Technology Category
- Functional Applications - Transportation Management Systems (TMS)
- Sensors - Autonomous Driving Sensors
Applicable Industries
- Automotive
- Transportation
Applicable Functions
- Logistics & Transportation
- Product Research & Development
Use Cases
- Onsite Human Safety Management
- Public Transportation Management
Services
- System Integration
- Testing & Certification
About The Customer
Sharma & Associates (SA) is a company that provides engineering solutions to the railroad industry. They specialize in railway mechanical and infrastructure engineering, as well as mechanical engineering projects in the automotive and consumer electronics industries. Since 1995, SA has delivered safe, effective, and efficient solutions to its customers, which include the Federal Railroad Administration (FRA), the Association of American Railroads (AAR), railroads and transit agencies, rail car builders, and rail car component manufacturers. SA also works with the National Transportation agency (VOLPE), a part of the U.S. Department of Transportation, which helps the transportation community anticipate emerging problems with technical, operational, and institutional issues.
The Challenge
Train collisions, though not common, can have devastating impacts, especially on the often unprotected rail engineer. The interior of the front rail car is built to withstand a moderate to severe impact, but the engineer console is virtually unprotected, leaving the engineer vulnerable to potentially life-threatening impact injuries. Sharma & Associates (SA), a provider of engineering solutions to the railroad industry, initiated research into creating an Engineer Protection System (EPS) concept. However, SA was not familiar with the necessary safety requirements, available systems, or overall performance tuning of impact environments and needed a partner to help develop the new system. The EPS had to meet specific criteria: it could not be triggered by the engineer and could not interfere with the engineer exiting the control car.
The Solution
SA enlisted the help of Altair ProductDesign for the project. Altair's first task was to create accurate finite element (FE) models of the interior of a standard rail operator's cabin using HyperWorks pre-processor, HyperMesh. They then brought in a human dummy model into the environment and positioned it into the engineer’s seat facing the control panel. Altair’s crash specialists experimented with a wide variety of airbag types, sizes, positioning, and flow rates, along with developing a new deformable knee bolster to absorb impact forces during a crash. The EPS system that the team developed used an automobile passenger style airbag system in combination with a crushable knee bolster to keep injuries to a minimum, while also meeting compartmentalization, egress, and functionality requirements for an unbelted occupant. The development effort used analytical modeling at the system and sub-system levels, in combination with a series of quasi-static and dynamic sled tests using HyperWorks’ RADIOSS solver, to develop and demonstrate system level performance.
Operational Impact
Quantitative Benefit
Case Study missing?
Start adding your own!
Register with your work email and create a new case study profile for your business.
Related Case Studies.
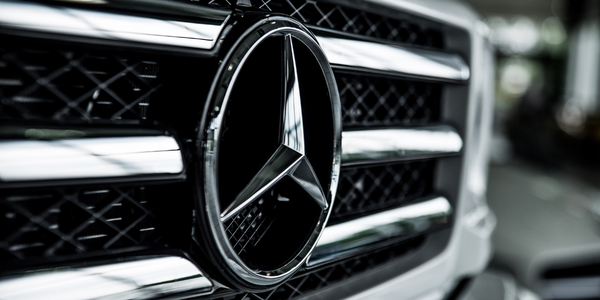
Case Study
Integral Plant Maintenance
Mercedes-Benz and his partner GAZ chose Siemens to be its maintenance partner at a new engine plant in Yaroslavl, Russia. The new plant offers a capacity to manufacture diesel engines for the Russian market, for locally produced Sprinter Classic. In addition to engines for the local market, the Yaroslavl plant will also produce spare parts. Mercedes-Benz Russia and his partner needed a service partner in order to ensure the operation of these lines in a maintenance partnership arrangement. The challenges included coordinating the entire maintenance management operation, in particular inspections, corrective and predictive maintenance activities, and the optimizing spare parts management. Siemens developed a customized maintenance solution that includes all electronic and mechanical maintenance activities (Integral Plant Maintenance).
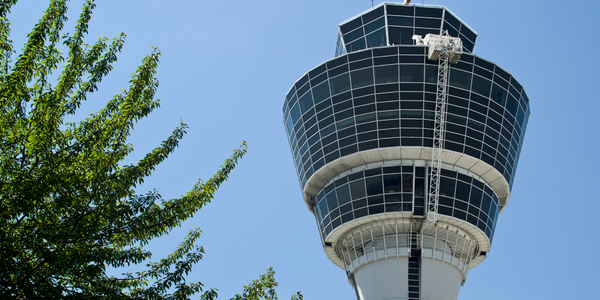
Case Study
Airport SCADA Systems Improve Service Levels
Modern airports are one of the busiest environments on Earth and rely on process automation equipment to ensure service operators achieve their KPIs. Increasingly airport SCADA systems are being used to control all aspects of the operation and associated facilities. This is because unplanned system downtime can cost dearly, both in terms of reduced revenues and the associated loss of customer satisfaction due to inevitable travel inconvenience and disruption.
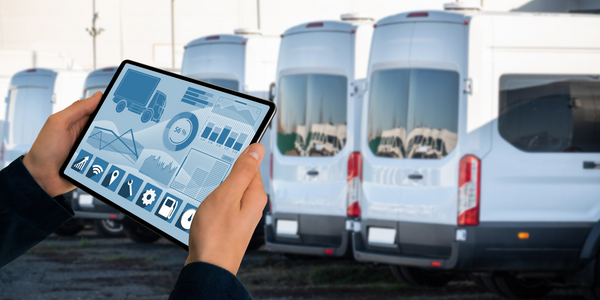
Case Study
IoT-based Fleet Intelligence Innovation
Speed to market is precious for DRVR, a rapidly growing start-up company. With a business model dependent on reliable mobile data, managers were spending their lives trying to negotiate data roaming deals with mobile network operators in different countries. And, even then, service quality was a constant concern.
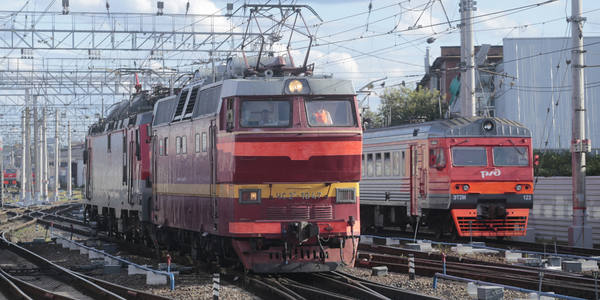
Case Study
Digitize Railway with Deutsche Bahn
To reduce maintenance costs and delay-causing failures for Deutsche Bahn. They need manual measurements by a position measurement system based on custom-made MEMS sensor clusters, which allow autonomous and continuous monitoring with wireless data transmission and long battery. They were looking for data pre-processing solution in the sensor and machine learning algorithms in the cloud so as to detect critical wear.