Customer Company Size
Large Corporate
Region
- Europe
Country
- Russia
Product
- AVEVA Everything 3D (E3D)
- AVEVA Bocad
- AVEVA Engineering
- AVEVA Diagrams
- AVEVA Instrumentation
- AVEVA Electrical
Tech Stack
- 3D Design Software
- Data Management Tool
- Laser Scanning Technology
Implementation Scale
- Enterprise-wide Deployment
Impact Metrics
- Productivity Improvements
- Cost Savings
- Customer Satisfaction
Technology Category
- Application Infrastructure & Middleware - Data Exchange & Integration
Applicable Industries
- Chemicals
Applicable Functions
- Discrete Manufacturing
- Procurement
Use Cases
- Predictive Maintenance
- Process Control & Optimization
Services
- Software Design & Engineering Services
- System Integration
About The Customer
NIIK is a leading engineering company in Russia and former Soviet Union countries, with vast experience in grass-root construction and the revamp of urea plants. The company offers a full range of engineering services, based on its 65 years of experience. These services include laboratory tests, pilot studies, feasibility studies, and the development of Engineering & Design documentation in the field of urea and urea-based fertilisers, as well as detailed engineering for downstream products such as melamine and relative compounds. NIIK possesses vast experience in the field of engineering and design, yet the company is as eager as ever to implement innovative technologies to improve and continue development. The goal is not just to undertake a large number of projects, but to organise processes so that these projects are carried out as effectively as possible.
The Challenge
NIIK, a leading engineering company in Russia, was facing challenges in improving change management across departments and growing visibility of processes at the design supervision stage. Each change in a project required collaboration and coordination across multiple teams and disciplines. The existing working standards were failing to support the company’s ambitious goals and were not fit for purpose for a 21st-century industry leader. The process of updating new information from different design departments was holding up progress and pushing back delivery dates. There were misunderstandings between the design and procurement functions, leading to lost time, impacts on the bottom line, and implications for safety.
The Solution
To solve the challenges, a common information platform was introduced, both in IT and in ways of operating. Here, updates are communicated automatically instead of being tracked manually. NIIK now has a valuable commodity which provides the right information to the right people at the right time, helping its staff to make informed decisions as they carry out Engineering & Design work. By managing and incorporating changes during the design and construction process, it is now possible to monitor and control progress at all stages. This major improvement also has an effect on operators, who have more confidence now that their partnership is predictable and their plans reliable. Because they have one common information platform they are in control from the CAPEX phase right through to operations, since processes are transparent and change is seamless. For NIIK this is especially beneficial at the design supervision stage. Executing capital projects is now straightforward, because at the heart of each challenge NIIK now has the ability to make the right decisions at the right time.
Operational Impact
Quantitative Benefit
Case Study missing?
Start adding your own!
Register with your work email and create a new case study profile for your business.
Related Case Studies.
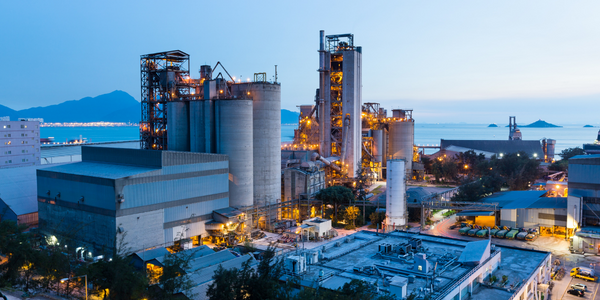
Case Study
Honeywell - Tata Chemicals Improves Data Accessibility with OneWireless
Tata was facing data accessibility challenges in the cement plant control room tapping signals from remote process control areas and other distant locations, including the gas scrubber. Tata needed a wireless solution to extend its control network securely to remote locations that would also provide seamless communication with existing control applications.

Case Study
Advanced Elastomer Systems Upgrades Production
In order to maintain its share of the international market for thermoplastic elastomers AES recently expanded its Florida plant by adding a new production line. While the existing lines were operating satisfactorily using a PROVOX distributed control system with traditional analog I/O, AES wanted advanced technology on the new line for greater economy, efficiency, and reliability. AES officials were anxious to get this line into production to meet incoming orders, but two hurricanes slowed construction.
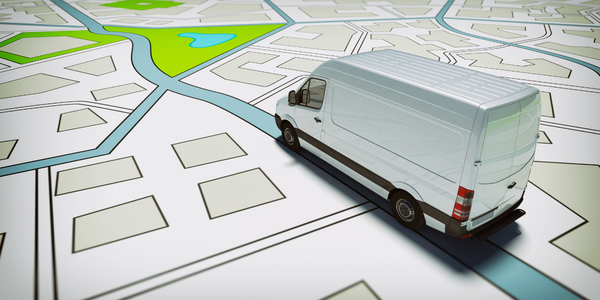
Case Study
Wireless GPS Tracking & Security Monitoring
Enhancing the security of hazardous freight and ensuring compliance with Homeland Security’s Transportation Security Administration mandate that all trains carrying chemicals capable of creating a toxic inhalation condition are equipped with on-board safety monitoring systems.

Case Study
Field Device Asset Management For Chemical Company in China
Chinese chemical subsidiary of multinational corporation serves customers throughout the world. Sales offices and research and technology centers are strategically located to provide rapid response to customer requests. Just two workers were assigned to maintain thousands of intelligent instruments in three production units, so they could do little more than react to device issues as they appeared. This costly maintenance method inevitably led to unexpected downtime when a critical instrument failed. Plant management recognized the need to change from reactive to predictive maintenance for all assets, including instruments and control valves, but help was needed in implementing such a technology-based initiative.
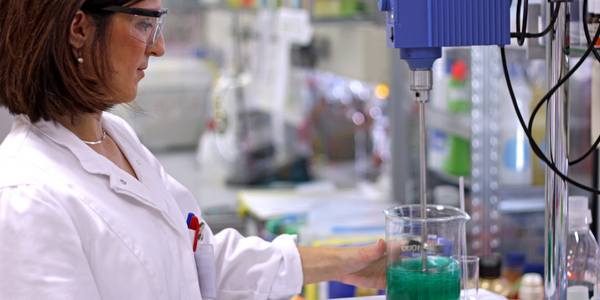
Case Study
Industrial Workforce Mobility for Improved Safety & Operations
Huntsman Corporation, a global manufacturer and marketer of differentiated chemicals, undertook an aggressive program to eliminate injuries, product defects, and environmental releases at their Port Neches facility. Termed “Project Zero”, this program required a completely mobile solution to empower operations and maintenance personnel to capture defects, track work progress and make process and safety related decisions in real-time.