Innovative Vehicle Design through System-Level Modeling: A Case Study on China Euro Vehicle Technology
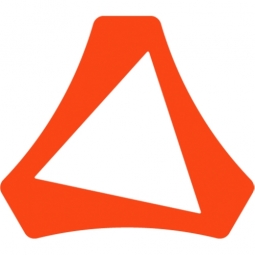
Technology Category
- Analytics & Modeling - Digital Twin / Simulation
- Platform as a Service (PaaS) - Application Development Platforms
Applicable Industries
- Automotive
- Education
Applicable Functions
- Product Research & Development
- Quality Assurance
Use Cases
- Virtual Reality
- Virtual Training
Services
- Testing & Certification
- Training
About The Customer
China Euro Vehicle Technology (CEVT) is an automotive company that focuses on integrating new technologies into passenger vehicles. They are committed to developing new techniques to ensure the successful integration of various systems present in modern vehicle designs. The company is constantly under pressure to innovate and meet higher performance standards without delaying the time to market. They are particularly interested in system-level modeling, a technology that uses specialized software to model the interactions across an entire system. CEVT is dedicated to creating a powerful testing and simulation platform that can verify the functionality of new automotive technologies at earlier stages in the design process.
The Challenge
The automotive industry is under constant pressure to innovate and meet higher performance standards without delaying the time to market. This challenge is particularly evident at China Euro Vehicle Technology (CEVT), where the integration of new technologies into passenger vehicles is a key focus. The company is developing new techniques to ensure the successful integration of various systems present in modern vehicle designs. One of the advanced technologies available for modern automotive design is system-level modeling, which uses specialized software to model the interactions across an entire system. However, the challenge lies in creating a powerful testing and simulation platform that can verify the functionality of new automotive technologies at earlier stages in the design process.
The Solution
CEVT engineer Michael Palander, with his team, decided to use system-level modeling to create a robust testing and simulation platform. They chose MapleSim as their modeling and simulation tool due to its Modelica standard for system-modeling components. The team aimed to create a simulation platform that could validate a wide range of design components, from software controllers to individual hardware subsystems, in what is known as “in-the-loop” simulations. To avoid the typical slowdowns associated with adopting a new modeling tool, the team opted for customized training services provided by Maplesoft Engineering Solutions. Over a three-day training program, modeling experts from Maplesoft worked directly with the research team, helping them become proficient with MapleSim. The team quickly worked through the basics of model creation, before moving on to training related to their specific project needs.
Operational Impact
Case Study missing?
Start adding your own!
Register with your work email and create a new case study profile for your business.
Related Case Studies.
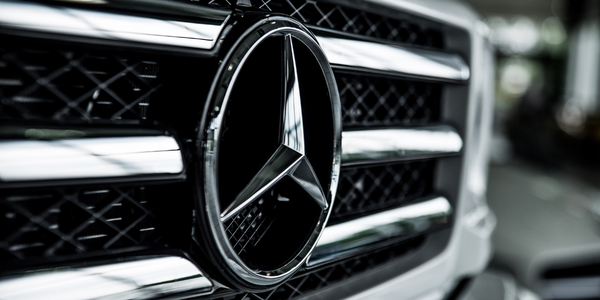
Case Study
Integral Plant Maintenance
Mercedes-Benz and his partner GAZ chose Siemens to be its maintenance partner at a new engine plant in Yaroslavl, Russia. The new plant offers a capacity to manufacture diesel engines for the Russian market, for locally produced Sprinter Classic. In addition to engines for the local market, the Yaroslavl plant will also produce spare parts. Mercedes-Benz Russia and his partner needed a service partner in order to ensure the operation of these lines in a maintenance partnership arrangement. The challenges included coordinating the entire maintenance management operation, in particular inspections, corrective and predictive maintenance activities, and the optimizing spare parts management. Siemens developed a customized maintenance solution that includes all electronic and mechanical maintenance activities (Integral Plant Maintenance).

Case Study
Monitoring of Pressure Pumps in Automotive Industry
A large German/American producer of auto parts uses high-pressure pumps to deburr machined parts as a part of its production and quality check process. They decided to monitor these pumps to make sure they work properly and that they can see any indications leading to a potential failure before it affects their process.