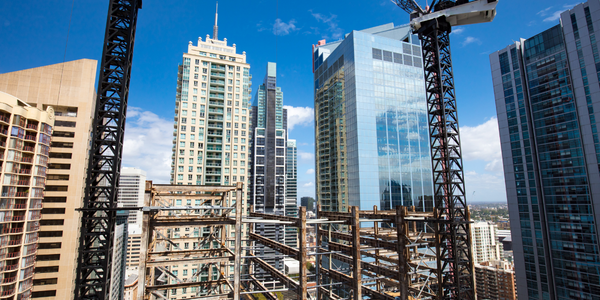
- Analytics & Modeling - Real Time Analytics
- Application Infrastructure & Middleware - Data Visualization
- Functional Applications - Enterprise Asset Management Systems (EAM)
- Buildings
- Discrete Manufacturing
- Machine Condition Monitoring
There’s always a sort of lag in the information we get from the ERP. It’s not real time, its not updated every second. We were able to see what happened yesterday, what happened last week but not what was happening right now, and we would always have to somehow fill that gap. Also, to get data into the ERP we were relying on a human being to accurately define and manually input the information to enter it into our database. All of the real-time monitoring systems that Carlson Products had seen were only dedicated to machining. They had chats with some of their equipment providers and the solutions they attempted to provide them with were not visually appealing, not web-based and felt quite rudimentary. They did attempt to do manual tracking before MachineMetrics, and they got so much junk data that they just stopped trying. They kept a Microsoft access database where employees would track this information themselves but with all the huge outliers, data it went to hell and a handbasket. The most important thing Carlson Products wanted was to look at was historical labor data information: whether or not the jobs were on target. Tracking down the supervisors and operators to understand why they weren’t on target was quite time consuming, not to mention most of their employees had difficulty remembering why problems had occurred when reviewing the issues reactively. There was no ability to identify systematic issues vs singular issues. Also, the lack of historical data made it difficult for them to calculate their utilization as well as their potential capacity.
MachineMetrics was their solution. Tablets were mounted to 15 individual machines to display job performance and provide operators with an interface that categorized downtime, setups, part rejections, and tool changes. Real-time dashboards were installed on large screen monitors across the facility to display the performance of jobs against the company’s production goals. Instant text notifications were set up so Production Managers could identify underperforming machines immediately and quickly address issues in real-time.
Case Study missing?
Start adding your own!
Register with your work email and create a new case study profile for your business.
Related Case Studies.
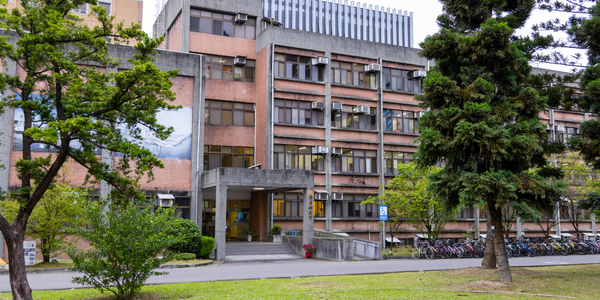
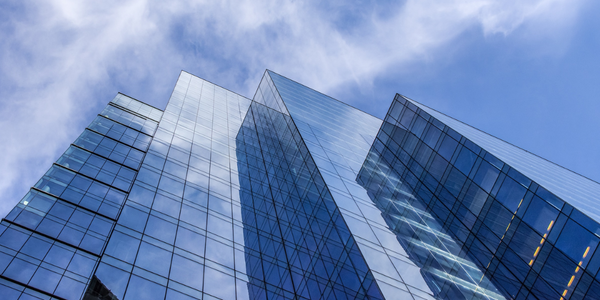
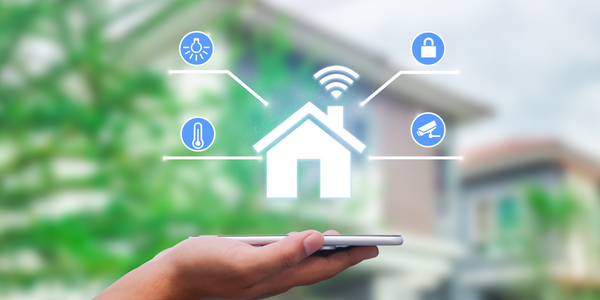

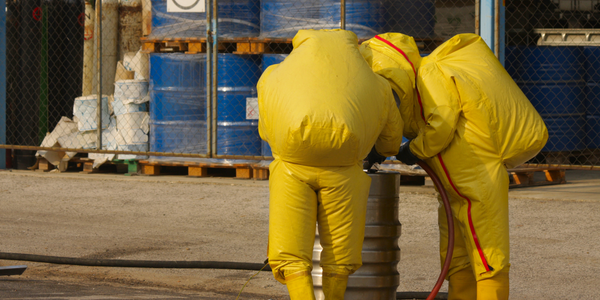