Technology Category
- Sensors - Gas Sensors
- Sensors - Utility Meters
Applicable Industries
- Oil & Gas
- Transportation
Applicable Functions
- Logistics & Transportation
Use Cases
- Inventory Management
- Time Sensitive Networking
Services
- System Integration
About The Customer
Nuovo Pignone, now a key technological component of GE's Oil & Gas business, began life 100 years ago as a foundry. Today, more than 20,000 machines manufactured by this GE business are operated worldwide by major companies to keep petroleum products moving from oil rigs to storage facilities to refineries to distribution points. The engineering groups at GE's Oil & Gas Florence headquarters work extensively with commercial and proprietary CFD and CEA tools which are used to build and test product designs. The gas turbine engineering group designs gas turbines that are installed in the pipeline system or offshore for mechanical drive applications. Their customers are major petroleum companies like Shell and Texaco, with sites around the world.
The Challenge
GE's Oil & Gas business was facing a significant challenge in job scheduling for their applications. The gas turbine engineering group was upgrading its High-Performance Computing (HPC) resources, moving from an 8-CPU UNIX server to a 20-CPU HP ProLiant 380 cluster running Red Hat Linux. However, they encountered unexpected difficulties in job scheduling using open source code. The situation was becoming increasingly difficult to manage, causing delays in production. The group leader, Alessandro Ciani, was tasked with getting the cluster into production but was frustrated with the delays. The situation was urgent, and a solution was needed to ensure the system could be put into production.
The Solution
Altair, a global technology company providing solutions in product development, high-performance computing and data intelligence, was approached to provide a solution. Instead of a standard presentation, Altair suggested a pilot installation of their PBS Professional® workload management software. This integrated workload management solution was optimized for running the StarCD application. The GE engineering team was soon able to submit and manage its StarCD workload with confidence. Following the success of the pilot, GE's Oil & Gas business purchased PBS Professional licenses for all CPUs in the cluster and hired Altair to integrate their other applications into their PBS Professional cluster. The cluster was expanded by adding heterogeneous nodes, and all 90 processors in the cluster and the corresponding application licenses were efficiently managed with PBS Professional.
Operational Impact
Quantitative Benefit
Case Study missing?
Start adding your own!
Register with your work email and create a new case study profile for your business.
Related Case Studies.
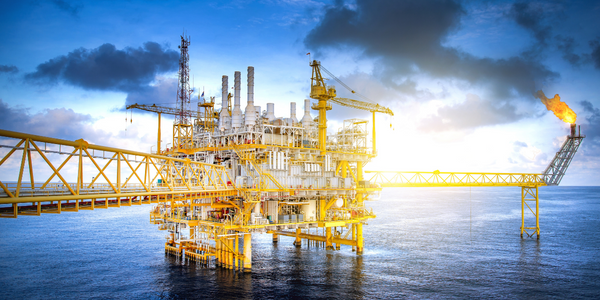
Case Study
Taking Oil and Gas Exploration to the Next Level
DownUnder GeoSolutions (DUG) wanted to increase computing performance by 5 to 10 times to improve seismic processing. The solution must build on current architecture software investments without sacrificing existing software and scale computing without scaling IT infrastructure costs.
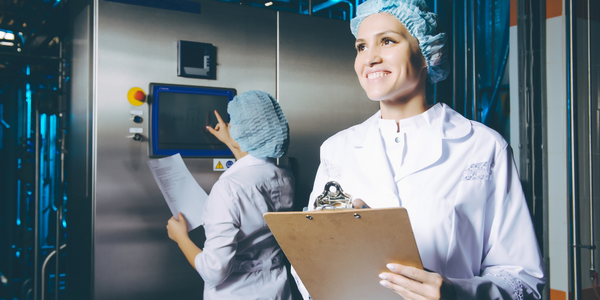
Case Study
Remote Wellhead Monitoring
Each wellhead was equipped with various sensors and meters that needed to be monitored and controlled from a central HMI, often miles away from the assets in the field. Redundant solar and wind generators were installed at each wellhead to support the electrical needs of the pumpstations, temperature meters, cameras, and cellular modules. In addition to asset management and remote control capabilities, data logging for remote surveillance and alarm notifications was a key demand from the customer. Terra Ferma’s solution needed to be power efficient, reliable, and capable of supporting high-bandwidth data-feeds. They needed a multi-link cellular connection to a central server that sustained reliable and redundant monitoring and control of flow meters, temperature sensors, power supply, and event-logging; including video and image files. This open-standard network needed to interface with the existing SCADA and proprietary network management software.
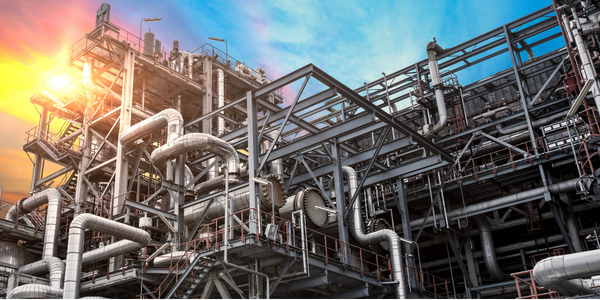
Case Study
Refinery Saves Over $700,000 with Smart Wireless
One of the largest petroleum refineries in the world is equipped to refine various types of crude oil and manufacture various grades of fuel from motor gasoline to Aviation Turbine Fuel. Due to wear and tear, eight hydrogen valves in each refinery were leaking, and each cost $1800 per ton of hydrogen vented. The plant also had leakage on nearly 30 flare control hydrocarbon valves. The refinery wanted a continuous, online monitoring system that could catch leaks early, minimize hydrogen and hydrocarbon production losses, and improve safety for maintenance.
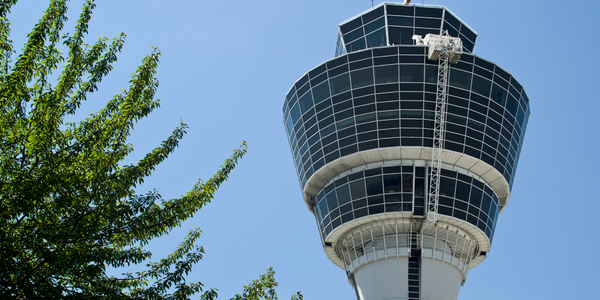
Case Study
Airport SCADA Systems Improve Service Levels
Modern airports are one of the busiest environments on Earth and rely on process automation equipment to ensure service operators achieve their KPIs. Increasingly airport SCADA systems are being used to control all aspects of the operation and associated facilities. This is because unplanned system downtime can cost dearly, both in terms of reduced revenues and the associated loss of customer satisfaction due to inevitable travel inconvenience and disruption.