INTECH DMLS Achieves 27% Weight Reduction in 3D Printed Satellite Component using Altair Inspire™ and OptiStruct™
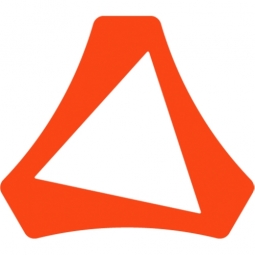
Technology Category
- Networks & Connectivity - Cellular
Applicable Industries
- Aerospace
- Automotive
Applicable Functions
- Product Research & Development
- Quality Assurance
Use Cases
- Additive Manufacturing
- Rapid Prototyping
Services
- Hardware Design & Engineering Services
- Testing & Certification
About The Customer
INTECH DMLS is a visionary in the field of metal-based DMLS 3D printing in India. The company has a creative design team, a meticulous analysis team, a dedicated machine shop, an accurate post-processing facility, and a competent quality control services team. With over 30 years of metallurgical expertise and 25 years of machining expertise, INTECH DMLS has established itself as the leader of the Metal Additive Manufacturing industry in India. The company provides complete solutions from concept design to fully functional metal-based production parts and manufactures precision components for the aerospace, automotive, tool & die, rapid prototyping, general engineering, and medical industry.
The Challenge
INTECH DMLS, a leader in the field of metal-based DMLS 3D printing in India, was faced with the challenge of reducing the weight of a camera holder to be placed on a satellite. The company needed to get the weight right the first time, eliminating the need for prototype iterations. This was a unique challenge as the company did not have the luxury of making errors and iterating. The team had to focus on product design optimization, analysis, mechanical integrity, heat transfer, and other criteria while developing Bionic, Dynamic, and Cellular structures and carrying out lightweight analysis for their products. The camera holder had to be lightweight but still withstand a predefined load and assist in the smooth functioning of the satellite. The customer also wanted the holder to be of a specific weight - not too light nor too heavy - and stiff enough to withstand dynamic load.
The Solution
To meet this challenge, INTECH DMLS decided to leverage simulation as a standard process to rule out errors and invested in Altair HyperWorks to realize their simulation needs. Simulation using Altair HyperWorks played a crucial role in optimizing the product design. The team used simulation to develop the Bionic, Dynamic, and Cellular structure and carry out the weight optimization for the project. They performed various analyses required early in the development cycle to make sure they got it right the first time. The team verified mechanical integrity and its working and checked the support that was required for 3D printing. The team also checked and ensured various parameters with respect to heat transfer. The key solutions to address their challenges were Topology Optimization and Structural Analysis using Altair HyperWorks. Altair OptiStruct was the main solver used for analysis of the project and Altair Inspire was used for concept generation and analysis at the early stage to achieve the validated design of the product vis-a-vis the bionic shape of the product.
Operational Impact
Quantitative Benefit
Case Study missing?
Start adding your own!
Register with your work email and create a new case study profile for your business.
Related Case Studies.
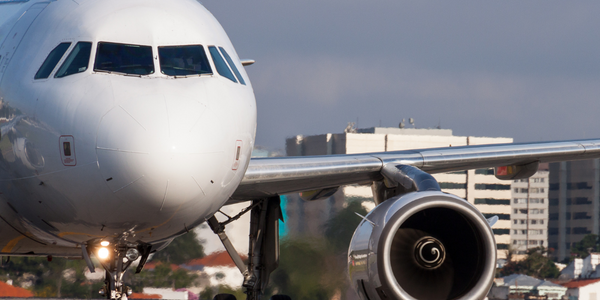
Case Study
Airbus Soars with Wearable Technology
Building an Airbus aircraft involves complex manufacturing processes consisting of thousands of moving parts. Speed and accuracy are critical to business and competitive advantage. Improvements in both would have high impact on Airbus’ bottom line. Airbus wanted to help operators reduce the complexity of assembling cabin seats and decrease the time required to complete this task.
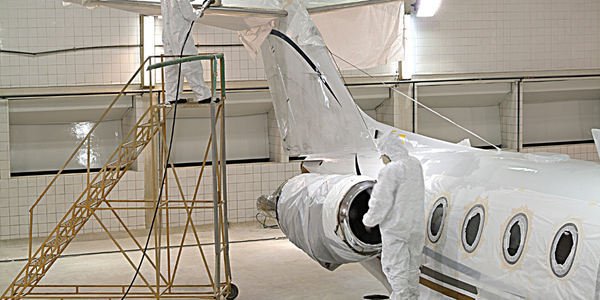
Case Study
Aircraft Predictive Maintenance and Workflow Optimization
First, aircraft manufacturer have trouble monitoring the health of aircraft systems with health prognostics and deliver predictive maintenance insights. Second, aircraft manufacturer wants a solution that can provide an in-context advisory and align job assignments to match technician experience and expertise.
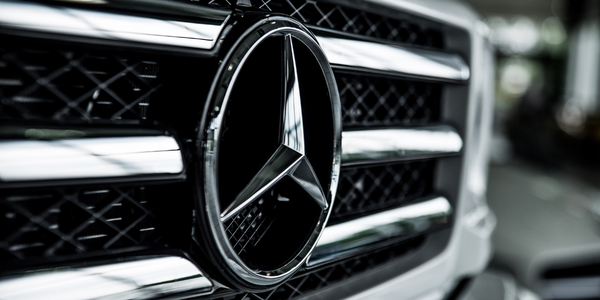
Case Study
Integral Plant Maintenance
Mercedes-Benz and his partner GAZ chose Siemens to be its maintenance partner at a new engine plant in Yaroslavl, Russia. The new plant offers a capacity to manufacture diesel engines for the Russian market, for locally produced Sprinter Classic. In addition to engines for the local market, the Yaroslavl plant will also produce spare parts. Mercedes-Benz Russia and his partner needed a service partner in order to ensure the operation of these lines in a maintenance partnership arrangement. The challenges included coordinating the entire maintenance management operation, in particular inspections, corrective and predictive maintenance activities, and the optimizing spare parts management. Siemens developed a customized maintenance solution that includes all electronic and mechanical maintenance activities (Integral Plant Maintenance).
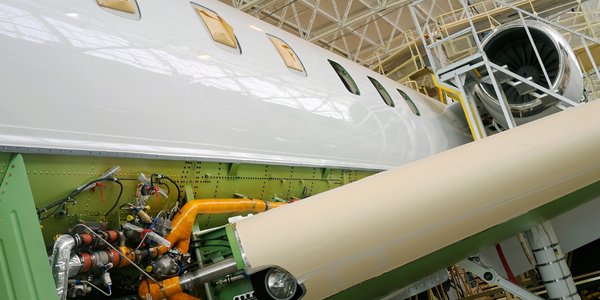
Case Study
Aerospace & Defense Case Study Airbus
For the development of its new wide-body aircraft, Airbus needed to ensure quality and consistency across all internal and external stakeholders. Airbus had many challenges including a very aggressive development schedule and the need to ramp up production quickly to satisfy their delivery commitments. The lack of communication extended design time and introduced errors that drove up costs.