Customer Company Size
Large Corporate
Region
- Asia
Country
- China
Product
- QlikView
Tech Stack
- Business Intelligence
Implementation Scale
- Departmental Deployment
Impact Metrics
- Cost Savings
- Productivity Improvements
Technology Category
- Analytics & Modeling - Real Time Analytics
Applicable Industries
- Automotive
Applicable Functions
- Procurement
- Warehouse & Inventory Management
Use Cases
- Inventory Management
- Supply Chain Visibility
Services
- Software Design & Engineering Services
About The Customer
Anji-TNT Automotive Logistics Co. Ltd. is the first automotive logistics joint venture established in China between the Shanghai Automotive Industry Sales Corporation (SAISC) and CEVA Logistics (TNT Logistics), a subsidiary of Apollo. Anji-TNT offers logistical services for both automotives and their parts. It also provides logistics training, technical support, logistics planning, and logistical management. The company has a workforce of 4,300 employees and operates in the logistics industry.
The Challenge
Anji-TNT Automotive Logistics Co. Ltd., a joint venture between the Shanghai Automotive Industry Sales Corporation (SAISC) and CEVA Logistics (TNT Logistics), was in need of a Business Intelligence (BI) solution to manage the inventory of raw materials, parts, equipment, and finished products efficiently and effectively. The company had previously adopted a competitor's solution, which proved to be complicated to deploy and difficult for end users to navigate. After comparing different vendors' solutions in terms of cost and performance, Anji-TNT selected QlikView.
The Solution
Anji-TNT implemented QlikView in the first stage in its procurement department in China for supply chain analysis. The solution was used to plan the demand for different raw materials and parts, analyze procurement and supplier performance, manage inventory and warehouse, as well as analyze logistics and fulfillment. QlikView was adopted due to its simple and rapid implementation process, which took only two months, three times faster than other competitive solutions.
Operational Impact
Quantitative Benefit
Case Study missing?
Start adding your own!
Register with your work email and create a new case study profile for your business.
Related Case Studies.
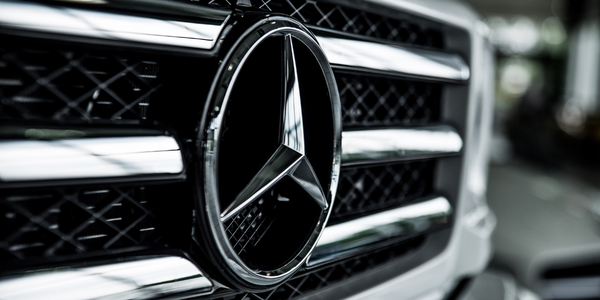
Case Study
Integral Plant Maintenance
Mercedes-Benz and his partner GAZ chose Siemens to be its maintenance partner at a new engine plant in Yaroslavl, Russia. The new plant offers a capacity to manufacture diesel engines for the Russian market, for locally produced Sprinter Classic. In addition to engines for the local market, the Yaroslavl plant will also produce spare parts. Mercedes-Benz Russia and his partner needed a service partner in order to ensure the operation of these lines in a maintenance partnership arrangement. The challenges included coordinating the entire maintenance management operation, in particular inspections, corrective and predictive maintenance activities, and the optimizing spare parts management. Siemens developed a customized maintenance solution that includes all electronic and mechanical maintenance activities (Integral Plant Maintenance).

Case Study
Monitoring of Pressure Pumps in Automotive Industry
A large German/American producer of auto parts uses high-pressure pumps to deburr machined parts as a part of its production and quality check process. They decided to monitor these pumps to make sure they work properly and that they can see any indications leading to a potential failure before it affects their process.