Customer Company Size
Large Corporate
Region
- Asia
Country
- China
Product
- Lenovo ThinkPad X300
- Lenovo ThinkPad T400
- Abaqus FEA software
Tech Stack
- Finite Element Analysis (FEA)
- Computational Fluid Dynamics
Implementation Scale
- Enterprise-wide Deployment
Impact Metrics
- Productivity Improvements
- Innovation Output
Technology Category
- Analytics & Modeling - Digital Twin / Simulation
Applicable Industries
- Electronics
Applicable Functions
- Product Research & Development
Use Cases
- Digital Twin
- Virtual Prototyping & Product Testing
Services
- Software Design & Engineering Services
About The Customer
Lenovo is a multinational technology company that designs, develops, manufactures, and sells personal computers, tablet computers, smartphones, workstations, servers, electronic storage devices, IT management software, and smart televisions. The company is known for its ThinkPad line of laptops, which are widely recognized for their performance, durability, and aesthetics. Lenovo's Innovation Design Center (IDC) in Beijing is responsible for analyzing all of Lenovo’s products, ranging from PCs and notebooks to cell phones and servers. The IDC has received numerous awards for its design excellence.
The Challenge
Lenovo's ThinkPad line of laptops is known for its aesthetics and durability. However, the challenge lies in ensuring that the laptops are not only portable but also durable. The laptops face demanding loads and forces even when they’re just being carried from place to place. It’s important for the covers to be stiff enough, with minimal deformation, so that the rear cover will protect the display, while the base cover protects the motherboard. Another challenge was to reduce the thickness of the keyboard assembly without losing the traditional keystroke feel.
The Solution
Lenovo uses SIMULIA’s Abaqus FEA software to design out flex, engineer in stiffness, and improve keystroke feel. The software is used early in the design process to verify product strength, choose between different versions, and identify and improve problem areas. The process involves pre-processing from CAD to meshed model; establishing loads, boundaries, and part interactions; running the analysis; and creating the reports. For the keyboard design, engineers simulated the effects of keystroke pressure on the original dome-shaped rubber spring to confirm that the feel remained the same from the old keyboard to the new. The nonlinear simulation enabled the engineers to establish values for how far the rubber dome traveled downward as keystroke force increased.
Operational Impact
Quantitative Benefit
Case Study missing?
Start adding your own!
Register with your work email and create a new case study profile for your business.
Related Case Studies.
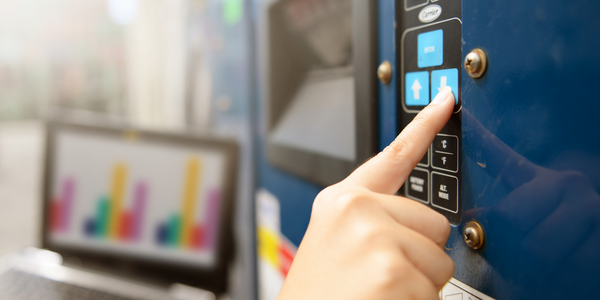
Case Study
Remote Temperature Monitoring of Perishable Goods Saves Money
RMONI was facing temperature monitoring challenges in a cold chain business. A cold chain must be established and maintained to ensure goods have been properly refrigerated during every step of the process, making temperature monitoring a critical business function. Manual registration practice can be very costly, labor intensive and prone to mistakes.
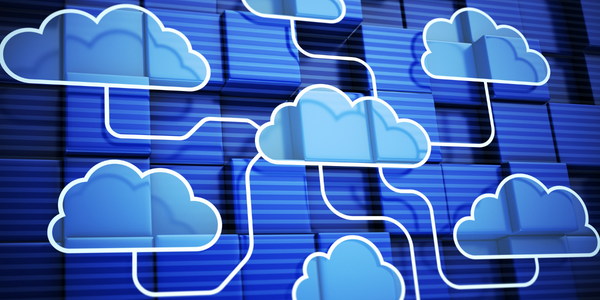
Case Study
Cloud Solution for Energy Management Platform-Schneider Electric
Schneider Electric required a cloud solution for its energy management platform to manage high computational operations, which were essential for catering to client requirements. As the business involves storage and analysis of huge amounts of data, the company also needed a convenient and scalable storage solution to facilitate operations efficiently.
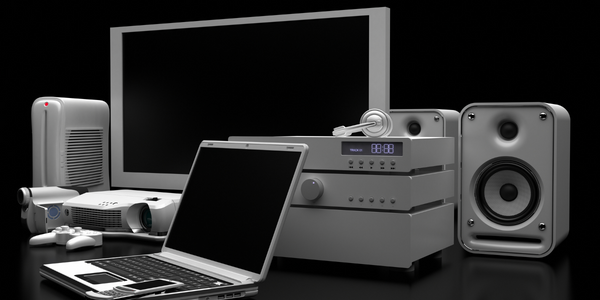
Case Study
Leveraging the IoT to Gain a Competitive Edge in International Competition
Many large manufacturers in and outside Japan are competing for larger market share in the same space, expecting a growing demand for projectors in the areas of entertainment, which requires glamor and strong visual performance as well as digital signage that can attract people’s attention. “It is becoming more and more difficult to differentiate ourselves with stand-alone hardware products,” says Kazuyuki Kitagawa, Director of Service & Support at Panasonic AVC Networks. “In order for Panasonic to grow market share and overall business, it is essential for us to develop solutions that deliver significant added value.” Panasonic believes projection failure and quality deterioration should never happen. This is what and has driven them to make their projectors IoT-enabled. More specifically, Panasonic has developed a system that collects data from projectors, visualizes detailed operational statuses, and predicts issues and address them before failure occurs. Their projectors are embedded with a variety of sensors that measure power supply, voltage, video input/ output signals, intake/exhaust air temperatures, cooling fan operations, and light bulb operating time. These sensors have been used to make the projector more intelligent, automatically suspending operation when the temperature rises excessively, and automatically switching light bulbs. Although this was a great first step, Panasonic projectors were still not equipped with any capability to send the data over a network.