Customer Company Size
Large Corporate
Region
- Asia
Country
- Singapore
Product
- EcoStruxure Power
- EcoStruxure Building
- EcoStruxure Building Advisor
- EcoStruxure Power Advisor
- EcoStruxure Asset Advisor
Tech Stack
- IoT
- Data Analytics
- Remote Monitoring
- Cloud
Implementation Scale
- Enterprise-wide Deployment
Impact Metrics
- Environmental Impact Reduction
- Energy Saving
- Cost Savings
Technology Category
- Platform as a Service (PaaS) - Connectivity Platforms
- Analytics & Modeling - Real Time Analytics
Applicable Functions
- Facility Management
- Maintenance
Use Cases
- Building Automation & Control
- Building Energy Management
- Predictive Maintenance
- Remote Asset Management
Services
- System Integration
- Cloud Planning, Design & Implementation Services
About The Customer
Bolloré Logistics is a French logistics and transport company with a strong commitment to sustainability. The company rolled out its 'Powering Sustainable Logistics' program in 2018 as part of its efforts to promote sustainable global trade and growth. The program aims to reduce the environmental impact of Bolloré Logistics’ activities. As part of this initiative, Bolloré Logistics built the Blue Hub, a 540,000 sq ft building in Jurong, Singapore. The Blue Hub is not only Bolloré Logistics’ first Asia-Pacific smart warehouse, but is also an icon of new-generation sustainable architecture. The building is equipped with an advanced energy management system and other eco-friendly features such as a storm-water recycling system, energy and water consumption monitoring. The building is monitored in real-time using 300 smart sensors which are scattered across the warehouse.
The Challenge
Bolloré Logistics, a French logistics giant, is a strong advocate for sustainability and has rolled out its 'Powering Sustainable Logistics' program in 2018. The program aims to reduce the environmental impact of Bolloré Logistics’ activities. As part of this initiative, Bolloré Logistics built the Blue Hub, a green building equipped with an advanced energy management system and other eco-friendly features. However, achieving tangible sustainability benchmarks required to obtain environmental certifications such as Green Mark & LEED was a challenge. The company needed a solution that would help them reduce their carbon footprint and make their operations more energy-efficient.
With the effects of global warming felt worldwide, companies around the globe have been trying their best to reduce their carbon footprint. The logistics industry has also followed suit, environmentally friendly packaging and carbon emission reduction of freight shipping are the many ways employed as part of its efforts to go green. Bolloré Logistics wanted to go the extra mile by ensuring that Blue Hub is energy-efficient.
The Solution
Bolloré Logistics adopted Schneider Electric’s EcoStruxure Power and EcoStruxure Building technologies to make Blue Hub energy-efficient. These technologies keep the building systems working optimally while also keeping operation and maintenance costs to a minimum. Using Schneider Electric’s EcoStruxure Building Advisor, Bolloré Logistics is able to optimise their power consumption levels through the aid of system suggestions and insightful visualisation of collected data, and remote management of AHU over the weekends.
Aside from employing the Building Advisor service to keep Blue Hub running smoothly, Bolloré Logistics is also using Schneider Electric’s Power Advisor service. The service enables remote monitoring of every connected asset and helps Bolloré Logistics visualise their energy consumption patterns across a variety of parameters. With this information, the facility management team can easily spot an asset that is spiking in its energy consumption which often signals a need for inspection and possible preventive maintenance. EcoStruxure Asset Advisor provides online condition monitoring to identify abnormalities in electrical devices (using sensors) to prevent impending failures and reduce unscheduled downtime due to electrical process failure.
Aside from employing the Building Advisor service to keep Blue Hub running smoothly, Bolloré Logistics is also using Schneider Electric’s Power Advisor service. The service enables remote monitoring of every connected asset and helps Bolloré Logistics visualise their energy consumption patterns across a variety of parameters. With this information, the facility management team can easily spot an asset that is spiking in its energy consumption which often signals a need for inspection and possible preventive maintenance. EcoStruxure Asset Advisor provides online condition monitoring to identify abnormalities in electrical devices (using sensors) to prevent impending failures and reduce unscheduled downtime due to electrical process failure.
Operational Impact
Case Study missing?
Start adding your own!
Register with your work email and create a new case study profile for your business.
Related Case Studies.
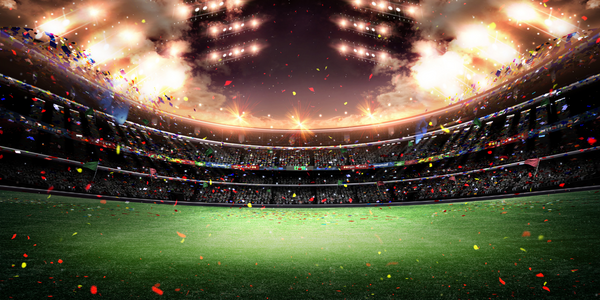
Case Study
Turning A Stadium Into A Smart Building
Honeywell created what it called the “intelligent system” for the National Stadium in Beijing, China, turning the venue for the opening and closing events at the 2008 Summer Olympics into a “smart building.” Designed by highly controversial artist Ai Weiwei, the “Bird’s Nest” remains one of the most impressive feats of stadium architecture in the world. The 250,000 square meter structure housed more than 100,000 athletes and spectators at a time. To accommodate such capacity, China turned to Honeywell’s EBI Integrated Building Management System to create an integrated “intelligent system” for improved building security, safety and energy efficiency.
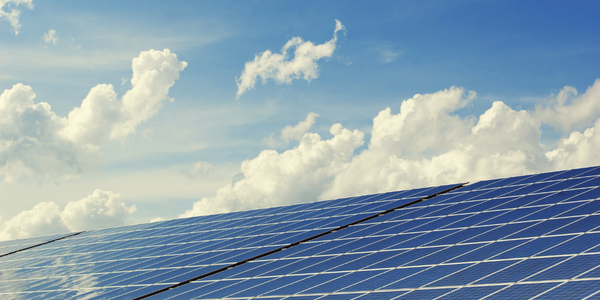
Case Study
Remote Monitoring & Predictive Maintenance App for a Solar Energy System
The maintenance & tracking of various modules was an overhead for the customer due to the huge labor costs involved. Being an advanced solar solutions provider, they wanted to ensure early detection of issues and provide the best-in-class customer experience. Hence they wanted to automate the whole process.
.png)
Case Study
Improving Vending Machine Profitability with the Internet of Things (IoT)
The vending industry is undergoing a sea change, taking advantage of new technologies to go beyond just delivering snacks to creating a new retail location. Intelligent vending machines can be found in many public locations as well as company facilities, selling different types of goods and services, including even computer accessories, gold bars, tickets, and office supplies. With increasing sophistication, they may also provide time- and location-based data pertaining to sales, inventory, and customer preferences. But at the end of the day, vending machine operators know greater profitability is driven by higher sales and lower operating costs.
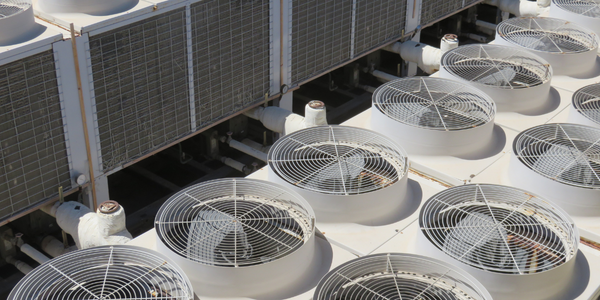
Case Study
Predictive Maintenance for Industrial Chillers
For global leaders in the industrial chiller manufacturing, reliability of the entire production process is of the utmost importance. Chillers are refrigeration systems that produce ice water to provide cooling for a process or industrial application. One of those leaders sought a way to respond to asset performance issues, even before they occur. The intelligence to guarantee maximum reliability of cooling devices is embedded (pre-alarming). A pre-alarming phase means that the cooling device still works, but symptoms may appear, telling manufacturers that a failure is likely to occur in the near future. Chillers who are not internet connected at that moment, provide little insight in this pre-alarming phase.