
Technology Category
- Sensors - Barcode Readers
- Sensors - GPS
Applicable Industries
- Pharmaceuticals
- Transportation
Applicable Functions
- Logistics & Transportation
- Sales & Marketing
Use Cases
- Augmented Reality
- Last Mile Delivery
The Customer
NACEX
About The Customer
NACEX is a leading B2B and B2C courier service for parcels and documents, operating in Spain, Portugal, and Andorra. The company provides value-added services for deliveries with special requirements, such as pharmaceuticals. They have an exclusive network of franchisees across the regions they operate for handling last mile deliveries. With a combined total of over 1,500 vehicles, franchisees receive parcels from NACEX distribution hubs every morning – sorting them into vans for delivery to the final destination. NACEX relies on technology to enhance the quality of service to their franchisees and customers.
The Challenge
NACEX, a leading courier service operating in Spain, Portugal, and Andorra, was facing challenges in speeding up parcel deliveries from distribution centers to the last mile. The company, which handles special requirement deliveries such as pharmaceuticals, relied on franchisees with over 1,500 vehicles to sort and deliver parcels. The standard receiving process involved using a dedicated device to scan the barcode on every parcel for verification and sorting. The company wanted to improve scan speeds and the type of information they could record for faster delivery and improved customer service. With last mile drivers scanning over five million barcodes every month, superfast scanning was critical. Additionally, they needed to maintain proof of delivery records for each delivery, which included photographing the parcel and the recipient’s signature, or scanning it. Drivers delivering pharmaceutical items had to abide by stringent temperature requirements and delivery times, and needed to be alerted in advance of any updates.
The Solution
NACEX replaced dedicated scanners for last mile drivers with an Android app that integrates with Scandit’s barcode scanner SDK, and extended its functionality with MatrixScan-AR and OCR. The GPS navigation on the smartphone app determines the driver's location and the parcels scheduled for delivery. MatrixScan is used to capture multiple barcodes on several parcels in the van with a single scan, where barcodes on parcels for delivery are highlighted on their smartphone screens based on AR feedback. AR overlays on the barcode offer additional information to support quicker deliveries. This could include instructions for drivers to deliver items at locations specified by customers, if they could not receive parcels in-person, amongst other things. Drivers who deliver pharmaceutical items now receive automatic alerts through the AR overlays, if deliveries need to be paused or terminated. For parcels or packages with barcode labels that are badly damaged in transit, last mile drivers use the OCR functionality in the scanning app to capture the accompanying text.
Operational Impact
Quantitative Benefit
Case Study missing?
Start adding your own!
Register with your work email and create a new case study profile for your business.
Related Case Studies.
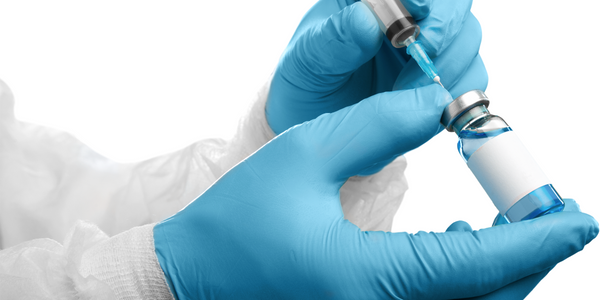
Case Study
Case Study: Pfizer
Pfizer’s high-performance computing software and systems for worldwide research and development support large-scale data analysis, research projects, clinical analytics, and modeling. Pfizer’s computing services are used across the spectrum of research and development efforts, from the deep biological understanding of disease to the design of safe, efficacious therapeutic agents.
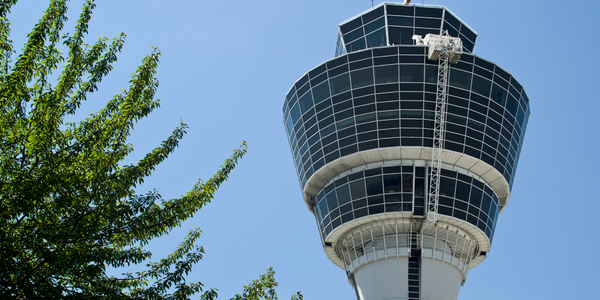
Case Study
Airport SCADA Systems Improve Service Levels
Modern airports are one of the busiest environments on Earth and rely on process automation equipment to ensure service operators achieve their KPIs. Increasingly airport SCADA systems are being used to control all aspects of the operation and associated facilities. This is because unplanned system downtime can cost dearly, both in terms of reduced revenues and the associated loss of customer satisfaction due to inevitable travel inconvenience and disruption.
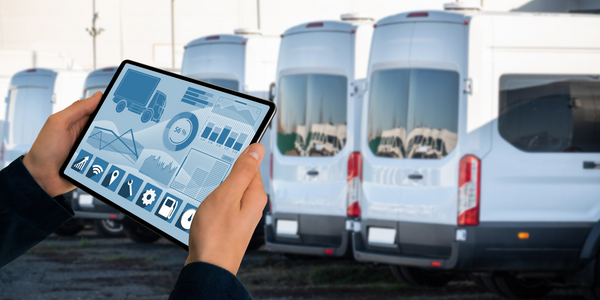
Case Study
IoT-based Fleet Intelligence Innovation
Speed to market is precious for DRVR, a rapidly growing start-up company. With a business model dependent on reliable mobile data, managers were spending their lives trying to negotiate data roaming deals with mobile network operators in different countries. And, even then, service quality was a constant concern.
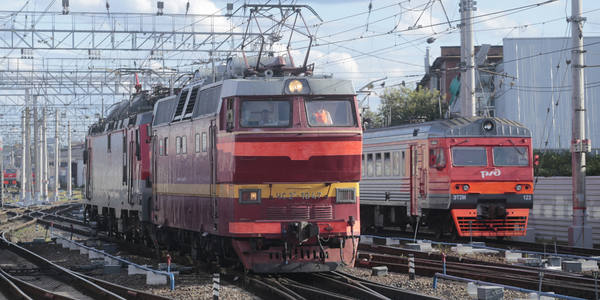
Case Study
Digitize Railway with Deutsche Bahn
To reduce maintenance costs and delay-causing failures for Deutsche Bahn. They need manual measurements by a position measurement system based on custom-made MEMS sensor clusters, which allow autonomous and continuous monitoring with wireless data transmission and long battery. They were looking for data pre-processing solution in the sensor and machine learning algorithms in the cloud so as to detect critical wear.
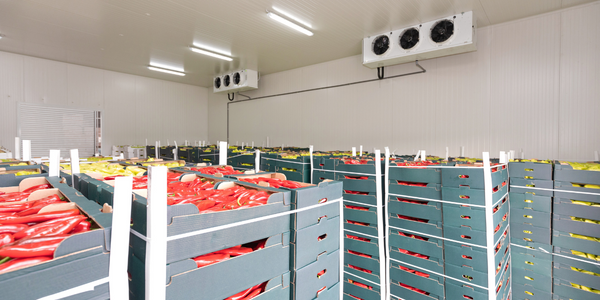
Case Study
Cold Chain Transportation and Refrigerated Fleet Management System
1) Create a digital connected transportation solution to retrofit cold chain trailers with real-time tracking and controls. 2) Prevent multi-million dollar losses due to theft or spoilage. 3) Deliver a digital chain-of-custody solution for door to door load monitoring and security. 4) Provide a trusted multi-fleet solution in a single application with granular data and access controls.
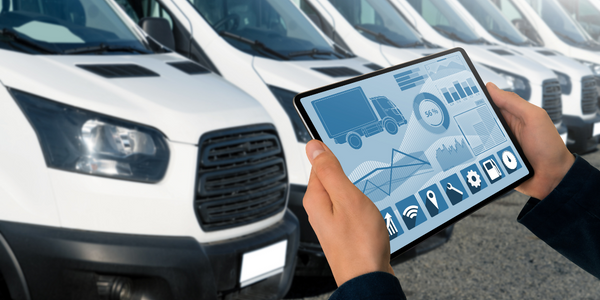
Case Study
Vehicle Fleet Analytics
Organizations frequently implement a maintenance strategy for their fleets of vehicles using a combination of time and usage based maintenance schedules. While effective as a whole, time and usage based schedules do not take into account driving patterns, environmental factors, and sensors currently deployed within the vehicle measuring crank voltage, ignition voltage, and acceleration, all of which have a significant influence on the overall health of the vehicle.In a typical fleet, a large percentage of road calls are related to electrical failure, with battery failure being a common cause. Battery failures result in unmet service agreement levels and costly re-adjustment of scheduled to provide replacement vehicles. To reduce the impact of unplanned maintenance, the transportation logistics company was interested in a trial of C3 Vehicle Fleet Analytics.