Customer Company Size
Large Corporate
Region
- Europe
Country
- Sweden
Product
- QlikView
Tech Stack
- Data Analysis
- Data Visualization
Implementation Scale
- Enterprise-wide Deployment
Impact Metrics
- Cost Savings
- Productivity Improvements
Technology Category
- Application Infrastructure & Middleware - Data Visualization
Use Cases
- Inventory Management
- Supply Chain Visibility
Services
- Data Science Services
About The Customer
Frigoscandia Distribution AB is a leading logistics partner in the food industry. The company is fully owned by the Norwegian Post and the business is focused on transportation and storage of chilled, dried and frozen products. One of its larger customers is IKEA for whom Frigoscandia manages food logistics all over the world. Ulf Carlsson is the manager of the administrative functions at Frigoscandia and responsible for the corporate QlikView applications. He was also responsible for the evaluation that was carried out in the spring of 2004 that lead to the choice of QlikView as the coordinating analysis and presentation tool for the entire company. Now, several years later, more or less all of the corporate functions are connected to QlikView.
The Challenge
Frigoscandia Distribution, a leading logistics partner in the food industry, was facing several challenges. They wanted to increase control over accounts payable by providing customer-facing employees with accurate payment histories. They also aimed to streamline purchasing processes to lower purchasing costs and improve cash flow. Additionally, they needed to reconcile redundant and outdated data to improve operational efficiency. The company was looking for a solution that could help them achieve these goals and improve their overall business operations.
The Solution
Frigoscandia deployed QlikView to 150 employees and various customers in record time. With QlikView across 4 functional areas, Frigoscandia now analyzes everything from customer profitability to supply chain efficiency to human resources’ effectiveness – all focused on driving corporate profitability. With QlikView Server and Publisher, management can now access a map that graphically shows results for all business units and allows managers to drill down to more detailed information for further analysis. The company used QlikView to improve the quality of their data by defining criteria for what a customer is, reducing the number of entries in the customer database from 24,000 to 4,000. The same method was used to reduce the supplier list from 14,000 to 3,000. By comparing the in-house databases with official business information, it was possible to use QlikView for automatic correction of errors like customer names or addresses.
Operational Impact
Quantitative Benefit
Case Study missing?
Start adding your own!
Register with your work email and create a new case study profile for your business.
Related Case Studies.
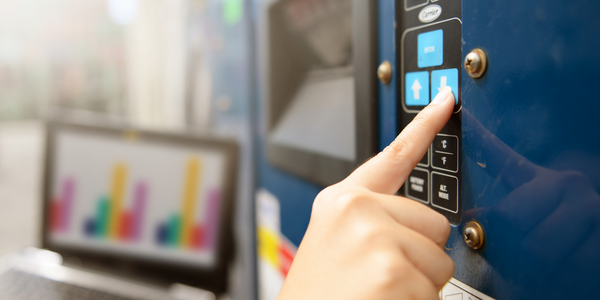
Case Study
Remote Temperature Monitoring of Perishable Goods Saves Money
RMONI was facing temperature monitoring challenges in a cold chain business. A cold chain must be established and maintained to ensure goods have been properly refrigerated during every step of the process, making temperature monitoring a critical business function. Manual registration practice can be very costly, labor intensive and prone to mistakes.
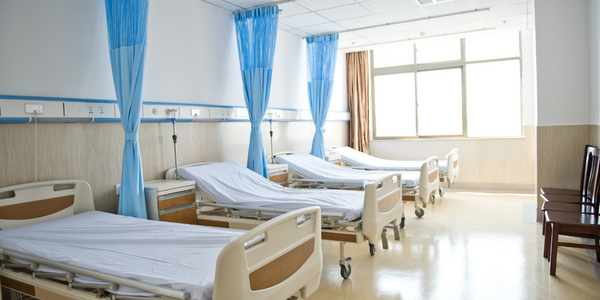
Case Study
Hospital Inventory Management
The hospital supply chain team is responsible for ensuring that the right medical supplies are readily available to clinicians when and where needed, and to do so in the most efficient manner possible. However, many of the systems and processes in use at the cancer center for supply chain management were not best suited to support these goals. Barcoding technology, a commonly used method for inventory management of medical supplies, is labor intensive, time consuming, does not provide real-time visibility into inventory levels and can be prone to error. Consequently, the lack of accurate and real-time visibility into inventory levels across multiple supply rooms in multiple hospital facilities creates additional inefficiency in the system causing over-ordering, hoarding, and wasted supplies. Other sources of waste and cost were also identified as candidates for improvement. Existing systems and processes did not provide adequate security for high-cost inventory within the hospital, which was another driver of cost. A lack of visibility into expiration dates for supplies resulted in supplies being wasted due to past expiry dates. Storage of supplies was also a key consideration given the location of the cancer center’s facilities in a dense urban setting, where space is always at a premium. In order to address the challenges outlined above, the hospital sought a solution that would provide real-time inventory information with high levels of accuracy, reduce the level of manual effort required and enable data driven decision making to ensure that the right supplies were readily available to clinicians in the right location at the right time.