel and gas engines and articulated dump trucks in Korea. Since it joined the Doosan Group in 2005, Doosan Infracore has been busy expanding its business, acquiring companies such as Bobcat and CTI in the USA, ATL in Germany, Moxy Engineering AS in Norway, Yantai Machinery in China, and the machine tool business division of Doosan Mechatec in Korea. As a result, the company’s exports increased almost two-fold in just two years, earning it the 2 Billion Dollar Export Tower Award from the Korea International Trade Association Day in 2007. Maintaining this steady growth, Doosan Infracore has positioned itself to overtake its global competitors and become one of the top three industrial machinery manufacturers worldwide.
The Challenge
Doosan Infracore, a globally renowned player in the industrial equipment industry, aimed to become one of the top three global machinery suppliers by 2020. To achieve this, the company needed to improve the productivity and product quality of its 14 subsidiaries and R&D centers in the US, China, Norway, and the Czech Republic. The company faced challenges in reducing product development time, errors, and rework, and improving data integration and security throughout the product lifecycle. Their existing PLM system, a collection of heterogeneous, tailor-made, in-house software applications, generated data incompatibility issues from one site to another, making it difficult to address these challenges.
The Solution
After a year of analyzing several PLM solutions, Doosan Infracore chose Dassault Systèmes’ 3DEXPERIENCE platform, including CATIA V6, ENOVIA V6, and DELMIA V6, for product development, multi-site collaboration, and manufacturing simulation. The 3DEXPERIENCE platform’s applications are seamlessly integrated in a unique collaborative work environment, which perfectly reflects Doosan Infracore’s R&D motto: ‘Design anywhere/Build anywhere.’ Concurrent engineering and implementing design changes early in the process help Doosan Infracore engineers to drastically reduce their product development time. Bills of Materials (BOM), which were managed separately previously, can be managed with one real-time data during the entire process – planning, development, design, sales, and service.
Operational Impact
Quantitative Benefit
Case Study missing?
Start adding your own!
Register with your work email and create a new case study profile for your business.
Related Case Studies.
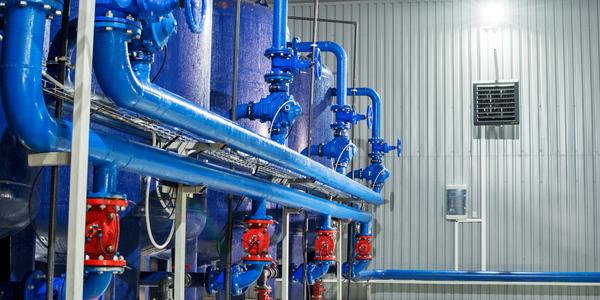
Case Study
Smart Water Filtration Systems
Before working with Ayla Networks, Ozner was already using cloud connectivity to identify and solve water-filtration system malfunctions as well as to monitor filter cartridges for replacements.But, in June 2015, Ozner executives talked with Ayla about how the company might further improve its water systems with IoT technology. They liked what they heard from Ayla, but the executives needed to be sure that Ayla’s Agile IoT Platform provided the security and reliability Ozner required.
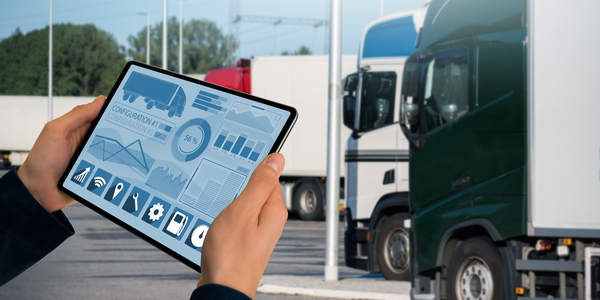
Case Study
IoT enabled Fleet Management with MindSphere
In view of growing competition, Gämmerler had a strong need to remain competitive via process optimization, reliability and gentle handling of printed products, even at highest press speeds. In addition, a digitalization initiative also included developing a key differentiation via data-driven services offers.
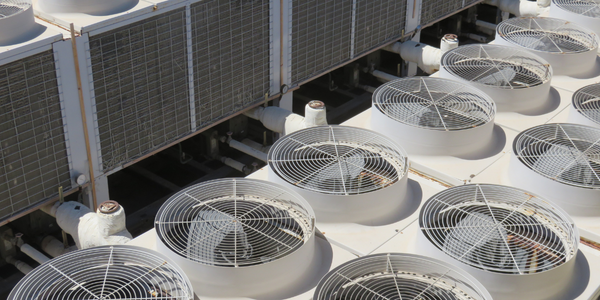
Case Study
Predictive Maintenance for Industrial Chillers
For global leaders in the industrial chiller manufacturing, reliability of the entire production process is of the utmost importance. Chillers are refrigeration systems that produce ice water to provide cooling for a process or industrial application. One of those leaders sought a way to respond to asset performance issues, even before they occur. The intelligence to guarantee maximum reliability of cooling devices is embedded (pre-alarming). A pre-alarming phase means that the cooling device still works, but symptoms may appear, telling manufacturers that a failure is likely to occur in the near future. Chillers who are not internet connected at that moment, provide little insight in this pre-alarming phase.
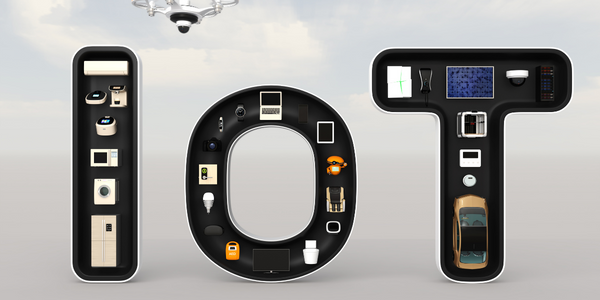
Case Study
Premium Appliance Producer Innovates with Internet of Everything
Sub-Zero faced the largest product launch in the company’s history:It wanted to launch 60 new products as scheduled while simultaneously opening a new “greenfield” production facility, yet still adhering to stringent quality requirements and manage issues from new supply-chain partners. A the same time, it wanted to increase staff productivity time and collaboration while reducing travel and costs.
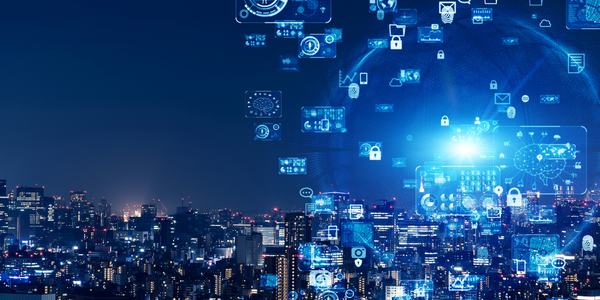
Case Study
Integration of PLC with IoT for Bosch Rexroth
The application arises from the need to monitor and anticipate the problems of one or more machines managed by a PLC. These problems, often resulting from the accumulation over time of small discrepancies, require, when they occur, ex post technical operations maintenance.
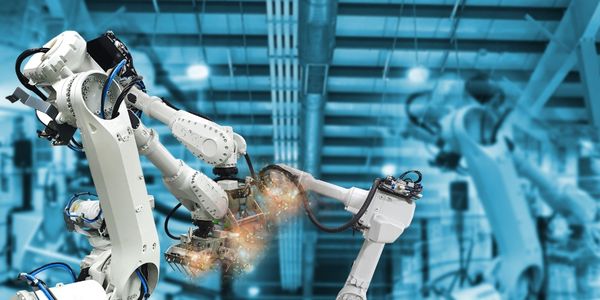
Case Study
Robot Saves Money and Time for US Custom Molding Company
Injection Technology (Itech) is a custom molder for a variety of clients that require precision plastic parts for such products as electric meter covers, dental appliance cases and spools. With 95 employees operating 23 molding machines in a 30,000 square foot plant, Itech wanted to reduce man hours and increase efficiency.