Customer Company Size
Large Corporate
Region
- Europe
Country
- Italy
Product
- AVEVA’s Monitoring and Control
- AVEVA’s AR/VR platforms
- System Platform
- InTouch HMI
Tech Stack
- Microsoft .Net
- SQL Server
- Azure
- Microsoft Visual Studio
- DirectX
- Windows API
Implementation Scale
- Enterprise-wide Deployment
Impact Metrics
- Productivity Improvements
- Innovation Output
Technology Category
- Platform as a Service (PaaS) - Connectivity Platforms
Applicable Industries
- Automotive
Applicable Functions
- Discrete Manufacturing
- Maintenance
Use Cases
- Predictive Maintenance
- Machine Condition Monitoring
- Remote Asset Management
- Virtual Training
Services
- Cloud Planning, Design & Implementation Services
- Software Design & Engineering Services
- System Integration
About The Customer
Italpresse Gauss is a company based in Capriano del Colle, Italy. They build machines and automatic work cells for light alloy casting primarily for the global automotive industry. The company focuses on excellence, technological innovation, quality, and production flexibility. Italpresse Gauss is committed to increasing its leadership position and worldwide presence by providing cutting-edge technological solutions. To stay ahead of Industry 4.0., Italpresse Gauss looked to the AVEVA portfolio to develop both “HMe”, a custom HMI with advanced data management and diagnostics capabilities; and “AMe”, a powerful AR application for live remote maintenance and service assistance.
The Challenge
Italpresse Gauss, a company that builds machines and automatic work cells for light alloy casting primarily for the global automotive industry, was looking to develop a custom HMI that operates with other OEM devices and software platforms. They also wanted to incorporate AR/VR technologies as an asset performance and remote support tool to support the company’s leadership position in Industrie 4.0. The challenges they faced included introducing Industrie 4.0 technologies to a traditional aluminum foundry industry, leveraging breakthrough AR/VR technology to pilot new asset performance management and operator training solutions, and delivering new concepts to market on an aggressive timeline.
The Solution
Italpresse Gauss used AVEVA’s Monitoring and Control and AR/VR platforms to develop a custom HMI and a first-of-its-kind remote maintenance solution. Using System Platform and InTouch–both based on Microsoft .Net, SQL Server and Azure– Italpresse Gauss developed a custom monitoring and control interface they coined “HMe”. This open interface architecture communicates with other devices, automatically collects data on a local SQL server database within the application, reduces operator complexity, and improves situational awareness. They also developed “AMe”, a powerful AR application for live remote maintenance and service assistance, built using AVEVA’s AR/VR solution–a powerful toolset based on Microsoft Visual Studio, DirectX and the Windows API.
Operational Impact
Quantitative Benefit
Case Study missing?
Start adding your own!
Register with your work email and create a new case study profile for your business.
Related Case Studies.
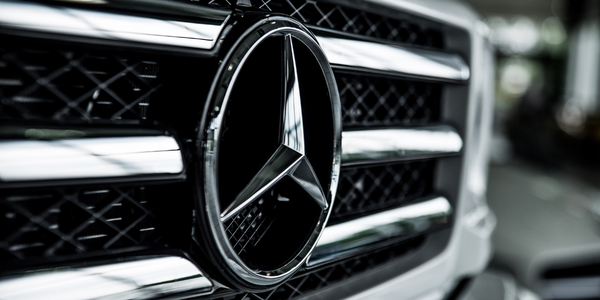
Case Study
Integral Plant Maintenance
Mercedes-Benz and his partner GAZ chose Siemens to be its maintenance partner at a new engine plant in Yaroslavl, Russia. The new plant offers a capacity to manufacture diesel engines for the Russian market, for locally produced Sprinter Classic. In addition to engines for the local market, the Yaroslavl plant will also produce spare parts. Mercedes-Benz Russia and his partner needed a service partner in order to ensure the operation of these lines in a maintenance partnership arrangement. The challenges included coordinating the entire maintenance management operation, in particular inspections, corrective and predictive maintenance activities, and the optimizing spare parts management. Siemens developed a customized maintenance solution that includes all electronic and mechanical maintenance activities (Integral Plant Maintenance).

Case Study
Monitoring of Pressure Pumps in Automotive Industry
A large German/American producer of auto parts uses high-pressure pumps to deburr machined parts as a part of its production and quality check process. They decided to monitor these pumps to make sure they work properly and that they can see any indications leading to a potential failure before it affects their process.