Customer Company Size
Large Corporate
Region
- Europe
Country
- Spain
Product
- QlikView
Tech Stack
- SAP/R3
- Oracle
- CRM
Implementation Scale
- Enterprise-wide Deployment
Impact Metrics
- Productivity Improvements
- Cost Savings
Technology Category
- Analytics & Modeling - Real Time Analytics
Use Cases
- Supply Chain Visibility
- Real-Time Location System (RTLS)
Services
- System Integration
- Software Design & Engineering Services
About The Customer
Schenker España is a subsidiary of Deutsche Bahn (DB) Schenker, one of the leading global integrated logistics service providers. With 91,000 employees in 2,000 offices in 130 countries, DB Schenker manages all the DB Group’s transport and logistics activities. Schenker España, headquartered in Barcelona, is one of the leading Spanish shipping companies. It has an impressive network throughout Spain, and customers say it provides the best integrated service offered by any single operator in this market. Schenker España has 37 offices, 75 branches, and around 140,000 square metres of storage space in the Iberian Peninsula, the Balearic Isles, and the Canaries. The subsidiary also has a branch in Santo Domingo in the Dominican Republic and Havana, Cuba, in addition to a Shanghai branch. Schenker España specialises in logistics services for air and sea shipping companies around the world, European land transport, international fairs and sports events, industrial projects, aero engine parts and marine parts. It offers integrated logistics solutions throughout the supply chain for the consumer, industrial, electronic, automation and pharmaceuticals sectors.
The Challenge
Schenker España, a leading Spanish shipping company and a subsidiary of Deutsche Bahn (DB) Schenker, was in need of a global information analysis system that could be deployed in the shortest time possible. The company uses diverse technology platforms, each with corporate applications for each specific business area, and an SAP/R3 enterprise resource planning (ERP) system for financial and logistics management. These platforms include Windows, Citrix, VMWare, Oracle, and various UNIX/Linux-based systems. The company had evaluated various business intelligence (BI) tools and began to develop a pilot project with Business Objects, though this never became a reality. In addition, it had spent most of its available resources in the early stages.
The Solution
Schenker España opted for QlikView on the recommendation of other European DB Schenker subsidiaries. Managers were impressed by the ease with which data can be input, its rapid deployment, and the cost effectiveness of the software. A work team comprising engineers from the company’s IT department and QlikView consultants managed the development and deployment of the QlikView solution. After the pilot stage, lasting just a few weeks, the first applications were installed with satisfactory results. The first analytical applications introduced by Schenker España using QlikView provided it with business analysis functions, customer relationship management (CRM) support, provider management, and information on warehouse analysis and operations. Deployment continued incrementally for each of the company’s business divisions: land, air, and sea transport, logistics, commercial and management departments, and included finance and accounting.
Operational Impact
Case Study missing?
Start adding your own!
Register with your work email and create a new case study profile for your business.
Related Case Studies.
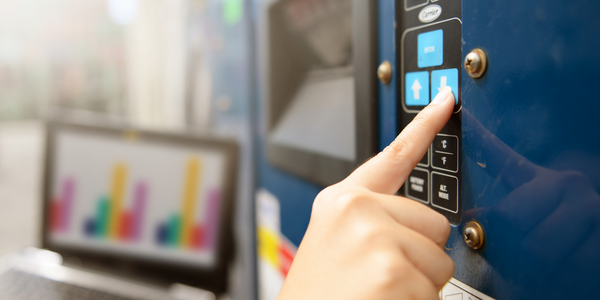
Case Study
Remote Temperature Monitoring of Perishable Goods Saves Money
RMONI was facing temperature monitoring challenges in a cold chain business. A cold chain must be established and maintained to ensure goods have been properly refrigerated during every step of the process, making temperature monitoring a critical business function. Manual registration practice can be very costly, labor intensive and prone to mistakes.
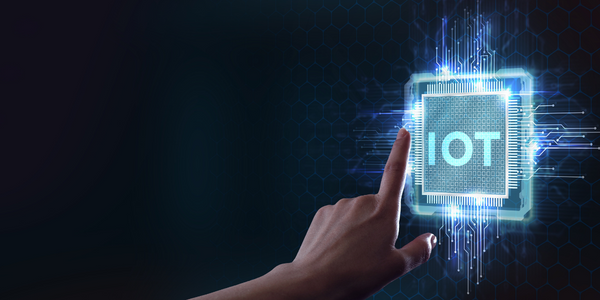
Case Study
Leading Tools Manufacturer Transforms Operations with IoT
Stanley Black & Decker required transparency of real-time overall equipment effectiveness and line productivity to reduce production line change over time.The goal was to to improve production to schedule, reduce actual labor costs and understanding the effects of shift changes and resource shifts from line to line.
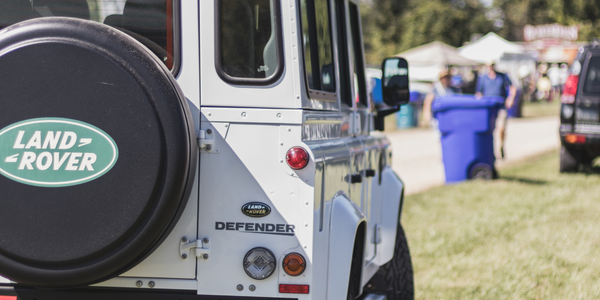
Case Study
Jaguar Land Rover Speeds Order-to-Cash Cycle
At Jaguar Land Rover, vehicles physically move around the facility for testing, configuration setting, rework and rectification, leading to a longer search time to get each vehicle to its next process facility. The main goal is to minimize the vehicles' dwell time between end of line and the delivery chain which was previously a manually intensive process. Jaguar Land Rover's goal was to build on the success of an earlier RFID project and improve the efficiency of delivering vehicles to meet dealer orders.
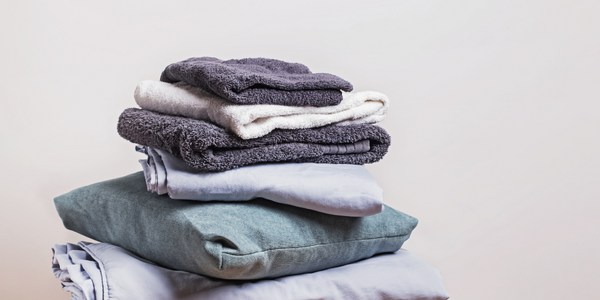
Case Study
Retail Uses RFID to Enable Cold Chain Monitoring
Like most grocery retailers, Hy-Vee is faced with the challenge of providing the highest quality products to its shoppers. Shoppers want the longest possible shelf life from perishable products and expect a consistent product experience each time they shop. Controlling the quality of products sold leads to shopper loyalty, which is of paramount importance to the success of Hy-Vee. Before products arrive in stores, Hy-Vee's distribution centers (DCs) handle items including dairy products, fresh meats, seafood, deli items, produce and frozen goods, all of which have different temperature needs and sensitivities. During transit from suppliers to DCs, Hy-Vee has limited visibility and temperature management abilities due to large amount of supplier managed transportation. For instance, during a week-long transit, a supplier's carrier equipment may malfunction, causing an item to thaw and then refreeze once repairs are made. Hy-Vee sought help from TempTRIP, an RFID solution provider that focuses on shipping, storage, receiving, and temperature control. TempTRIP's EPC RFID tags use Impinj chips to monitor and report temperature readings throughout the shipping and receiving process. The tags can also be re-configured and re-used, a unique feature within the current market of temperature monitoring devices.