Customer Company Size
Large Corporate
Region
- America
Country
- Mexico
Product
- EcoStruxure™ Asset Advisor
- Model 6 Motor Control Center from Square D™
- LV Prisma panels
- Trihal transformers
- QDLogic switchboards
- PowerLogic™ meters
- MasterPacT™ circuit breakers
Tech Stack
- IoT
- Cloud
- Wi-Fi connectivity
Implementation Scale
- Enterprise-wide Deployment
Impact Metrics
- Productivity Improvements
- Customer Satisfaction
- Cost Savings
Technology Category
- Infrastructure as a Service (IaaS) - Cloud Computing
- Networks & Connectivity - WiFi
Applicable Functions
- Facility Management
Use Cases
- Building Automation & Control
- Building Energy Management
- Predictive Maintenance
Services
- Cloud Planning, Design & Implementation Services
- System Integration
About The Customer
Hyatt Regency Mexico City is one of the city’s largest hotels, located in one of the city’s most exclusive areas. The hotel spans 44 floors and is 144 meters tall, with an average of 20,000 guests per month. Since the hotel’s beginnings in 1957, Hyatt has been on a mission to ensure the well-being of its guests, partners, and associates. “For us, the most important thing is people, whether they’re our guests or not,” says Christophe Lorvo, General Manager and Area Vice President at Hyatt Regency Mexico City (HRMC). “This way of working allows us to provide a much more welcoming stay and achieve our mission of delivering unforgettable experiences.
The Challenge
Hyatt Regency® Mexico City needed to modernize its power equipment without disrupting the guest experience. The hotel had the infrastructure it needed for daily operations but lacked visibility into the status of crucial power equipment, such as transformers. Without real-time monitoring of the state of the electrical system, the hotel risked power failures that could compromise the guest experience, and the risks only increased as energy demands grew. But the hotel faced another problem — its existing equipment wasn’t designed to guarantee constant power during maintenance or repair activity. Power outages weren’t an option; any type of disruption could negatively impact the guest experience, from the guest staying on the top floor to those attending events hosted in the hotel’s conference areas. To maintain the hospitality experience — and to keep its reputation intact — HRMC needed to ensure reliable power around the clock.
The Solution
The hotel modernized its power infrastructure with a Model 6 Motor Control Center from Square D™ by Schneider Electric, LV Prisma panels, Trihal transformers, QDLogic switchboards, PowerLogic™ meters, and MasterPacT™ circuit breakers — all of which can be managed remotely through EcoStruxure™ Asset Advisor. The Schneider Electric team concluded it would be most profitable long-term to upgrade all substation equipment. This way, HRMC could ensure integration and cohesion of current, as well as future, systems that would allow greater control. These new additions would drastically reduce future technical inspections and general maintenance. Old transformers were exchanged for Trihal transformers — next-generation, high-performance solutions with Wi-Fi connectivity and IoT capabilities. Existing control panels were replaced with QDLogic low-voltage switchboards, which feature the most reliable electronic and thermomagnetic switches, with ISO90001 and ISO14000 quality certifications. The QDLogic switchboards include PowerLogic PM8000 series measurement and monitoring equipment, which allow Hyatt to forecast energy requirements and accurately allocate or sub-invoice consumption costs. In addition, the key performance indicators that PowerLogic provides helps the hotel discover the best ways to save energy, helping Hyatt meet its long-term consumption reduction goals.
Operational Impact
Quantitative Benefit
Case Study missing?
Start adding your own!
Register with your work email and create a new case study profile for your business.
Related Case Studies.
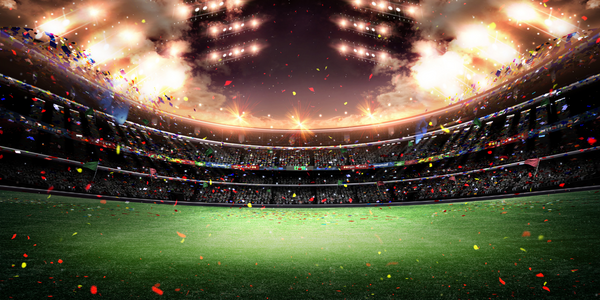
Case Study
Turning A Stadium Into A Smart Building
Honeywell created what it called the “intelligent system” for the National Stadium in Beijing, China, turning the venue for the opening and closing events at the 2008 Summer Olympics into a “smart building.” Designed by highly controversial artist Ai Weiwei, the “Bird’s Nest” remains one of the most impressive feats of stadium architecture in the world. The 250,000 square meter structure housed more than 100,000 athletes and spectators at a time. To accommodate such capacity, China turned to Honeywell’s EBI Integrated Building Management System to create an integrated “intelligent system” for improved building security, safety and energy efficiency.
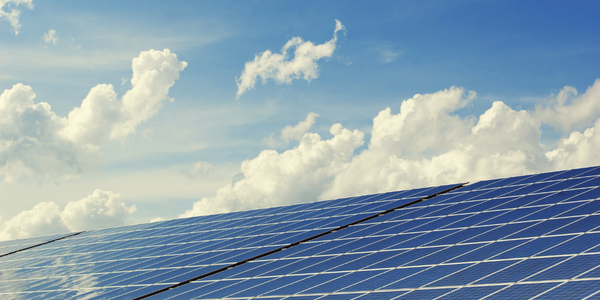
Case Study
Remote Monitoring & Predictive Maintenance App for a Solar Energy System
The maintenance & tracking of various modules was an overhead for the customer due to the huge labor costs involved. Being an advanced solar solutions provider, they wanted to ensure early detection of issues and provide the best-in-class customer experience. Hence they wanted to automate the whole process.
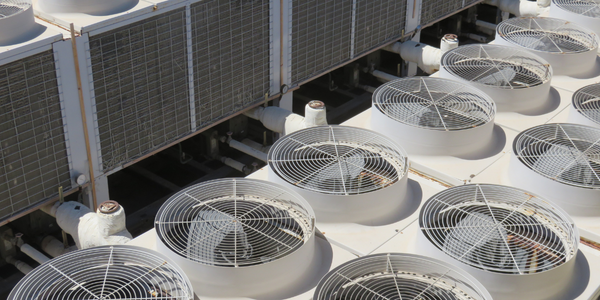
Case Study
Predictive Maintenance for Industrial Chillers
For global leaders in the industrial chiller manufacturing, reliability of the entire production process is of the utmost importance. Chillers are refrigeration systems that produce ice water to provide cooling for a process or industrial application. One of those leaders sought a way to respond to asset performance issues, even before they occur. The intelligence to guarantee maximum reliability of cooling devices is embedded (pre-alarming). A pre-alarming phase means that the cooling device still works, but symptoms may appear, telling manufacturers that a failure is likely to occur in the near future. Chillers who are not internet connected at that moment, provide little insight in this pre-alarming phase.
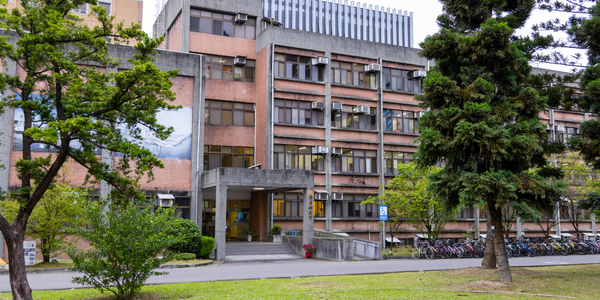
Case Study
Energy Saving & Power Monitoring System
Recently a university in Taiwan was experiencing dramatic power usage increases due to its growing number of campus buildings and students. Aiming to analyze their power consumption and increase their power efficiency across 52 buildings, the university wanted to build a power management system utilizing web-based hardware and software. With these goals in mind, they contacted Advantech to help them develop their system and provide them with the means to save energy in the years to come.
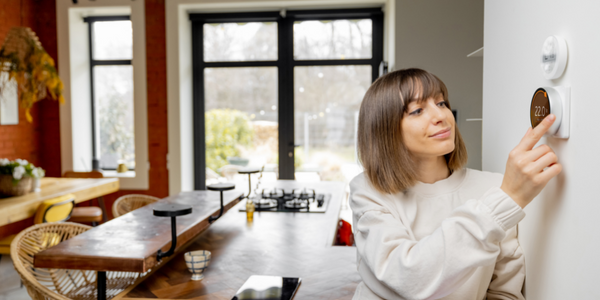
Case Study
BACnet enabled Wireless Temperature Monitoring System
Client offered a Temperature Monitoring System which consists of Wireless Transmitters and Application Software. Third party BACnet Application such as a Building Automation System needs access to vital parameter such as temperature, humidity, CO2, etc., measured by wireless sensor devices. Client needed a solution to allow data exchange from its Temperature Monitoring System with BMS.
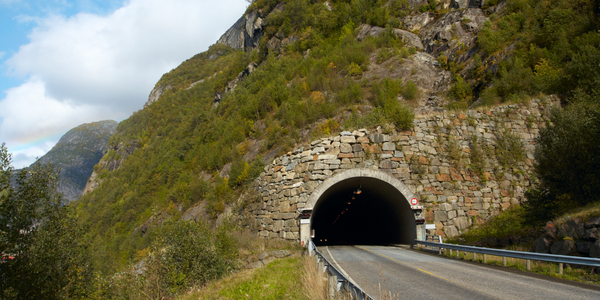
Case Study
IoT System for Tunnel Construction
The Zenitaka Corporation ('Zenitaka') has two major business areas: its architectural business focuses on structures such as government buildings, office buildings, and commercial facilities, while its civil engineering business is targeted at structures such as tunnels, bridges and dams. Within these areas, there presented two issues that have always persisted in regard to the construction of mountain tunnels. These issues are 'improving safety" and "reducing energy consumption". Mountain tunnels construction requires a massive amount of electricity. This is because there are many kinds of electrical equipment being used day and night, including construction machinery, construction lighting, and ventilating fan. Despite this, the amount of power consumption is generally not tightly managed. In many cases, the exact amount of power consumption is only ascertained when the bill from the power company becomes available. Sometimes, corporations install demand-monitoring equipment to help curb the maximum power demanded. However, even in these cases, the devices only allow the total volume of power consumption to be ascertained, or they may issue warnings to prevent the contracted volume of power from being exceeded. In order to tackle the issue of reducing power consumption, it was first necessary to obtain an accurate breakdown of how much power was being used in each particular area. In other words, we needed to be able to visualize the amount of power being consumed. Safety, was also not being managed very rigorously. Even now, tunnel construction sites often use a 'name label' system for managing entry into the work site. Specifically, red labels with white reverse sides that bear the workers' names on both sides are displayed at the tunnel work site entrance. The workers themselves then flip the name label to the appropriate side when entering or exiting from the work site to indicate whether or not they are working inside the tunnel at any given time. If a worker forgets to flip his or her name label when entering or exiting from the tunnel, management cannot be performed effectively. In order to tackle the challenges mentioned above, Zenitaka decided to build a system that could improve the safety of tunnel construction as well as reduce the amount of power consumed. In other words, this new system would facilitate a clear picture of which workers were working in each location at the mountain tunnel construction site, as well as which processes were being carried out at those respective locations at any given time. The system would maintain the safety of all workers while also carefully controlling the electrical equipment to reduce unnecessary power consumption. Having decided on the concept, our next concern was whether there existed any kind of robust hardware that would not break down at the construction work site, that could move freely in response to changes in the working environment, and that could accurately detect workers and vehicles using radio frequency identification (RFID). Given that this system would involve many components that were new to Zenitaka, we decided to enlist the cooperation of E.I.Sol Co., Ltd. ('E.I.Sol') as our joint development partner, as they had provided us with a highly practical proposal.