Technology Category
- Sensors - Haptic Sensors
- Sensors - Infrared Sensors
Applicable Industries
- Automotive
- Electronics
Applicable Functions
- Product Research & Development
Use Cases
- Onsite Human Safety Management
About The Customer
Delphi is a world leader in mobile electronics and transportation components and systems technology. The firm operates through various subsidiaries worldwide and has headquarters in Troy, Michigan, Paris, Tokyo, and São Paulo, Brazil. Delphi’s two business sectors – Dynamics, Propulsion, Thermal and Interior Sector and Electronics and Safety Sector – provide comprehensive product solutions to complex customer needs. The company has approximately 186,000 employees and operates 172 wholly owned manufacturing sites, 42 joint ventures, 53 customer centers and sales offices, and 34 technical centers in 41 countries. The Delphi Electronics and Safety division produces about 1 million integrated circuits each day, making it one of the largest in-house manufacturers of customer ICs in the United States.
The Challenge
Delphi, a global leader in mobile electronics and transportation components, faced a significant challenge in the design of their automotive engine control modules (ECMs). The ECMs use silicone rubber spacers in the shape of truncated cones to ensure thermal or electrical contact between different components. These spacers press the integrated circuit (IC) against metal heat sinks to provide a conduction heat transfer path to cool the circuitry. Determining the force exerted by the spacer is critical to the design of the module. Insufficient force would not adequately cool the IC or properly secure it, resulting in premature failure due to overheating or excessive shock and vibration. Conversely, the force cannot be set too high because of constraints in the ECM housing and printed-circuit board. The challenge was to accurately represent the elastomer material so spacers could be designed to provide an optimal force against the circuit board.
The Solution
Delphi utilized ANSYS Structural to accurately represent the elastomer material so spacers could be designed to provide an optimal force against the circuit board. Mooney-Rivlin material constants for the FEA model were derived from experimentation, where spacer samples were compressed and resulting force-deflection curves derived through curve-fitting commands and macros in ANSYS. FEA models were developed and validated by reproducing the measured data with very good accuracy. These FEA models were then used to accurately predict force-deflection curves for new spacers as well as establish curves for spacers already in use. ANSYS contact elements were particularly useful in these models to represent surface-to-surface contact between the spacer and PCB. Furthermore, ANSYS Parametric Design Language (APDL) was developed to model the spacers as well as to extract FEA results data of interest to product engineers and present this information in tabular form.
Operational Impact
Quantitative Benefit
Case Study missing?
Start adding your own!
Register with your work email and create a new case study profile for your business.
Related Case Studies.
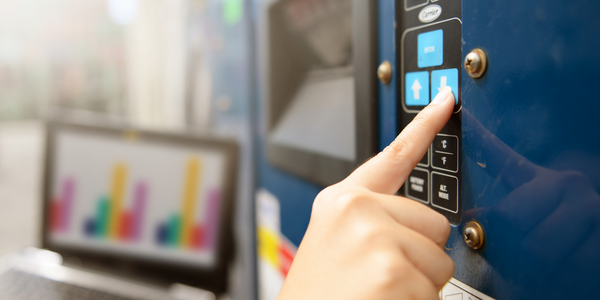
Case Study
Remote Temperature Monitoring of Perishable Goods Saves Money
RMONI was facing temperature monitoring challenges in a cold chain business. A cold chain must be established and maintained to ensure goods have been properly refrigerated during every step of the process, making temperature monitoring a critical business function. Manual registration practice can be very costly, labor intensive and prone to mistakes.
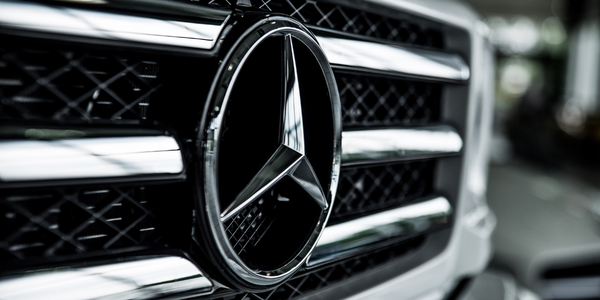
Case Study
Integral Plant Maintenance
Mercedes-Benz and his partner GAZ chose Siemens to be its maintenance partner at a new engine plant in Yaroslavl, Russia. The new plant offers a capacity to manufacture diesel engines for the Russian market, for locally produced Sprinter Classic. In addition to engines for the local market, the Yaroslavl plant will also produce spare parts. Mercedes-Benz Russia and his partner needed a service partner in order to ensure the operation of these lines in a maintenance partnership arrangement. The challenges included coordinating the entire maintenance management operation, in particular inspections, corrective and predictive maintenance activities, and the optimizing spare parts management. Siemens developed a customized maintenance solution that includes all electronic and mechanical maintenance activities (Integral Plant Maintenance).