Technology Category
- Functional Applications - Manufacturing Execution Systems (MES)
Applicable Industries
- Automotive
- Construction & Infrastructure
Applicable Functions
- Facility Management
- Product Research & Development
Use Cases
- Additive Manufacturing
- Rapid Prototyping
About The Customer
EDAG is Germany's largest independent engineering partner to the worldwide automotive industry. Founded by Horst Eckard in 1969, the company has grown to employ over 7900 employees worldwide and had a total turnover in 2013 of € 632 Million. EDAG offers its services to all of the automotive industry – from OEMs to suppliers and works with some of the most exciting automotive brands in the world. The company has widespread expertise in integrated development and in the production of vehicles, production facilities, derivatives, and modules. EDAG is continuously seeking new technology and innovative processes to streamline vehicle development, particularly in the area of lightweight design.
The Challenge
Germany's largest independent engineering partner to the global automotive industry, EDAG, was seeking innovative processes to streamline vehicle development, particularly in the area of lightweight design for both passenger and commercial vehicles. The automotive industry is faced with the challenge of increasing fuel efficiency and meeting legal requirements on emissions, while ensuring safety and competitive pricing. Traditional methods of manufacturing often require design proposals to be adapted to manufacturing constraints, which can limit the potential for lightweight design. In a recent project, EDAG engineers were tasked with developing and manufacturing affordable lightweight constructions of a commercial vehicle that could meet individual customer specifications without major changes in production facilities. This required a process that not only offered the best design approach but also incorporated the requirements of the selected manufacturing method.
The Solution
EDAG leveraged its engineering knowledge to combine state-of-the-art computer-aided engineering tools with new production technologies such as additive manufacturing. The company used the best practice optimization tool OptiStruct to develop a lightweight biomimicry structure of a truck cabin and chassis, which was then manufactured using additive manufacturing methods. This combination of topology optimization and additive manufacturing allowed EDAG to fully benefit from the design freedom of additive manufacturing. The engineers conducted multi-physical optimizations and combined strength and crash demands of the vehicle to find the optimal solution for the final design. The result was an optimized frame structure that integrated a large number of functions and provided a significant weight advantage compared to a non-optimized structure, manufactured with conventional construction methods. A specially designed safety cell inside the cab was also designed and analyzed to protect occupants from typical injury risks in crash scenarios.
Operational Impact
Quantitative Benefit
Case Study missing?
Start adding your own!
Register with your work email and create a new case study profile for your business.
Related Case Studies.
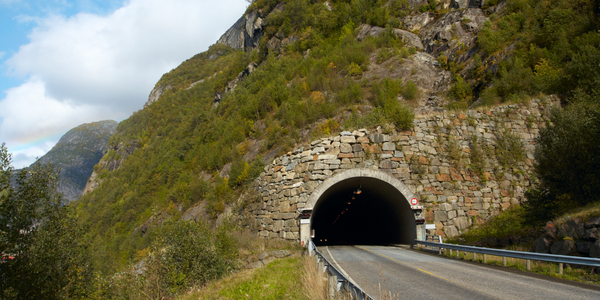
Case Study
IoT System for Tunnel Construction
The Zenitaka Corporation ('Zenitaka') has two major business areas: its architectural business focuses on structures such as government buildings, office buildings, and commercial facilities, while its civil engineering business is targeted at structures such as tunnels, bridges and dams. Within these areas, there presented two issues that have always persisted in regard to the construction of mountain tunnels. These issues are 'improving safety" and "reducing energy consumption". Mountain tunnels construction requires a massive amount of electricity. This is because there are many kinds of electrical equipment being used day and night, including construction machinery, construction lighting, and ventilating fan. Despite this, the amount of power consumption is generally not tightly managed. In many cases, the exact amount of power consumption is only ascertained when the bill from the power company becomes available. Sometimes, corporations install demand-monitoring equipment to help curb the maximum power demanded. However, even in these cases, the devices only allow the total volume of power consumption to be ascertained, or they may issue warnings to prevent the contracted volume of power from being exceeded. In order to tackle the issue of reducing power consumption, it was first necessary to obtain an accurate breakdown of how much power was being used in each particular area. In other words, we needed to be able to visualize the amount of power being consumed. Safety, was also not being managed very rigorously. Even now, tunnel construction sites often use a 'name label' system for managing entry into the work site. Specifically, red labels with white reverse sides that bear the workers' names on both sides are displayed at the tunnel work site entrance. The workers themselves then flip the name label to the appropriate side when entering or exiting from the work site to indicate whether or not they are working inside the tunnel at any given time. If a worker forgets to flip his or her name label when entering or exiting from the tunnel, management cannot be performed effectively. In order to tackle the challenges mentioned above, Zenitaka decided to build a system that could improve the safety of tunnel construction as well as reduce the amount of power consumed. In other words, this new system would facilitate a clear picture of which workers were working in each location at the mountain tunnel construction site, as well as which processes were being carried out at those respective locations at any given time. The system would maintain the safety of all workers while also carefully controlling the electrical equipment to reduce unnecessary power consumption. Having decided on the concept, our next concern was whether there existed any kind of robust hardware that would not break down at the construction work site, that could move freely in response to changes in the working environment, and that could accurately detect workers and vehicles using radio frequency identification (RFID). Given that this system would involve many components that were new to Zenitaka, we decided to enlist the cooperation of E.I.Sol Co., Ltd. ('E.I.Sol') as our joint development partner, as they had provided us with a highly practical proposal.
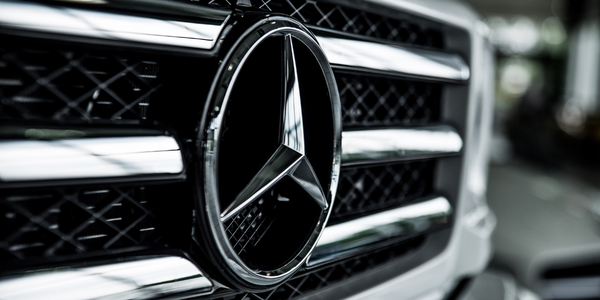
Case Study
Integral Plant Maintenance
Mercedes-Benz and his partner GAZ chose Siemens to be its maintenance partner at a new engine plant in Yaroslavl, Russia. The new plant offers a capacity to manufacture diesel engines for the Russian market, for locally produced Sprinter Classic. In addition to engines for the local market, the Yaroslavl plant will also produce spare parts. Mercedes-Benz Russia and his partner needed a service partner in order to ensure the operation of these lines in a maintenance partnership arrangement. The challenges included coordinating the entire maintenance management operation, in particular inspections, corrective and predictive maintenance activities, and the optimizing spare parts management. Siemens developed a customized maintenance solution that includes all electronic and mechanical maintenance activities (Integral Plant Maintenance).
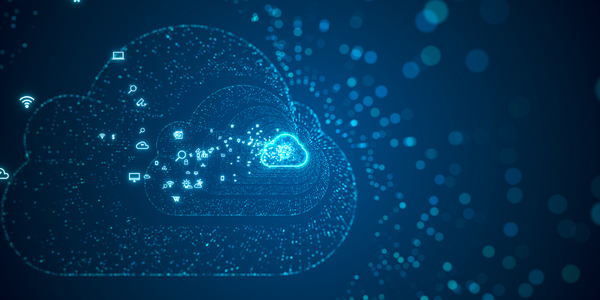
Case Study
Splunk Partnership Ties Together Big Data & IoT Services
Splunk was faced with the need to meet emerging customer demands for interfacing IoT projects to its suite of services. The company required an IoT partner that would be able to easily and quickly integrate with its Splunk Enterprise platform, rather than allocating development resources and time to building out an IoT interface and application platform.