Customer Company Size
Large Corporate
Region
- America
Country
- United States
Product
- Samsara Dash Cams
- Samsara Vehicle Gateways
- Samsara Real-Time GPS Tracking
Tech Stack
- Real-Time GPS
- WiFi Hotspot
- Open API
Implementation Scale
- Enterprise-wide Deployment
Impact Metrics
- Cost Savings
- Customer Satisfaction
- Employee Satisfaction
- Productivity Improvements
Technology Category
- Analytics & Modeling - Predictive Analytics
- Analytics & Modeling - Real Time Analytics
- Sensors - GPS
Applicable Industries
- Construction & Infrastructure
- Oil & Gas
Applicable Functions
- Field Services
- Logistics & Transportation
- Maintenance
Use Cases
- Fleet Management
- Geofencing
- Predictive Maintenance
- Remote Asset Management
- Vehicle Telematics
Services
- Software Design & Engineering Services
- System Integration
- Training
About The Customer
KS Industries (KSI) is a nationwide oil and gas piping construction company that provides engineering, fabrication, maintenance, and construction services for oil and gas producers. Operating at a massive scale, KSI manages over 1,200 vehicles and 1,000 drivers across six of the largest energy-producing states in the United States, including California, Colorado, New Mexico, Texas, Wyoming, and North Dakota. The company builds and maintains oil and gas facilities for major clients like Chevron and Hess Corporation. Given the hazardous nature of the oil and gas and construction industries, KSI prioritizes safety above all else. The safety department, led by Phillip Clarke, Director of Safety and Risk Management, is tasked with ensuring the safety of KSI's crews in the field.
The Challenge
KS Industries (KSI) operates across six major energy-producing states in the United States, managing over 1,200 vehicles and 1,000 drivers. The company needed to enhance safety and visibility for its crews working in remote and hazardous oil fields. The previous system had limitations, including a 100-vehicle cap on live map visibility and connectivity issues in the field. These challenges made it difficult to monitor real-time GPS locations, track crews for rescues, and ensure safety compliance. Additionally, the lack of connectivity hindered productivity, causing delays in processing critical paperwork like Standard Operating Procedures (SOPs) and safety audits.
The Solution
To address these challenges, KSI implemented Samsara's dash cams and real-time GPS tracking system. The new system provided a single dashboard to view all vehicles across different geographies, improving visibility and saving time. The real-time GPS data allowed safety supervisors to monitor the fields effectively, ensuring they spent sufficient time in the field. The system also enabled geofencing of job sites to track supervisor activities. Additionally, Samsara's WiFi hotspot feature provided reliable connectivity, allowing teams to send SOPs and audits back to HQ from the field. This reduced cellular bills and enabled real-time access to safety metrics. The Samsara platform also facilitated faster video retrieval and smarter coaching with AI dash cams, allowing Clarke's team to review footage the same day and spot-check for safe driving behaviors. This proactive monitoring helped in coaching drivers on safe driving techniques, thereby reducing accidents.
Operational Impact
Quantitative Benefit
Case Study missing?
Start adding your own!
Register with your work email and create a new case study profile for your business.
Related Case Studies.
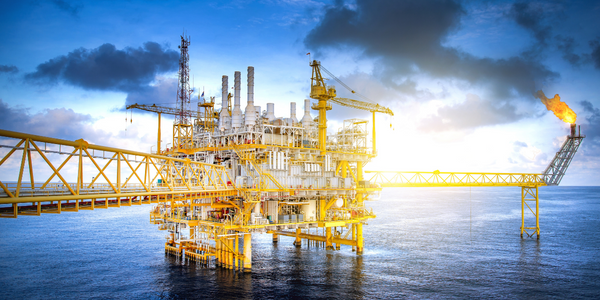
Case Study
Taking Oil and Gas Exploration to the Next Level
DownUnder GeoSolutions (DUG) wanted to increase computing performance by 5 to 10 times to improve seismic processing. The solution must build on current architecture software investments without sacrificing existing software and scale computing without scaling IT infrastructure costs.
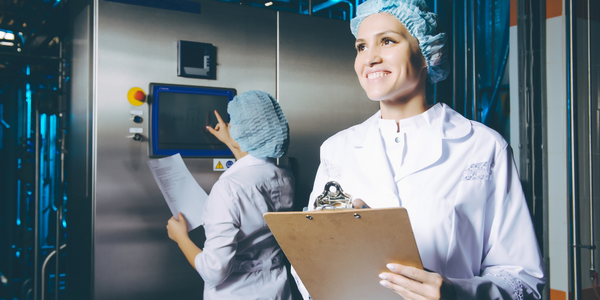
Case Study
Remote Wellhead Monitoring
Each wellhead was equipped with various sensors and meters that needed to be monitored and controlled from a central HMI, often miles away from the assets in the field. Redundant solar and wind generators were installed at each wellhead to support the electrical needs of the pumpstations, temperature meters, cameras, and cellular modules. In addition to asset management and remote control capabilities, data logging for remote surveillance and alarm notifications was a key demand from the customer. Terra Ferma’s solution needed to be power efficient, reliable, and capable of supporting high-bandwidth data-feeds. They needed a multi-link cellular connection to a central server that sustained reliable and redundant monitoring and control of flow meters, temperature sensors, power supply, and event-logging; including video and image files. This open-standard network needed to interface with the existing SCADA and proprietary network management software.
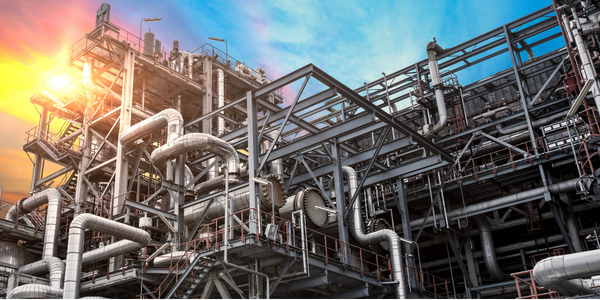
Case Study
Refinery Saves Over $700,000 with Smart Wireless
One of the largest petroleum refineries in the world is equipped to refine various types of crude oil and manufacture various grades of fuel from motor gasoline to Aviation Turbine Fuel. Due to wear and tear, eight hydrogen valves in each refinery were leaking, and each cost $1800 per ton of hydrogen vented. The plant also had leakage on nearly 30 flare control hydrocarbon valves. The refinery wanted a continuous, online monitoring system that could catch leaks early, minimize hydrogen and hydrocarbon production losses, and improve safety for maintenance.
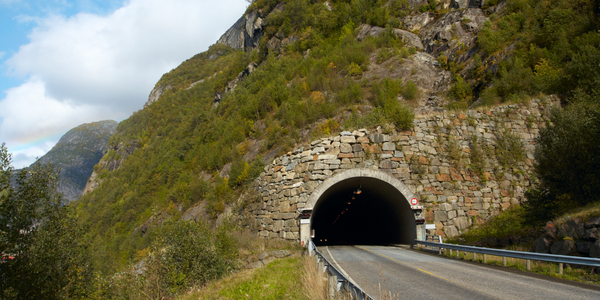
Case Study
IoT System for Tunnel Construction
The Zenitaka Corporation ('Zenitaka') has two major business areas: its architectural business focuses on structures such as government buildings, office buildings, and commercial facilities, while its civil engineering business is targeted at structures such as tunnels, bridges and dams. Within these areas, there presented two issues that have always persisted in regard to the construction of mountain tunnels. These issues are 'improving safety" and "reducing energy consumption". Mountain tunnels construction requires a massive amount of electricity. This is because there are many kinds of electrical equipment being used day and night, including construction machinery, construction lighting, and ventilating fan. Despite this, the amount of power consumption is generally not tightly managed. In many cases, the exact amount of power consumption is only ascertained when the bill from the power company becomes available. Sometimes, corporations install demand-monitoring equipment to help curb the maximum power demanded. However, even in these cases, the devices only allow the total volume of power consumption to be ascertained, or they may issue warnings to prevent the contracted volume of power from being exceeded. In order to tackle the issue of reducing power consumption, it was first necessary to obtain an accurate breakdown of how much power was being used in each particular area. In other words, we needed to be able to visualize the amount of power being consumed. Safety, was also not being managed very rigorously. Even now, tunnel construction sites often use a 'name label' system for managing entry into the work site. Specifically, red labels with white reverse sides that bear the workers' names on both sides are displayed at the tunnel work site entrance. The workers themselves then flip the name label to the appropriate side when entering or exiting from the work site to indicate whether or not they are working inside the tunnel at any given time. If a worker forgets to flip his or her name label when entering or exiting from the tunnel, management cannot be performed effectively. In order to tackle the challenges mentioned above, Zenitaka decided to build a system that could improve the safety of tunnel construction as well as reduce the amount of power consumed. In other words, this new system would facilitate a clear picture of which workers were working in each location at the mountain tunnel construction site, as well as which processes were being carried out at those respective locations at any given time. The system would maintain the safety of all workers while also carefully controlling the electrical equipment to reduce unnecessary power consumption. Having decided on the concept, our next concern was whether there existed any kind of robust hardware that would not break down at the construction work site, that could move freely in response to changes in the working environment, and that could accurately detect workers and vehicles using radio frequency identification (RFID). Given that this system would involve many components that were new to Zenitaka, we decided to enlist the cooperation of E.I.Sol Co., Ltd. ('E.I.Sol') as our joint development partner, as they had provided us with a highly practical proposal.