Applicable Industries
- Automotive
- Equipment & Machinery
Applicable Functions
- Product Research & Development
- Quality Assurance
Use Cases
- Mesh Networks
- Smart Campus
Services
- Testing & Certification
About The Customer
The customer in this case study is the Biomedical Engineering Center of Wayne State University, located in the United States of America. The center has been conducting research in impact biomechanics and automotive safety for over 60 years, making it a leading institution in the field. The center is also a pioneer in the development of finite element models of the human body, which are used to understand injury mechanisms during automotive impacts and to design countermeasures. These models are also proving to be useful research tools in the field of orthopaedics biomechanics, where they can be used to better understand in-vivo loading.
The Challenge
The Biomedical Engineering Center of Wayne State University has been conducting research in impact biomechanics and automotive safety for over six decades. They are a leading institution in the development of finite element models of the human body. These models are used to understand injury mechanisms during automotive impacts and help design countermeasures. They are also useful in orthopaedics biomechanics to understand in-vivo loading. However, due to the use of explicit finite element codes, the typical meshing objective is a high-quality fully hexahedral mesh that respects minimum element size criteria. The anatomical complexity and irregularity of shapes make meshing a critical task in the development of these models. The team typically meshes bones and organs, with geometrical data reconstructed based on medical imaging (MRI or CT scans).
The Solution
The team at Wayne State University uses ANSYS ICEM CFD for basic repair of the geometry and to generate the mesh with the ANSYS ICEM CFD Hexa module. The Hexa blocking technique is extremely useful in finding an acceptable meshing topology. Once the mesh is generated based on minimum size constraints, it is optimized for quality in ANSYS ICEM CFD and exported to a format supported by their preprocessing tools. The key benefit of ANSYS ICEM CFD Hexa is the separation of the search for an acceptable meshing topology from the mesh generation itself. This, combined with the top-down approach and easy block editing, allows the team to try various meshing topologies very quickly independently from the mesh density, change the element density easily without changing the topology, and use the same or similar blocking topology for different individuals.
Operational Impact
Case Study missing?
Start adding your own!
Register with your work email and create a new case study profile for your business.
Related Case Studies.
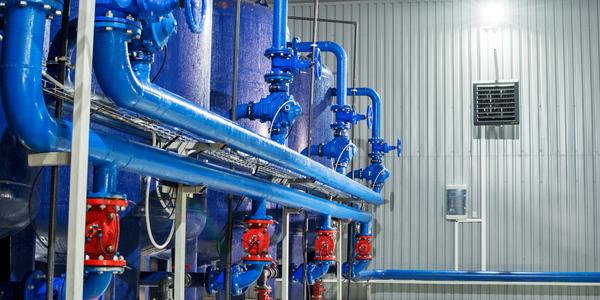
Case Study
Smart Water Filtration Systems
Before working with Ayla Networks, Ozner was already using cloud connectivity to identify and solve water-filtration system malfunctions as well as to monitor filter cartridges for replacements.But, in June 2015, Ozner executives talked with Ayla about how the company might further improve its water systems with IoT technology. They liked what they heard from Ayla, but the executives needed to be sure that Ayla’s Agile IoT Platform provided the security and reliability Ozner required.
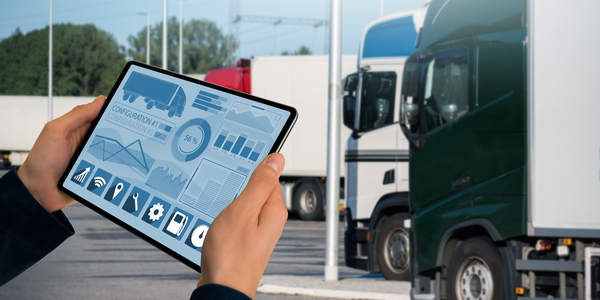
Case Study
IoT enabled Fleet Management with MindSphere
In view of growing competition, Gämmerler had a strong need to remain competitive via process optimization, reliability and gentle handling of printed products, even at highest press speeds. In addition, a digitalization initiative also included developing a key differentiation via data-driven services offers.
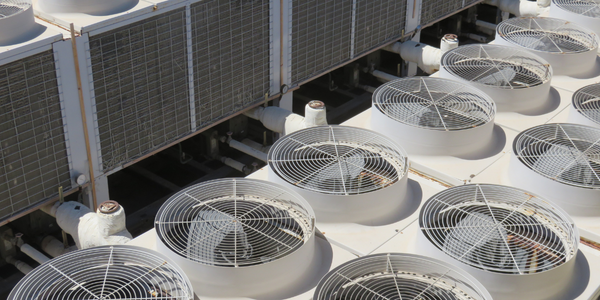
Case Study
Predictive Maintenance for Industrial Chillers
For global leaders in the industrial chiller manufacturing, reliability of the entire production process is of the utmost importance. Chillers are refrigeration systems that produce ice water to provide cooling for a process or industrial application. One of those leaders sought a way to respond to asset performance issues, even before they occur. The intelligence to guarantee maximum reliability of cooling devices is embedded (pre-alarming). A pre-alarming phase means that the cooling device still works, but symptoms may appear, telling manufacturers that a failure is likely to occur in the near future. Chillers who are not internet connected at that moment, provide little insight in this pre-alarming phase.
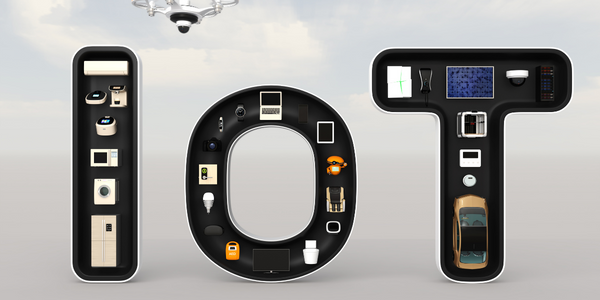
Case Study
Premium Appliance Producer Innovates with Internet of Everything
Sub-Zero faced the largest product launch in the company’s history:It wanted to launch 60 new products as scheduled while simultaneously opening a new “greenfield” production facility, yet still adhering to stringent quality requirements and manage issues from new supply-chain partners. A the same time, it wanted to increase staff productivity time and collaboration while reducing travel and costs.
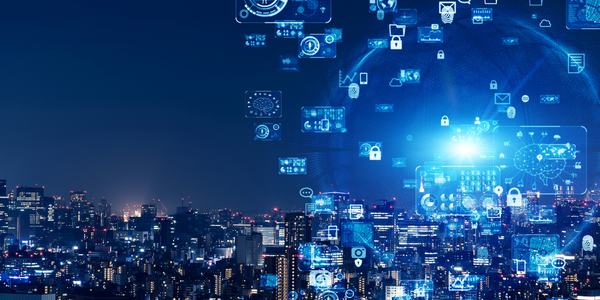
Case Study
Integration of PLC with IoT for Bosch Rexroth
The application arises from the need to monitor and anticipate the problems of one or more machines managed by a PLC. These problems, often resulting from the accumulation over time of small discrepancies, require, when they occur, ex post technical operations maintenance.
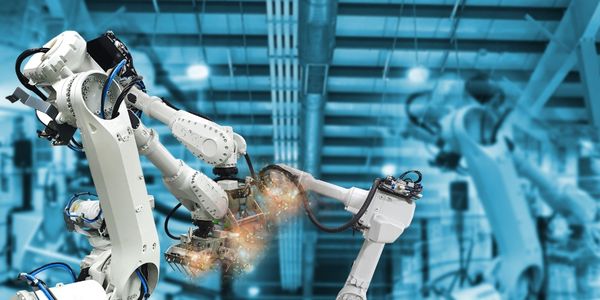
Case Study
Robot Saves Money and Time for US Custom Molding Company
Injection Technology (Itech) is a custom molder for a variety of clients that require precision plastic parts for such products as electric meter covers, dental appliance cases and spools. With 95 employees operating 23 molding machines in a 30,000 square foot plant, Itech wanted to reduce man hours and increase efficiency.