Customer Company Size
Large Corporate
Region
- Asia
Country
- Japan
Product
- Welded Metal Bellows
- Ultra-high vacuum valves
- Wafer processing equipment
- Single-crystal grower
- Gyroscopes
Tech Stack
- ANSYS software
- ANSYS Parametric Design Language (APDL)
Implementation Scale
- Enterprise-wide Deployment
Impact Metrics
- Productivity Improvements
- Innovation Output
Technology Category
- Analytics & Modeling - Digital Twin / Simulation
Applicable Industries
- Electronics
- Aerospace
Applicable Functions
- Product Research & Development
- Quality Assurance
Use Cases
- Predictive Maintenance
- Digital Twin
Services
- Software Design & Engineering Services
About The Customer
Nippon Valqua Industries is a leading manufacturer of industrial packing and gaskets based in Japan. The company produces a wide range of products including rubber, fiber products, high-performance resins, and metal packing. One of their key products is the “welded metal bellows,” which consists of an accordion-folded frame formed with elaborate metal disks cut out of corrugated plates. The inner and outer edges of these plates are alternately welded, giving the bellows their elastic and airtight features. These bellows are used in a variety of applications, including as seals for ultra-high vacuum valves in the semiconductor industry, wafer processing equipment, single-crystal growers, as well as gyroscopes, accumulators, and dampers used in aerospace vehicles.
The Challenge
Nippon Valqua Industries, a leading manufacturer of industrial packing and gaskets, faced the challenge of extending the service life of weld bellows. The bellows consist of an accordion-folded frame formed with elaborate metal disks cut out of corrugated plates, of which the inner and outer edges are alternately welded. The welded bellows have elastic and airtight features and are applied for seal application, such as ultra-high vacuum valves for the semiconductor industry, wafer processing equipment and single-crystal grower, as well as gyroscopes, accumulator and dampers used for aerospace vehicles. To extend the service life, it was critical to optimize the shape of corrugated plates comprising welded parts. For the design of welded bellows that receive concentrated reaction force on/around welded parts, it was critical to create a corrugated plate best suited to disperse such concentrated reaction force.
The Solution
Nippon Valqua created a model of corrugated plate having three crests from the entire bellows model as an axial-symmetric model to be analyzed. To this analysis, it applied the optimization method using parameter design. At this stage, Nippon Valqua parameterized circular arcs and other factors that specify the corrugation shape of corrugated plates. Subsequently it performed analyses using ANSYS software. For this analysis, a series of processes —from changing model shapes using parameters to storing analyzed results —were automated using ANSYS Parametric Design Language (APDL). Considering the fact that most breakage of bellows occurs on/around welded portions, Nippon Valqua explored possible causes of the increase in the Von Mises stress based on obtained results of analyses. As a result, it could find a parameter exerting significant effects upon the increase in stress from among those causes.
Operational Impact
Quantitative Benefit
Case Study missing?
Start adding your own!
Register with your work email and create a new case study profile for your business.
Related Case Studies.
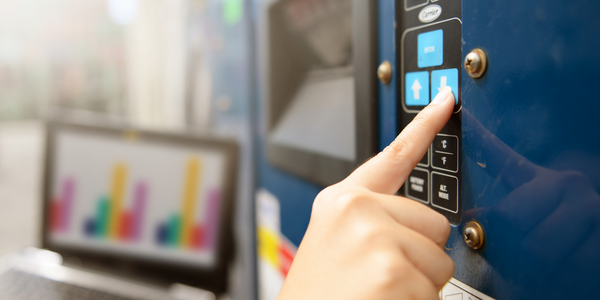
Case Study
Remote Temperature Monitoring of Perishable Goods Saves Money
RMONI was facing temperature monitoring challenges in a cold chain business. A cold chain must be established and maintained to ensure goods have been properly refrigerated during every step of the process, making temperature monitoring a critical business function. Manual registration practice can be very costly, labor intensive and prone to mistakes.
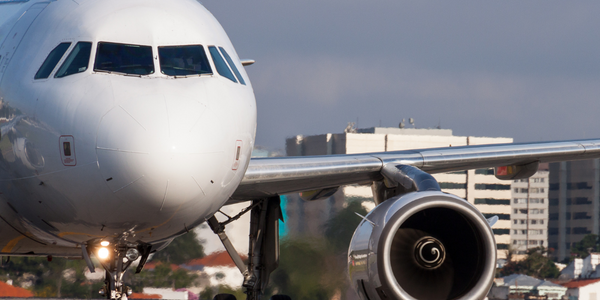
Case Study
Airbus Soars with Wearable Technology
Building an Airbus aircraft involves complex manufacturing processes consisting of thousands of moving parts. Speed and accuracy are critical to business and competitive advantage. Improvements in both would have high impact on Airbus’ bottom line. Airbus wanted to help operators reduce the complexity of assembling cabin seats and decrease the time required to complete this task.
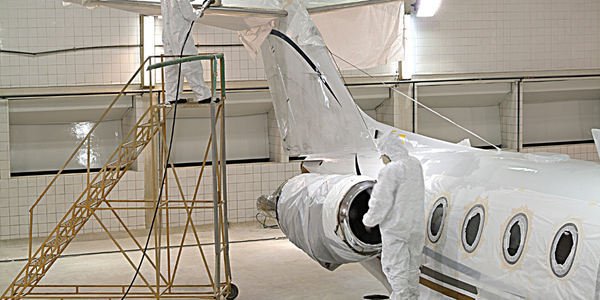
Case Study
Aircraft Predictive Maintenance and Workflow Optimization
First, aircraft manufacturer have trouble monitoring the health of aircraft systems with health prognostics and deliver predictive maintenance insights. Second, aircraft manufacturer wants a solution that can provide an in-context advisory and align job assignments to match technician experience and expertise.
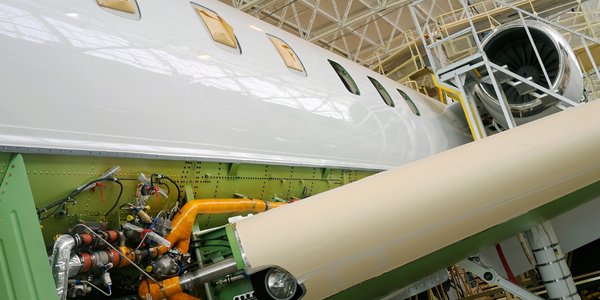
Case Study
Aerospace & Defense Case Study Airbus
For the development of its new wide-body aircraft, Airbus needed to ensure quality and consistency across all internal and external stakeholders. Airbus had many challenges including a very aggressive development schedule and the need to ramp up production quickly to satisfy their delivery commitments. The lack of communication extended design time and introduced errors that drove up costs.