Technology Category
- Robots - Autonomous Guided Vehicles (AGV)
- Sensors - Utility Meters
Applicable Industries
- Automotive
- Metals
Applicable Functions
- Product Research & Development
Use Cases
- Continuous Emission Monitoring Systems
- Vehicle Performance Monitoring
Services
- Testing & Certification
About The Customer
Kanto Auto Works, Ltd., which later became Toyota Motor East Japan, Inc., is a core member of the Toyota Group. The company is responsible for developing and producing Toyota vehicle bodies. The organic-material engineering department of the company evaluates and develops plastic parts to be used in vehicle bodies. In the initial stage of development for large plastic parts, such as instrument panels, the department verifies rigidity and heat resistance using computer aided engineering (CAE). The company's commitment to reducing vehicle weight and improving fuel efficiency is part of a larger global effort to reduce carbon dioxide emissions and combat global warming.
The Challenge
In a bid to reduce carbon dioxide emissions and contribute to the prevention of global warming, the automobile industry has been working on improving vehicle body structures and engine efficiency. A significant part of this effort is the drive to make vehicle bodies lighter, thereby improving fuel efficiency. While metals like steel and aluminum make up most of a car's weight, there has been a growing trend to replace some of these materials with lighter plastic. However, plastic, which now accounts for about 9% of a car's weight, presents its own challenges. It is significantly lighter than metal and can be molded into complex shapes, but it also deforms easily under external force or high temperatures. Kanto Auto Works, a core member of the Toyota Group, was faced with the challenge of making plastic parts lighter while ensuring they maintained sufficient rigidity and heat resistance.
The Solution
To address the challenge, Kanto Auto Works began using OptiStruct, a structural optimization tool from Altair. This tool allowed the company to visualize areas that required reinforcement. OptiStruct combines a choice of optimization functions to create innovative new shapes at any stage of the design process using information that cannot be obtained through experience alone. It enables the creation of lighter parts and reduces steps in the production process by determining optimal materials, identifying where reinforcement is and is not necessary, automatically beading or embossing, optimizing finite element modeling, and determining the optimal sheet thickness and cross-sectional shape of joist structures. Topology optimization calculations were carried out using OptiStruct to visualize areas requiring reinforcement to prevent deformation caused by external force. For heat resistance, calculations were carried out based on the test results for the plastic test plates to determine the load required to cause deformation in the plates.
Operational Impact
Quantitative Benefit
Case Study missing?
Start adding your own!
Register with your work email and create a new case study profile for your business.
Related Case Studies.
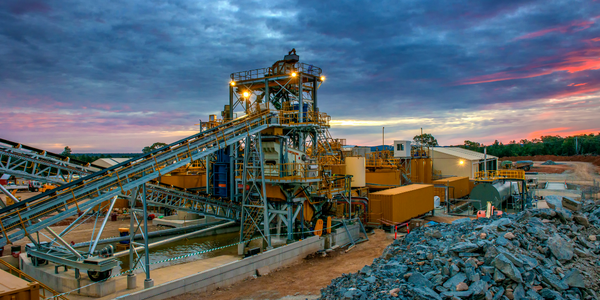
Case Study
Goldcorp: Internet of Things Enables the Mine of the Future
Goldcorp is committed to responsible mining practices and maintaining maximum safety for its workers. At the same time, the firm is constantly exploring ways to improve the efficiency of its operations, extend the life of its assets, and control costs. Goldcorp needed technology that can maximize production efficiency by tracking all mining operations, keep employees safe with remote operations and monitoring of hazardous work areas and control production costs through better asset and site management.

Case Study
KSP Steel Decentralized Control Room
While on-site in Pavlodar, Kazakhstan, the DAQRI team of Business Development and Solutions Architecture personnel worked closely with KSP Steel’s production leadership to understand the steel production process, operational challenges, and worker pain points.
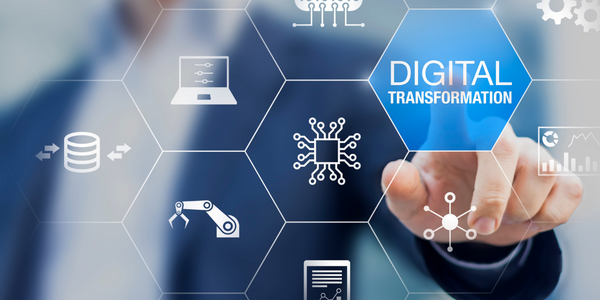
Case Study
Bluescope Steel on Path to Digitally Transform Operations and IT
Increasing competition and fluctuations in the construction market prompted BlueScope Steel to look toward digital transformation of its four businesses, including modern core applications and IT infrastructure. BlueScope needed to modernize its infrastructure and adopt new technologies to improve operations and supply chain efficiency while maintaining and updating an aging application portfolio.
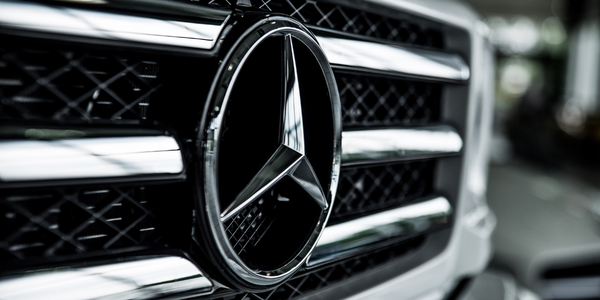
Case Study
Integral Plant Maintenance
Mercedes-Benz and his partner GAZ chose Siemens to be its maintenance partner at a new engine plant in Yaroslavl, Russia. The new plant offers a capacity to manufacture diesel engines for the Russian market, for locally produced Sprinter Classic. In addition to engines for the local market, the Yaroslavl plant will also produce spare parts. Mercedes-Benz Russia and his partner needed a service partner in order to ensure the operation of these lines in a maintenance partnership arrangement. The challenges included coordinating the entire maintenance management operation, in particular inspections, corrective and predictive maintenance activities, and the optimizing spare parts management. Siemens developed a customized maintenance solution that includes all electronic and mechanical maintenance activities (Integral Plant Maintenance).
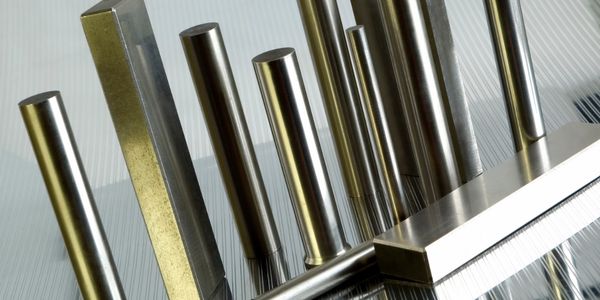
Case Study
RobotStudio Case Study: Benteler Automobiltechnik
Benteler has a small pipe business area for which they produce fuel lines and coolant lines made of aluminum for Porsche and other car manufacturers. One of the problems in production was that when Benteler added new products, production had too much downtime.