Technology Category
- Sensors - Haptic Sensors
- Sensors - Vibration Sensors
Applicable Industries
- Automotive
- Electronics
Applicable Functions
- Product Research & Development
Use Cases
- Predictive Maintenance
- Time Sensitive Networking
About The Customer
Trelleborg is a Swedish corporation with a 100-year history in engineering innovation. They specialize in creating molded rubber components that enhance the comfort and performance of vehicles. These components, which include brackets, bushings, and other chassis and power train components, are designed to absorb vibration and impact, providing a more pleasing experience for car owners. Trelleborg works closely with major automakers like GM, Ford, Chrysler, Honda, and Toyota to create custom polymer components. The design and finite element analysis (FEA) group at Trelleborg's Engineering Center in Michigan is a small but highly productive team that has greatly improved its throughput, cost-efficiency, and turnaround time by using PBS Professional.
The Challenge
Trelleborg, a Swedish corporation with a century-long history in engineering innovation, specializes in creating molded rubber components that enhance the comfort and performance of vehicles. The design and finite element analysis (FEA) group at Trelleborg's Engineering Center in Michigan, a small but highly productive team, was facing a significant challenge. They were trying to increase their throughput without adding more personnel or hardware. The team was attempting to utilize off-hour CPU cycles from the CAD workstations on an ad hoc basis. However, they were struggling with estimating how long each job would take on a specific machine so that another job could be set up to run behind it. The team needed a way to increase available CPU time to improve their productivity and efficiency.
The Solution
Trelleborg turned to Altair's PBS Professional to manage and harvest CPU cycles on six workstations. The team calculated the cost-effectiveness of using PBS Professional to manage CPU cycles from 6:00 pm to 6:00 am daily and on weekends. They estimated that PBS Professional would pay for itself in just two weekends by making idle CPU hours productive. After the installation of PBS Professional, the team experienced an immediate surge in productivity. Instead of running six jobs a night, they were soon averaging 10 or 20. Jobs were simply dumped into the queue, and PBS Professional assigned them to the first available CPU. Even if a workstation crashed, PBS Professional automatically sent the next job to the first available CPU, ensuring continuous productivity.
Operational Impact
Quantitative Benefit
Case Study missing?
Start adding your own!
Register with your work email and create a new case study profile for your business.
Related Case Studies.
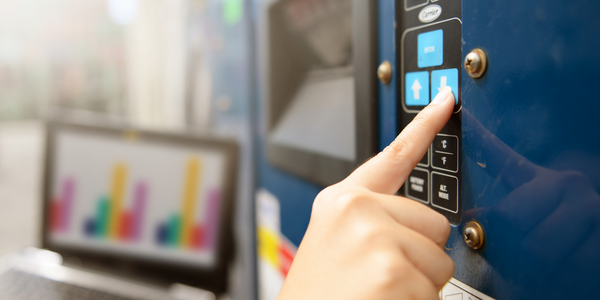
Case Study
Remote Temperature Monitoring of Perishable Goods Saves Money
RMONI was facing temperature monitoring challenges in a cold chain business. A cold chain must be established and maintained to ensure goods have been properly refrigerated during every step of the process, making temperature monitoring a critical business function. Manual registration practice can be very costly, labor intensive and prone to mistakes.
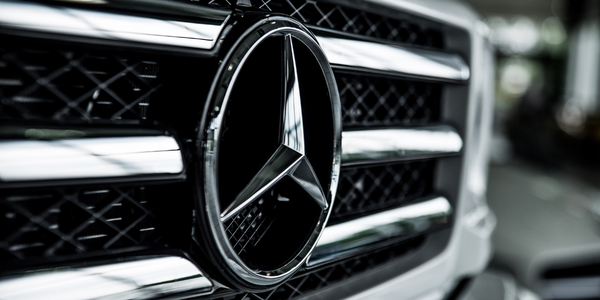
Case Study
Integral Plant Maintenance
Mercedes-Benz and his partner GAZ chose Siemens to be its maintenance partner at a new engine plant in Yaroslavl, Russia. The new plant offers a capacity to manufacture diesel engines for the Russian market, for locally produced Sprinter Classic. In addition to engines for the local market, the Yaroslavl plant will also produce spare parts. Mercedes-Benz Russia and his partner needed a service partner in order to ensure the operation of these lines in a maintenance partnership arrangement. The challenges included coordinating the entire maintenance management operation, in particular inspections, corrective and predictive maintenance activities, and the optimizing spare parts management. Siemens developed a customized maintenance solution that includes all electronic and mechanical maintenance activities (Integral Plant Maintenance).