Technology Category
- Infrastructure as a Service (IaaS) - Virtual Private Cloud
- Sensors - Chemical Sensors
Applicable Industries
- Chemicals
- Plastics
Applicable Functions
- Product Research & Development
- Quality Assurance
Use Cases
- Transportation Simulation
- Virtual Reality
About The Customer
BASF is the world’s leading chemical company, with a portfolio that ranges from oil and gas to chemicals, plastics, performance products, agricultural products, and fine chemicals. BASF helps its customers in virtually all industries to be more successful through its high-value products and intelligent solutions. The company plays an important role in finding answers to global challenges such as climate protection, energy efficiency, nutrition, and mobility. BASF has more than 95,000 employees and posted sales of almost €58 billion in 2007. The Engineering Plastics division's design capabilities reside in its Application Development Engineering Group, which employs leading-edge technologies and methods in their activities.
The Challenge
BASF Engineering Plastics, a division of the world's leading chemical company, BASF, is tasked with providing superior engineering design, simulation, and testing support during all phases of the development cycle. The group's primary goal is to provide superior engineering design, simulation, and testing support during all phases of the development cycle. However, the support of various customers in the application of modern materials often demands new concepts that make the advantages of the material applicable. This challenge is further compounded by the need to continually develop modern virtual methods to meet the needs of its customers, as the company believes that mathematical part optimization will broadly gain acceptance as the method of choice in the next few years.
The Solution
To address this challenge, BASF Engineering Plastics has been increasingly focusing on Mathematical Part Optimisation within the framework of BASF’s CAE activities. This method not only allows for the design of optimum parts on the computer but also fills a gap in virtual part development. Altair OptiStruct is the initial tool in this process. Mathematical optimization methods provide significant support in virtual CAE part development. In the early phases of the project, topology optimization provides valuable clues to the design of the geometry of the part. Subsequent questions about the precise dimensions can be effectively answered by parameter optimization runs. The use of morphing methods for this purpose has to be given particular emphasis.
Case Study missing?
Start adding your own!
Register with your work email and create a new case study profile for your business.
Related Case Studies.
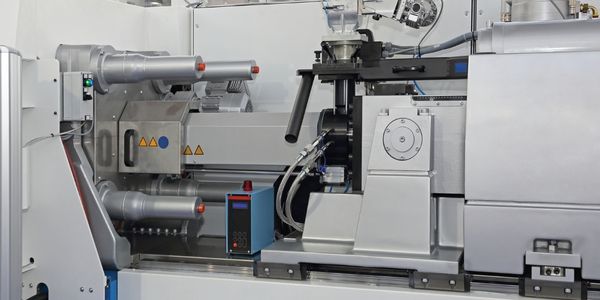
Case Study
Plastic Spoons Case study: Injection Moulding
In order to meet customer expectations by supplying a wide variety of packaging units, from 36 to 1000 spoons per package, a new production and packaging line needed to be built. DeSter wanted to achieve higher production capacity, lower cycle time and a high degree of operator friendliness with this new production line.
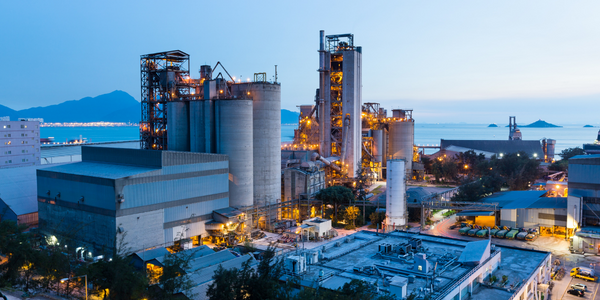
Case Study
Honeywell - Tata Chemicals Improves Data Accessibility with OneWireless
Tata was facing data accessibility challenges in the cement plant control room tapping signals from remote process control areas and other distant locations, including the gas scrubber. Tata needed a wireless solution to extend its control network securely to remote locations that would also provide seamless communication with existing control applications.

Case Study
Advanced Elastomer Systems Upgrades Production
In order to maintain its share of the international market for thermoplastic elastomers AES recently expanded its Florida plant by adding a new production line. While the existing lines were operating satisfactorily using a PROVOX distributed control system with traditional analog I/O, AES wanted advanced technology on the new line for greater economy, efficiency, and reliability. AES officials were anxious to get this line into production to meet incoming orders, but two hurricanes slowed construction.
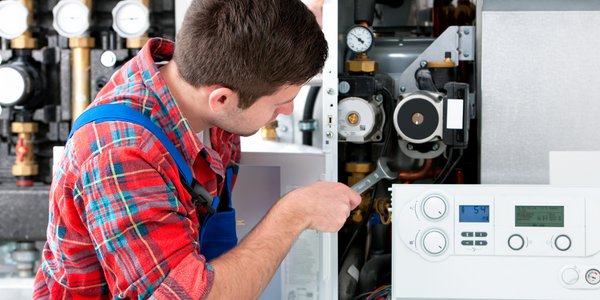
Case Study
Boiler Control System for Plastic Manufacturing Applications
Factory automation applications must be equipped to handle and monitor the myriads of information from attached devices. For plastic manufacturing applications, the boiler control system plays a critical role by gathering and regulating information to ensure production is accurate and smooth. In this particular case, the customer combines eight subsystems that include power meters, water meters, alarm output, displays, and I/O status to be controlled by several intelligent controllers with Modbus RTU interface. The Modbus TCP protocol is used for this application due to the distance. System Requirements: • Modbus serial to Modbus TCP translation • Multiple slaves/masters support • Automatic Modbus TCP response time detection
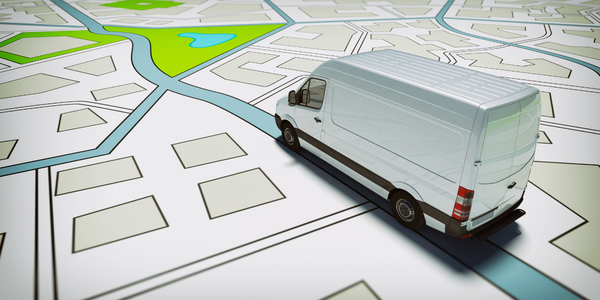
Case Study
Wireless GPS Tracking & Security Monitoring
Enhancing the security of hazardous freight and ensuring compliance with Homeland Security’s Transportation Security Administration mandate that all trains carrying chemicals capable of creating a toxic inhalation condition are equipped with on-board safety monitoring systems.