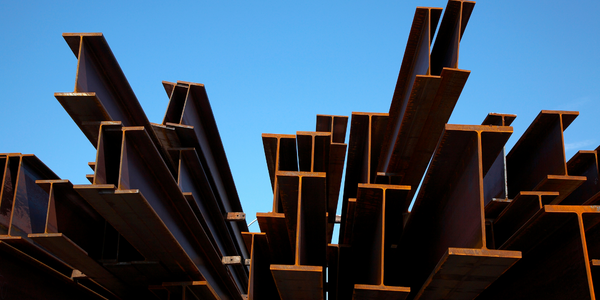
- Functional Applications - Remote Monitoring & Control Systems
- Networks & Connectivity - RFID
- Wearables - Tags & Patches
- Metals
- Logistics & Transportation
- Supply Chain Visibility
Until 2007, the Kerschgens Group handled the processes that involve moving goods into and out of stock like many companies in the industry. The daily work of the logistics personnel was characterised by delivery lists and slips of paper. However, the market is changing, and so are the requirements. Whereas the company used to sell mainly standard products, the need arose to put together orders made up from many different individual parts. And working with lots of bits of paper frequently led to time being spent on searching and errors with goods movements. A new concept had to be developed to optimise the process
The solution came in the form of using GRAPHIPLAST® combination labels which are used as the data carriers. Tagging the steel rods with these labels as opposed to tiny bits of paper completely modernized the Kerschgens operations in terms of how goods were transported and dispatched to, from and around the warehouse.
Case Study missing?
Start adding your own!
Register with your work email and create a new case study profile for your business.
Related Case Studies.
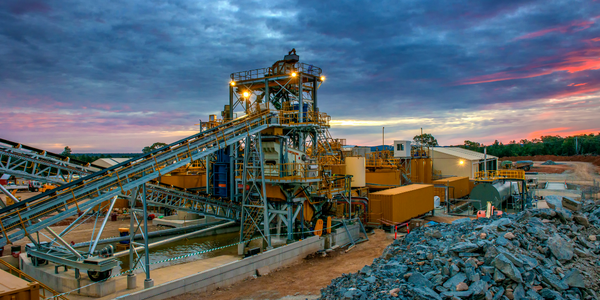

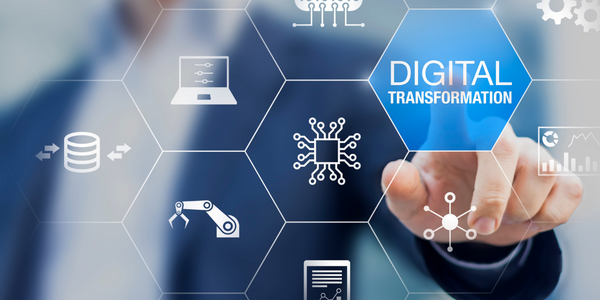
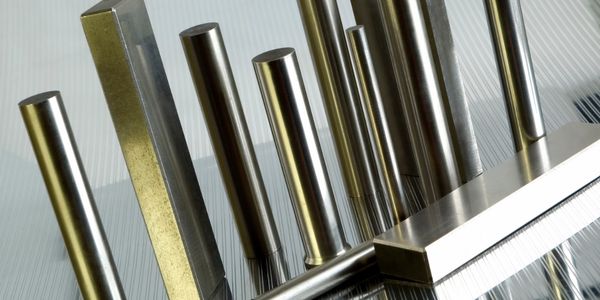
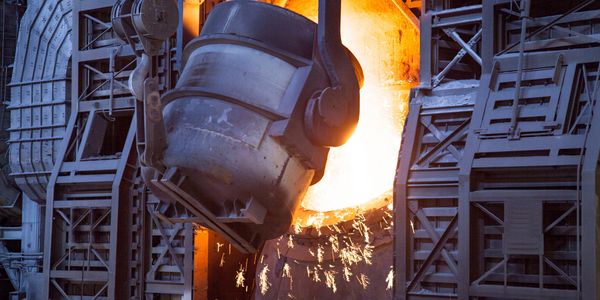
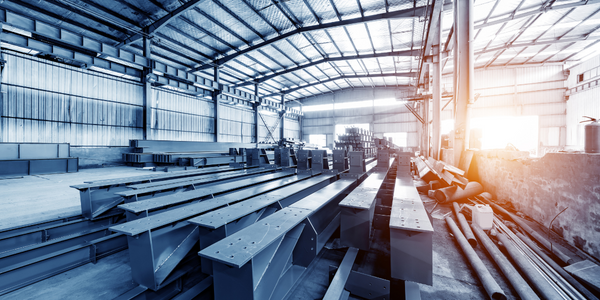