- Sensors - Chemical Sensors
- Sensors - Liquid Detection Sensors
- Packaging
- Retail
- Logistics & Transportation
- Procurement
- Intelligent Packaging
- Inventory Management
Quimtia is a company with over 55 years of experience in the production and distribution of chemical products. With more than 300 employees, Quimtia caters to the various needs and demands of the chemical industry through its four lines of business, including food & pharma, feed, and industrial. The company has subsidiaries in Brazil, Peru, Colombia, and Argentina, and exports its products throughout the Americas. Quimtia is committed to continually improving its processes and has a clear commitment to the AuraQuantic solution.
Quimtia, a company specializing in the production and distribution of chemical products, was facing significant inefficiencies in its export processes. The process was not functioning optimally due to the high level of manual tasks involved, causing numerous disadvantages in the daily operations of foreign trade. The entire process, from order placement in SAP, order planning, packing list generation, internal and external management, to the final delivery to the customer, was cumbersome and time-consuming. The management team recognized the need for a technological solution that could streamline and control the entire process, reducing the manual workload and accelerating management times.
Quimtia's management team sought the help of Daya+, a technology consultancy firm specializing in process automation. They implemented AuraQuantic, a leading intelligent business process management suite (iBPMS), to automate all tasks involved in the different stages of the export process. The iBPM suite has improved the export process in several ways. It has increased productivity by reducing the registration phase of new orders and sending automated alerts to sales, planning, and foreign trade areas. The centralized management of all data, with digitized documents and storage, has resulted in an efficient system that guarantees optimal storage, organization, dissemination, and preservation. The export process now follows a workflow model, divided into six phases, ensuring tasks are executed in line with predefined rules and timing, thereby improving performance levels and promoting company growth.
Case Study missing?
Start adding your own!
Register with your work email and create a new case study profile for your business.
Related Case Studies.
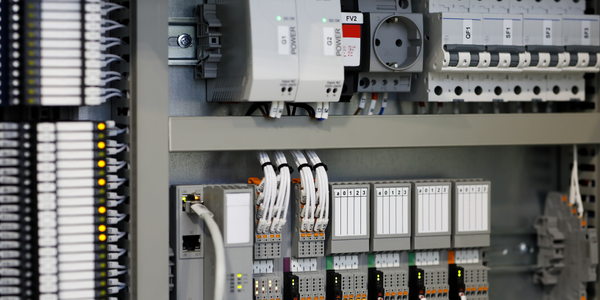
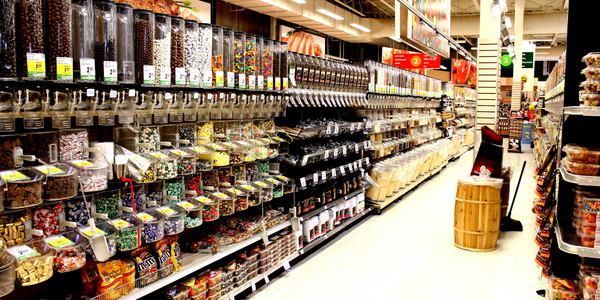

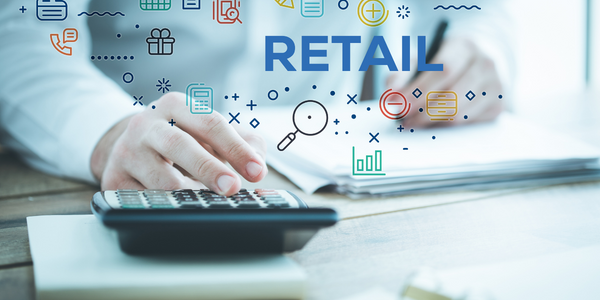
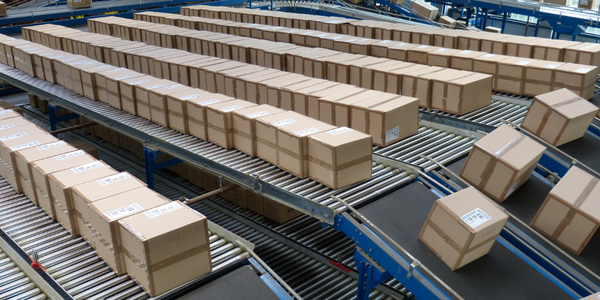