Technology Category
- Sensors - Flow Meters
- Sensors - Liquid Detection Sensors
Applicable Industries
- Life Sciences
- Mining
Applicable Functions
- Logistics & Transportation
- Product Research & Development
Use Cases
- Digital Twin
- Virtual Reality
Services
- System Integration
About The Customer
ArcelorMittal is the world’s leading steel and mining company, with a presence in 60 countries and primary steelmaking facilities in 17 countries. The company employs more than 190,000 people. In a recent project, the company's R&D team was tasked with optimizing a large-scale charging chute of a sinter cooler plant in Fos-Sur-Mer. The goal was to improve the reliability and efficiency of this device by identifying a better design that improved granular segregation, abrasion, and mechanical resistance.
The Challenge
ArcelorMittal, the world’s leading steel and mining company, faced a challenge in optimizing a large-scale charging chute of a sinter cooler plant in Fos-Sur-Mer. The objective was to improve the reliability and efficiency of the device by identifying a better design that enhanced granular segregation, abrasion, and mechanical resistance. The process of charging hot material into the sinter cooler often led to particle segregation, causing severe problems such as fire issues on conveyor belts and sinter quality issues. The R&D team needed to investigate these segregation patterns, particularly the impact of particle sizes and the effect of the filling ratio on the segregation patterns in the trolleys of the sinter strand. However, simulating granular flows in a large system compared to the particle size was complex and time-consuming. The team needed a modelling strategy that balanced computational efficiency and physical realism.
The Solution
ArcelorMittal R&D team used Altair® EDEM™, a high-performance software for granular material simulation, to simulate and analyze the granular flows in the charging chute. EDEM provided pre-calibrated material models, enabling the engineers to create and calibrate their model to match the physical experiments. The engineers first analyzed the segregation patterns in the trolleys of the sinter strand, which were in good agreement with the experimental measurements at the plant. They then performed a sensitivity study using different particle sizes to determine whether finer materials would change the segregation pattern. The results revealed that the size of the particles had no effect on the segregation patterns. The team also studied the effect of the filling ratio on granular flow patterns, finding that a large filling ratio led to an even distribution while a low filling ratio had a negative effect. Using these results, the engineers virtually tested different charging chute scenarios to find a design that met all requirements regarding capacity and mechanical resistance.
Operational Impact
Case Study missing?
Start adding your own!
Register with your work email and create a new case study profile for your business.
Related Case Studies.
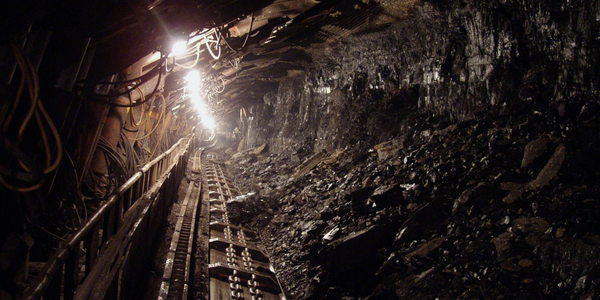
Case Study
Underground Mining Safety
The goal was to produce a safety system to monitor and support underground mining operations; existing systems were either too simple (i.e. phone line) or overly complex and expensive, inhibiting deployment, and providing little-to-no support in event of an accident. Given the dangerous nature of the mining work environment and the strict regulations placed on the industry, the solution would have to comply with Mine Safety and Health Administration (MSHA) regulations. Yet the product needed to allow for simple deployment to truly be a groundbreaking solution - increasing miner safety and changing daily operations for the better.
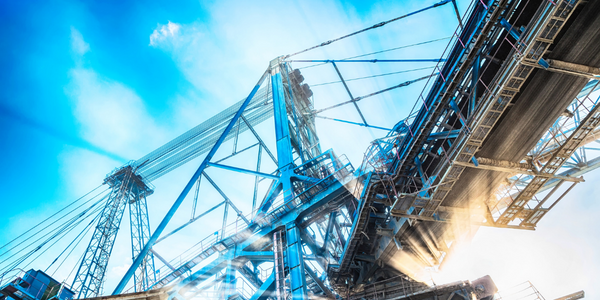
Case Study
Mining Firm Quadruples Production, with Internet of Everything
Dundee Precious Metal’s flagship mine, in Chelopech, Bulgaria, produces a gold, copper, and silver concentrate set a goal to increase production by 30%. Dundee wanted to increase production quality and output without increasing headcount and resources, improve miner safety, and minimize cost.
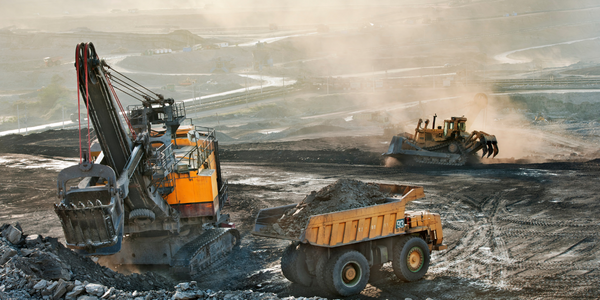
Case Study
Fastenal Builds the Future of Manufacturing with MachineMetrics
Fastenal's objective was to better understand their machine downtime, utilization, quality issues, and to embrace cutting-edge manufacturing technology/process improvement capabilities to bring their team to the next level. However, there was a lack of real-time data, visualization, and actionable insights made this transition impossible.
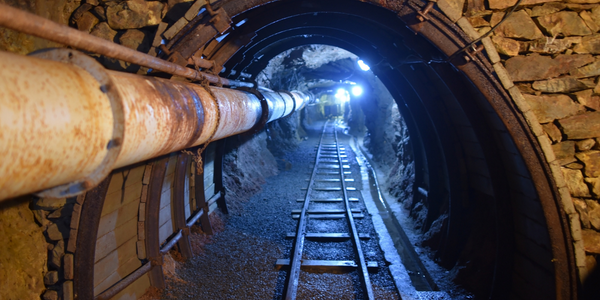
Case Study
Joy Mining Systems
Joy equipment faces many challenges. The first is machine integration and control. The business end of the machine has a rapidly-spinning cylinder with 6-inch diamond-studded cutting teeth. It chews through rock at rates measured in tens of tons per minute. The system grinds through the rock in front, creating a rectangular mine tunnel. Hydraulic lifters support the ceiling as the machine moves forward. Automated drills and screws drive 3-ft long screws into the ceiling to stabilize it. The rock and coal fall into a set of gathering "fingers" below the cutting cylinder. These fingers scoop up the rock and coal and deposit it onto a conveyor belt. The conveyor passes under the machine and out the back. A train of conveyor belt cars, up to a mile long, follows the cutter into the mine. The rock shoots along this train at over 400 feet per minute until it empties into rail cars at the end. Current systems place an operator cage next to the cutter. Choking dust (potentially explosive), the risk of collapse and the proximity of metal and rock mayhem make the operator cage a hazardous location.
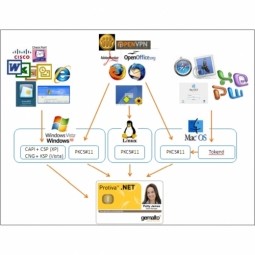
Case Study
Corporate Identity Solution Adds Convenience to Beckman Coulter
Beckman Coulter wanted to implement a single factor solution for physical and remote logical access to corporate network. Bechman Coulter's users were carrying smart card badges for doors, but also needed a one-time password token to access to our corporate network when they were not in the office. They wanted to simplify the process.
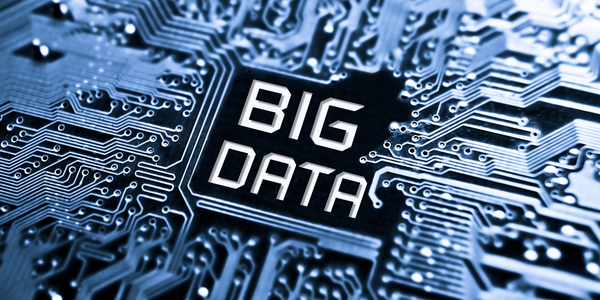
Case Study
Embracing Business Success in Real Time
· Increase control over growing Big Data to improve business decisions · Manage data for 28,000 biotechnology stockkeeping units in the fields of microbiology, molecular biology, animal cell cultures, plant tissue cultures, and lab ware for laboratory chemicals · Accelerate report generation and analysis with real-time data