Technology Category
- Analytics & Modeling - Digital Twin / Simulation
- Functional Applications - Manufacturing Execution Systems (MES)
Applicable Industries
- Equipment & Machinery
- Plastics
Applicable Functions
- Facility Management
- Product Research & Development
Use Cases
- Manufacturing Process Simulation
- Virtual Reality
Services
- System Integration
About The Customer
The National Composites Centre (NCC) is an open-access, industrial-scale, state-of-the art non-profit UK facility for technology development in the manufacture of advanced composites. Established by the University of Bristol, the NCC aims to accelerate the growth of UK industrial output by enabling design and manufacturing enterprises to deliver winning solutions in the application of composites. Since its inception in August 2011, the facility has doubled in size and serves as the primary composites catapult facility in the UK, playing an integral part in the UK’s composites initiative since the government launched its Composites Strategy in November 2009.
The Challenge
The National Composites Centre (NCC), a non-profit UK facility, was tasked with the development of an advanced technology demonstrator, a Sit-ski, using composite materials. The Sit-ski, a device used for sports on mountain slopes by individuals with lower extremity limitations, required a design that would showcase the Centre's capabilities while also delivering performance improvements for the skiers. The challenge was to understand the performance of existing Sit-skis, build kinematic models of the suspension behavior, and design a system that would be lighter and more efficient. The design process needed to consider the use of composite structures at an architecture/system level, and the importance of cost and manufacturability in the product development process.
The Solution
The NCC, in collaboration with the Manufacturing Technology Centre (MTC), Advanced Manufacturing Research Centre (AMRC) and University of Warwick (WMG), used simulation-driven design for the assessment of performance and structural reliability before manufacturing any component. The Altair HyperWorks™ suite was utilized throughout the development process. Altair MotionSolve™ was used to model the kinematic behavior of an existing coil-over suspension system and compared to the new composite leaf spring and damper concept. Altair HyperStudy™ was used in conjunction with Altair MotionSolve to optimize the kinematic behavior and assess the positions and sizes of various structural and suspension elements. Altair OptiStruct™ was used to perform detailed sizing of the laminates in the spring and chassis elements along with the use of the morphing capabilities in Altair HyperMesh™ to optimize the geometry. Altair Inspire™ and Altair Evolve™ were used for visualizing the full assembly and producing images for the reports and presentations.
Operational Impact
Quantitative Benefit
Case Study missing?
Start adding your own!
Register with your work email and create a new case study profile for your business.
Related Case Studies.
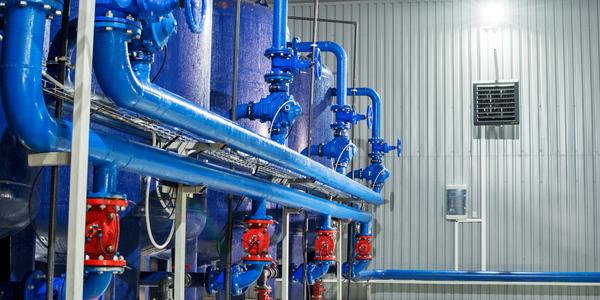
Case Study
Smart Water Filtration Systems
Before working with Ayla Networks, Ozner was already using cloud connectivity to identify and solve water-filtration system malfunctions as well as to monitor filter cartridges for replacements.But, in June 2015, Ozner executives talked with Ayla about how the company might further improve its water systems with IoT technology. They liked what they heard from Ayla, but the executives needed to be sure that Ayla’s Agile IoT Platform provided the security and reliability Ozner required.
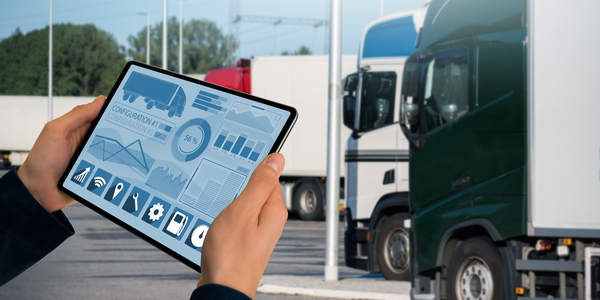
Case Study
IoT enabled Fleet Management with MindSphere
In view of growing competition, Gämmerler had a strong need to remain competitive via process optimization, reliability and gentle handling of printed products, even at highest press speeds. In addition, a digitalization initiative also included developing a key differentiation via data-driven services offers.
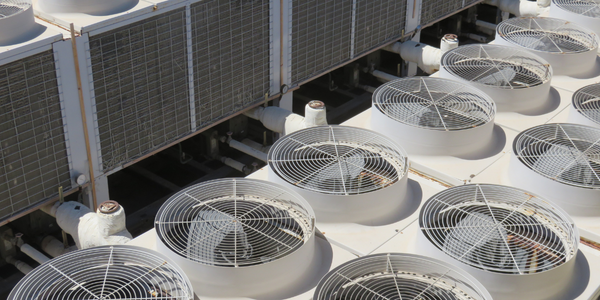
Case Study
Predictive Maintenance for Industrial Chillers
For global leaders in the industrial chiller manufacturing, reliability of the entire production process is of the utmost importance. Chillers are refrigeration systems that produce ice water to provide cooling for a process or industrial application. One of those leaders sought a way to respond to asset performance issues, even before they occur. The intelligence to guarantee maximum reliability of cooling devices is embedded (pre-alarming). A pre-alarming phase means that the cooling device still works, but symptoms may appear, telling manufacturers that a failure is likely to occur in the near future. Chillers who are not internet connected at that moment, provide little insight in this pre-alarming phase.
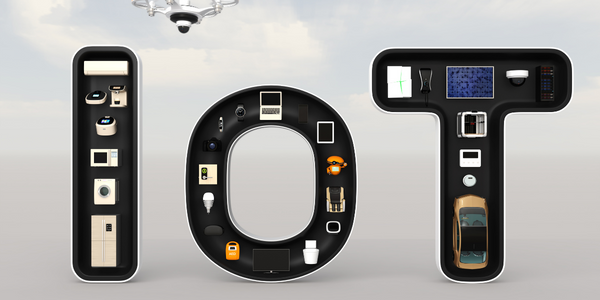
Case Study
Premium Appliance Producer Innovates with Internet of Everything
Sub-Zero faced the largest product launch in the company’s history:It wanted to launch 60 new products as scheduled while simultaneously opening a new “greenfield” production facility, yet still adhering to stringent quality requirements and manage issues from new supply-chain partners. A the same time, it wanted to increase staff productivity time and collaboration while reducing travel and costs.
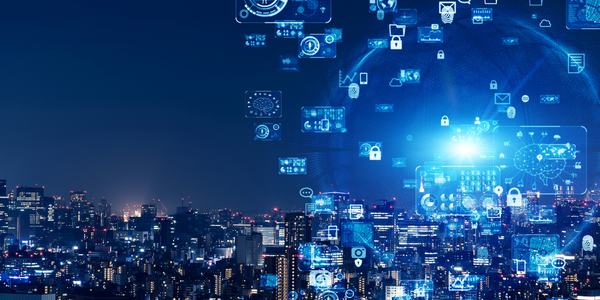
Case Study
Integration of PLC with IoT for Bosch Rexroth
The application arises from the need to monitor and anticipate the problems of one or more machines managed by a PLC. These problems, often resulting from the accumulation over time of small discrepancies, require, when they occur, ex post technical operations maintenance.
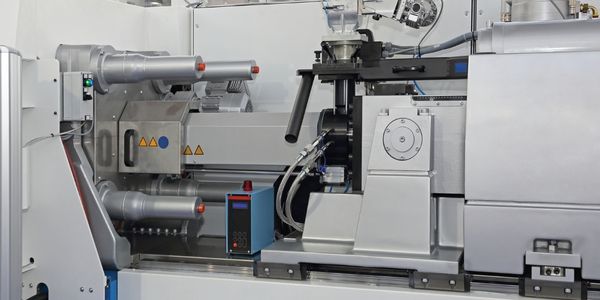
Case Study
Plastic Spoons Case study: Injection Moulding
In order to meet customer expectations by supplying a wide variety of packaging units, from 36 to 1000 spoons per package, a new production and packaging line needed to be built. DeSter wanted to achieve higher production capacity, lower cycle time and a high degree of operator friendliness with this new production line.