Technology Category
- Drones - Multirotor Drones
- Functional Applications - Manufacturing Execution Systems (MES)
Applicable Industries
- Aerospace
- Equipment & Machinery
Applicable Functions
- Maintenance
- Product Research & Development
Use Cases
- Manufacturing Process Simulation
- Time Sensitive Networking
Services
- Testing & Certification
About The Customer
The Boeing Company is a century-old aerospace organization that is the world's largest military aircraft manufacturer. It is known for its understanding and application of current and emerging technologies to improve the capabilities of existing products and deliver new solutions to meet changing customer needs. Boeing's Integrated Defense Systems (IDS) business unit is responsible for the design and manufacture of rotorcraft, aircraft that are kept airborne by airfoils that rotate around a vertical axis. The IDS unit is continuously working to refine these designs to reduce weight and enhance affordability, reliability, and manufacturing efficiency.
The Challenge
Boeing's Integrated Defense Systems (IDS) business unit, the world's largest military aircraft manufacturer, was faced with the challenge of refining rotorcraft designs to reduce weight and enhance affordability, reliability, and manufacturing efficiency. The design of rotorcraft, aircraft kept airborne by rotating airfoils, is a complex balance of form and function. The primary goal is to provide maximum functionality at the lowest overall weight. Weight affects the rotor's capacity for vertical lift, which in turn affects the aircraft's range and ability to fly at safe altitudes. However, reducing weight can also make the aircraft a more survivable target for ground fire. Additionally, the stiffness of the airframe needs to be tuned to reduce vibration, which affects passenger stamina, weapons use, airframe durability, and onboard electronics operation. This is also a weight-related issue. Every pound saved is an opportunity for additional improvements in efficiency, performance, ballistic tolerance, soldier survivability, maintenance, and repairability.
The Solution
Boeing turned to design optimization technology to meet these challenges. They used Altair OptiStruct, a software that designs and optimizes the performance of mechanical structures by defining the best material distribution for a given design space, target mass, and method of manufacture for a given set of objectives and constraints. This software enabled engineers to develop robust, efficient designs that have a higher probability of success in a shorter period of time, compared to the time-consuming trial-and-error approach. For example, using OptiStruct topology optimization technology, the engineers produced a new open truss structure for the ramp of the Boeing CH-47 Chinook heavy-lift transport helicopter. The new design was stiffer than the original while realizing a 17 percent weight savings. The open truss structure also increased the ramp's ballistic tolerance because the reduced volume of the new design presents a sparser target than more dense webs and stiffeners.
Operational Impact
Quantitative Benefit
Case Study missing?
Start adding your own!
Register with your work email and create a new case study profile for your business.
Related Case Studies.
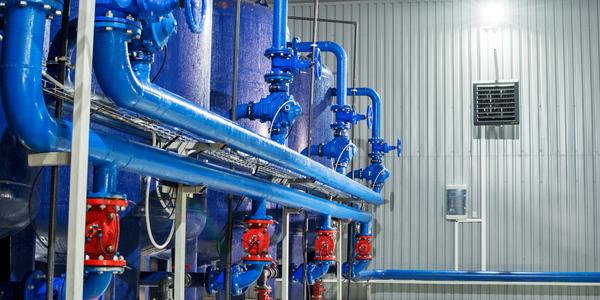
Case Study
Smart Water Filtration Systems
Before working with Ayla Networks, Ozner was already using cloud connectivity to identify and solve water-filtration system malfunctions as well as to monitor filter cartridges for replacements.But, in June 2015, Ozner executives talked with Ayla about how the company might further improve its water systems with IoT technology. They liked what they heard from Ayla, but the executives needed to be sure that Ayla’s Agile IoT Platform provided the security and reliability Ozner required.
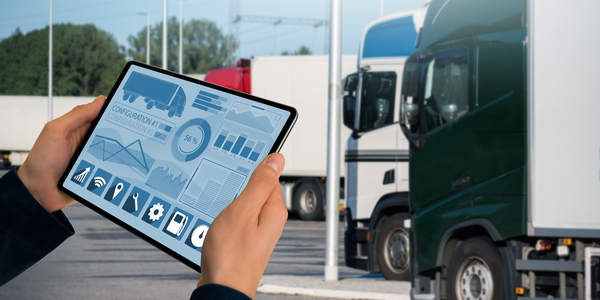
Case Study
IoT enabled Fleet Management with MindSphere
In view of growing competition, Gämmerler had a strong need to remain competitive via process optimization, reliability and gentle handling of printed products, even at highest press speeds. In addition, a digitalization initiative also included developing a key differentiation via data-driven services offers.
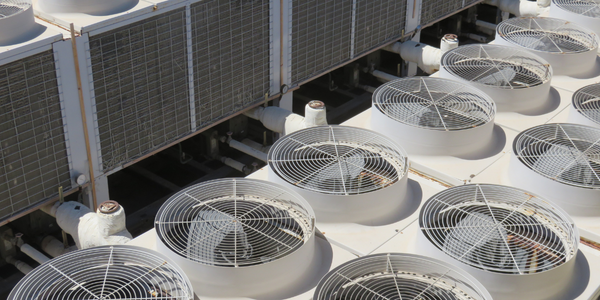
Case Study
Predictive Maintenance for Industrial Chillers
For global leaders in the industrial chiller manufacturing, reliability of the entire production process is of the utmost importance. Chillers are refrigeration systems that produce ice water to provide cooling for a process or industrial application. One of those leaders sought a way to respond to asset performance issues, even before they occur. The intelligence to guarantee maximum reliability of cooling devices is embedded (pre-alarming). A pre-alarming phase means that the cooling device still works, but symptoms may appear, telling manufacturers that a failure is likely to occur in the near future. Chillers who are not internet connected at that moment, provide little insight in this pre-alarming phase.
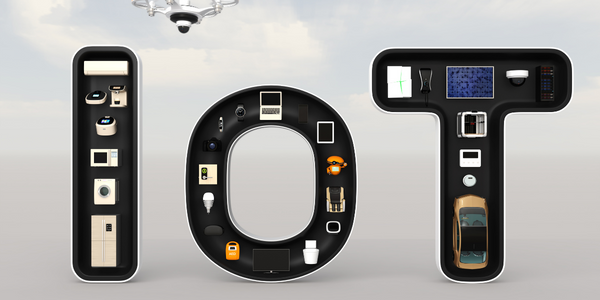
Case Study
Premium Appliance Producer Innovates with Internet of Everything
Sub-Zero faced the largest product launch in the company’s history:It wanted to launch 60 new products as scheduled while simultaneously opening a new “greenfield” production facility, yet still adhering to stringent quality requirements and manage issues from new supply-chain partners. A the same time, it wanted to increase staff productivity time and collaboration while reducing travel and costs.
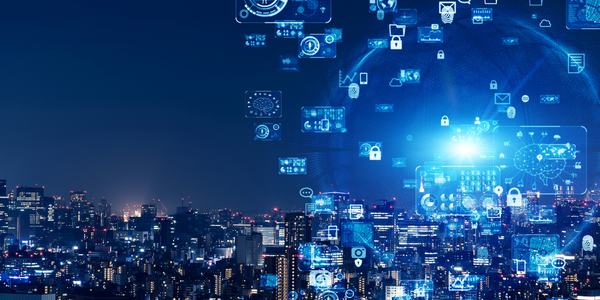
Case Study
Integration of PLC with IoT for Bosch Rexroth
The application arises from the need to monitor and anticipate the problems of one or more machines managed by a PLC. These problems, often resulting from the accumulation over time of small discrepancies, require, when they occur, ex post technical operations maintenance.
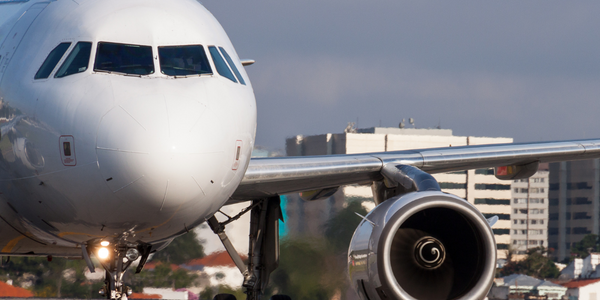
Case Study
Airbus Soars with Wearable Technology
Building an Airbus aircraft involves complex manufacturing processes consisting of thousands of moving parts. Speed and accuracy are critical to business and competitive advantage. Improvements in both would have high impact on Airbus’ bottom line. Airbus wanted to help operators reduce the complexity of assembling cabin seats and decrease the time required to complete this task.