Technology Category
- Analytics & Modeling - Digital Twin / Simulation
- Sensors - Autonomous Driving Sensors
Applicable Industries
- Automotive
- Electrical Grids
Applicable Functions
- Product Research & Development
- Warehouse & Inventory Management
Use Cases
- Last Mile Delivery
- Virtual Reality
About The Customer
Porsche AG is a globally recognized automotive company known for its high-performance cars. In response to the challenge of E-mobility, Porsche is developing high-performance electric powertrains that meet every Porsche standard in terms of performance, fuel efficiency, driving dynamics, and everyday practicality. The company is committed to improving the total design balance in e-motor development and is keen on adopting more integrated and holistic development strategies to better meet future requirements without significant sacrifices on target fulfillment. Porsche is dedicated to innovation and is always looking for ways to enhance its products and services to provide the best possible experience for its customers.
The Challenge
Porsche AG, a renowned automotive company, was faced with the challenge of improving the total design balance in e-motor development. The powertrain of electric vehicles had to be developed considering an increasing number of internal, customer, and legal requirements. Classical development strategies involved individual development routes for different requirements and different organizational structures responsible for fulfilling these requirements. This led to development taking place in several parallel disciplines, often resulting in negotiations and unfavorable compromises to reach a final acceptable design. Porsche aimed to adopt more integrated and holistic development strategies to better meet future requirements without significant sacrifices on target fulfillment. The challenge was to design optimization strategies that accounted for different requirements resulting from different physical phenomena simultaneously, i.e., multiphysics optimization.
The Solution
Porsche AG partnered with Altair, a software and consulting company specializing in simulation, optimization, and high-performance computing, to tackle the challenge of improving the total design balance in e-motor development. Altair's suite of tools, including Altair Flux, Altair FluxMotor, Altair OptiStruct, and Altair Activate, were used to create a process for multiphysics e-motor optimization. The classical motor efficiency/power design problem was coupled with other physics to account for thermal effects, structural boundary conditions, and vibrations. The effects of the inverter on the motor performance were also evaluated by integrating both controls and physical modeling. The design optimization aimed to maximize torque and power under defined driving conditions while keeping rotor stresses, motor vibrations, and motor temperature within certain limits. The design process accounted for both individual motor design points and evaluation in standardized driving cycles using reduced order models based on data provided by full-order models in the Altair suite of tools.
Operational Impact
Case Study missing?
Start adding your own!
Register with your work email and create a new case study profile for your business.
Related Case Studies.
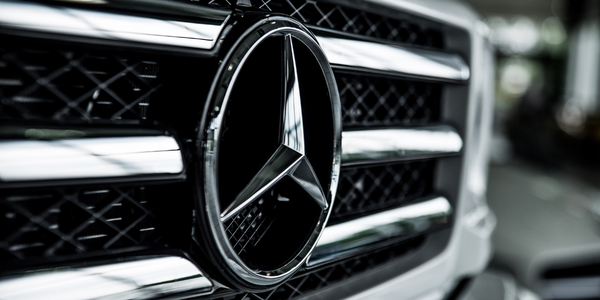
Case Study
Integral Plant Maintenance
Mercedes-Benz and his partner GAZ chose Siemens to be its maintenance partner at a new engine plant in Yaroslavl, Russia. The new plant offers a capacity to manufacture diesel engines for the Russian market, for locally produced Sprinter Classic. In addition to engines for the local market, the Yaroslavl plant will also produce spare parts. Mercedes-Benz Russia and his partner needed a service partner in order to ensure the operation of these lines in a maintenance partnership arrangement. The challenges included coordinating the entire maintenance management operation, in particular inspections, corrective and predictive maintenance activities, and the optimizing spare parts management. Siemens developed a customized maintenance solution that includes all electronic and mechanical maintenance activities (Integral Plant Maintenance).

Case Study
Hydro One Leads the Way In Smart Meter Development
In 2010, Ontario’s energy board mandated that time-of-use (TOU) pricing for consumers be available for all consumers on a regulated price plan. To meet this requirement, Hydro One needed to quickly deploy a smart meter and intelligent communications network solution to meet the provincial government’s requirement at a low cost. The network needed to cover Hydro One’s expansive service territory, which has a land mass twice the size of Texas, and its customers live in a mix of urban, rural, and remote areas, some places only accessible by air, rail, boat or snowmobile. Most importantly, the network needed to enable future enterprise-wide business efficiencies, modernization of distribution infrastructure and enhanced customer service. To meet these needs, Hydro One conceptualized an end-to-end solution leveraging open standards and Internet Protocols (IP) at all communication levels. The utility drew upon industry leaders like Trilliant to realize this vision.

Case Study
Monitoring of Pressure Pumps in Automotive Industry
A large German/American producer of auto parts uses high-pressure pumps to deburr machined parts as a part of its production and quality check process. They decided to monitor these pumps to make sure they work properly and that they can see any indications leading to a potential failure before it affects their process.