Customer Company Size
Large Corporate
Region
- Asia
Country
- Australia
Product
- Vocollect Talkman A730 Mobile Computing Devices
- Vocollect SRX2 Series Wireless Headsets
- Vocollect VoiceDirect ERP for SAP
Tech Stack
- Voice Technology
- SAP WMS
Implementation Scale
- Enterprise-wide Deployment
Impact Metrics
- Customer Satisfaction
- Employee Satisfaction
- Productivity Improvements
- Waste Reduction
Technology Category
- Functional Applications - Remote Monitoring & Control Systems
- Functional Applications - Warehouse Management Systems (WMS)
Applicable Industries
- Food & Beverage
Applicable Functions
- Logistics & Transportation
- Warehouse & Inventory Management
Use Cases
- Inventory Management
- Predictive Maintenance
- Warehouse Automation
Services
- System Integration
- Training
About The Customer
Parmalat is a global provider of world-class dairy and other food products, with more than 36,000 employees in 29 countries around the world, and annual revenue in Australia in excess of $1.4 billion. Parmalat Australia has 2,500 employees who work closely with around 500 Australian farmers to produce leading dairy products, including Pauls Milk, Ice Break Iced Coffee, Vaalia yoghurt, Oak and Breaka flavoured milk. Parmalat is one of Australia’s largest dairy producers and in 2014 was named Woolworths’ Core Fresh Supplier of the Year. Part of their Mission is to invest in and grow the Australian dairy industry, while also promoting Australia as a high quality producer for the Asia region.
The Challenge
In the past, Parmalat’s Lidcombe distribution centre (DC) relied on manual, paper-based processes to direct their pickers. The disadvantage of Parmalat’s old system was a lack of visibility of the warehouse operations. Parmalat was seeking improvement in the utilisation of labour and in order to achieve that, it needed greater operational visibility and control. Increased visibility and control would offer Parmalat the ability manage which tasks were completed by which worker and in what order. Seth van Dijk, Sales Manager, Real-time Logistics at Dematic, said Parmalat initially enlisted them to investigate how technology could help them optimise their current processes. “The basis of Dematic’s initial investigation on the DC floor was for us to look at what was traditionally a paper-based process, and to determine how we could implement technology to help speed that up,” Seth said. “Following the consideration of a number of different technologies, it was determined that voice picking was the optimal solution.”
The Solution
The new voice picking process is paperless, which means operators no longer need to look away from what they are doing or go back and forth picking up new pick slips. It is also easy for workers to be trained up, so they can hit the warehouse floor sooner. “With our new voice system, when an order drops into the system the operator will pick up the transfer order, they will then go to the location, confirm with the check-digit that they are at the right location,” explained Tony Behan, DC Trainer, Parmalat. “The system will then tell them to pick a certain amount of crates or units. From there they’ll pick it and the voice system will ask the worker if they picked the right amount. The system will keeping going through this process until the order is finished.” “Shipments are also now allocated and sent to several pickers on the floor, rather than just one under the previous system,” added Tony. “Picking is completed by multiple workers simultaneously, which greatly enhances Parmalat’s warehouse efficiency and productivity.” The new voice-directed smart SAP WMS solution also facilitates a real-time, two-way data flow between workers on the distribution floor and the WMS, making it easy for managers to generate reports, and to provide them with comprehensive and accurate insights on the operation – right down to an individual’s performance.
Operational Impact
Quantitative Benefit
Case Study missing?
Start adding your own!
Register with your work email and create a new case study profile for your business.
Related Case Studies.
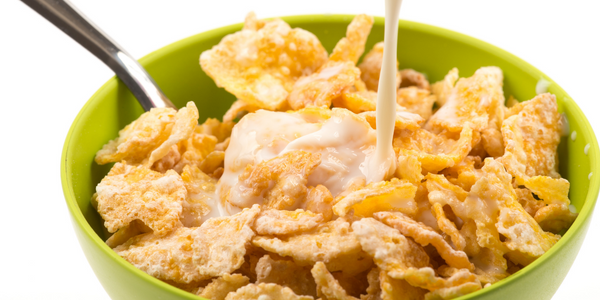
Case Study
The Kellogg Company
Kellogg keeps a close eye on its trade spend, analyzing large volumes of data and running complex simulations to predict which promotional activities will be the most effective. Kellogg needed to decrease the trade spend but its traditional relational database on premises could not keep up with the pace of demand.
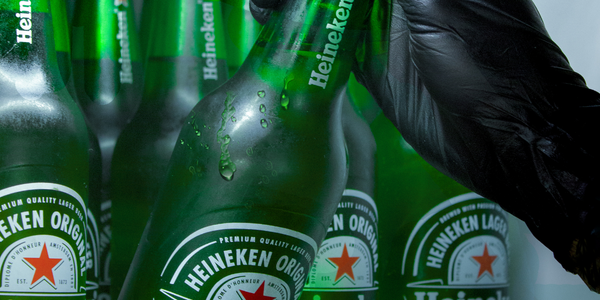
Case Study
HEINEKEN Uses the Cloud to Reach 10.5 Million Consumers
For 2012 campaign, the Bond promotion, it planned to launch the campaign at the same time everywhere on the planet. That created unprecedented challenges for HEINEKEN—nowhere more so than in its technology operation. The primary digital content for the campaign was a 100-megabyte movie that had to play flawlessly for millions of viewers worldwide. After all, Bond never fails. No one was going to tolerate a technology failure that might bruise his brand.Previously, HEINEKEN had supported digital media at its outsourced datacenter. But that datacenter lacked the computing resources HEINEKEN needed, and building them—especially to support peak traffic that would total millions of simultaneous hits—would have been both time-consuming and expensive. Nor would it have provided the geographic reach that HEINEKEN needed to minimize latency worldwide.
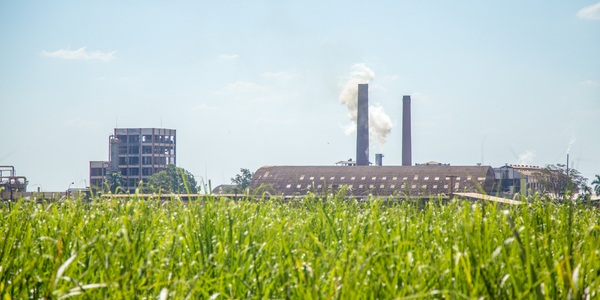
Case Study
Energy Management System at Sugar Industry
The company wanted to use the information from the system to claim under the renewable energy certificate scheme. The benefit to the company under the renewable energy certificates is Rs 75 million a year. To enable the above, an end-to-end solution for load monitoring, consumption monitoring, online data monitoring, automatic meter data acquisition which can be exported to SAP and other applications is required.
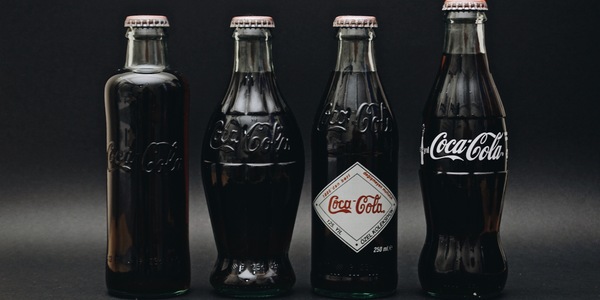
Case Study
Coca Cola Swaziland Conco Case Study
Coco Cola Swaziland, South Africa would like to find a solution that would enable the following results: - Reduce energy consumption by 20% in one year. - Formulate a series of strategic initiatives that would enlist the commitment of corporate management and create employee awareness while helping meet departmental targets and investing in tools that assist with energy management. - Formulate a series of tactical initiatives that would optimize energy usage on the shop floor. These would include charging forklifts and running cold rooms only during off-peak periods, running the dust extractors only during working hours and basing lights and air-conditioning on someone’s presence. - Increase visibility into the factory and other processes. - Enable limited, non-intrusive control functions for certain processes.
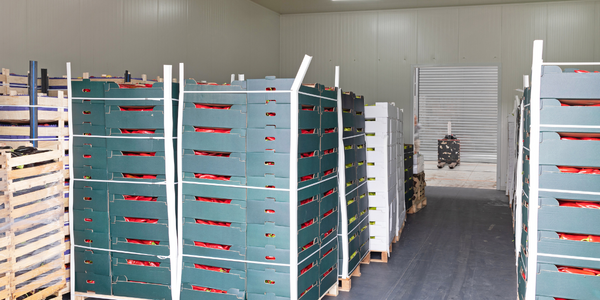
Case Study
Temperature Monitoring for Restaurant Food Storage
When it came to implementing a solution, Mr. Nesbitt had an idea of what functionality that he wanted. Although not mandated by Health Canada, Mr. Nesbitt wanted to ensure quality control issues met the highest possible standards as part of his commitment to top-of-class food services. This wish list included an easy-to use temperature-monitoring system that could provide a visible display of the temperatures of all of his refrigerators and freezers, including historical information so that he could review the performance of his equipment. It also had to provide alert notification (but email alerts and SMS text message alerts) to alert key staff in the event that a cooling system was exceeding pre-set warning limits.
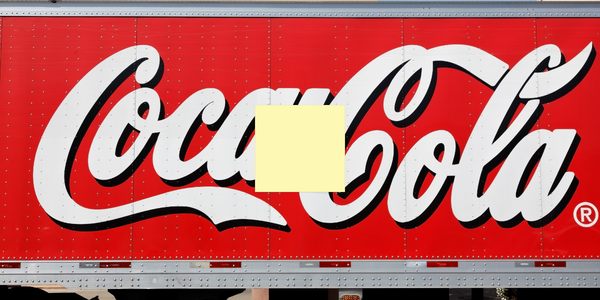
Case Study
Coca-Cola Refreshments, U.S.
Coca-Cola Refreshments owns and manages Coca-Cola branded refrigerators in retail establishments. Legacy systems were used to locate equipment information by logging onto multiple servers which took up to 8 hours to update information on 30-40 units. The company had no overall visibility into equipment status or maintenance history.