Technology Category
- Other - Battery
- Sensors - Autonomous Driving Sensors
Applicable Industries
- Automotive
- Electrical Grids
Applicable Functions
- Procurement
- Product Research & Development
Use Cases
- Smart Parking
- Vehicle-to-Infrastructure
Services
- System Integration
- Testing & Certification
About The Customer
The customer in this case is a leading Formula E team. Formula E is a class of auto racing that uses only electric-powered cars. The series was conceived in 2012, and the inaugural championship started in Beijing in September 2014. The series is sanctioned by the FIA. The customer team, recognizing the limitations imposed by the standardized battery, sought to optimize their car's performance by developing dynamic models of their car. They aimed to use these models to develop customized racing strategies for different tracks, weather conditions, and pit stops, ensuring optimal use of their battery power.
The Challenge
Competitive racing, particularly in the all-electric class of Formula E, demands the utmost from both driver skill and engineering innovation. However, the regulations in this field are stringent, with the battery being standardized across all vehicles. This leaves teams with limited areas for customization and performance enhancement. A leading Formula E team, recognizing these constraints, sought to develop dynamic models of their car to find new ways to optimize their systems for peak performance. The team aimed to develop customized racing strategies for different tracks, weather conditions, and pit stops, ensuring optimal use of their battery power. They also wanted to incorporate real-time simulations to update the team with information as variables change during the race, a feature not commonly available without a system-level modeling tool.
The Solution
Maplesoft was approached to develop a dynamic car model that would be validated against real-world performance data. The model needed to incorporate several important systems, including the chassis, steering, tires, battery, inverter, motor, and gearbox. Using the system-level modeling tool MapleSim, engineers were able to capture the dynamics of each system in one multidomain environment. A crucial step in the process was correlating the model’s parameters with test data provided by the Formula E team to ensure accurate data across the range of operating conditions. With all these components together in one system, the Formula E team could better understand trade-offs when trying to design a better car and a faster racing strategy. The model could simulate ideal performance in various scenarios and provide new insights for the team, such as modifying how the driver might accelerate on certain turns or the ideal timing for using their FanBoost accelerations in various kinds of weather.
Operational Impact
Case Study missing?
Start adding your own!
Register with your work email and create a new case study profile for your business.
Related Case Studies.
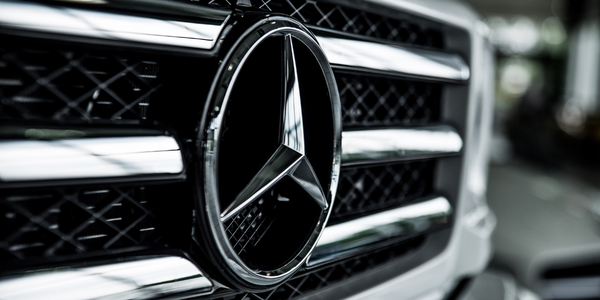
Case Study
Integral Plant Maintenance
Mercedes-Benz and his partner GAZ chose Siemens to be its maintenance partner at a new engine plant in Yaroslavl, Russia. The new plant offers a capacity to manufacture diesel engines for the Russian market, for locally produced Sprinter Classic. In addition to engines for the local market, the Yaroslavl plant will also produce spare parts. Mercedes-Benz Russia and his partner needed a service partner in order to ensure the operation of these lines in a maintenance partnership arrangement. The challenges included coordinating the entire maintenance management operation, in particular inspections, corrective and predictive maintenance activities, and the optimizing spare parts management. Siemens developed a customized maintenance solution that includes all electronic and mechanical maintenance activities (Integral Plant Maintenance).

Case Study
Hydro One Leads the Way In Smart Meter Development
In 2010, Ontario’s energy board mandated that time-of-use (TOU) pricing for consumers be available for all consumers on a regulated price plan. To meet this requirement, Hydro One needed to quickly deploy a smart meter and intelligent communications network solution to meet the provincial government’s requirement at a low cost. The network needed to cover Hydro One’s expansive service territory, which has a land mass twice the size of Texas, and its customers live in a mix of urban, rural, and remote areas, some places only accessible by air, rail, boat or snowmobile. Most importantly, the network needed to enable future enterprise-wide business efficiencies, modernization of distribution infrastructure and enhanced customer service. To meet these needs, Hydro One conceptualized an end-to-end solution leveraging open standards and Internet Protocols (IP) at all communication levels. The utility drew upon industry leaders like Trilliant to realize this vision.

Case Study
Monitoring of Pressure Pumps in Automotive Industry
A large German/American producer of auto parts uses high-pressure pumps to deburr machined parts as a part of its production and quality check process. They decided to monitor these pumps to make sure they work properly and that they can see any indications leading to a potential failure before it affects their process.