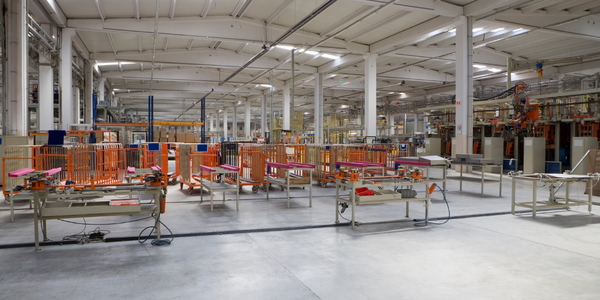
Technology Category
- Application Infrastructure & Middleware - Database Management & Storage
- Infrastructure as a Service (IaaS) - Cloud Databases
Applicable Industries
- Cement
- Equipment & Machinery
Applicable Functions
- Maintenance
- Product Research & Development
Use Cases
- Additive Manufacturing
- Root Cause Analysis & Diagnosis
Services
- System Integration
- Training
The Customer
JSW Steel Ltd
About The Customer
JSW is a multi-billion dollar company that has played a significant role in India’s growth in the steel, energy, cement, and infrastructure industries. The company prides itself on its differentiated product mix, state-of-the-art technology, excellence in execution, and focus on sustainability. JSW's steel manufacturing is spread across multiple plants, each housing a variety of machines equipped with numerous sensors tracking multiple data points. These machines generate a vast amount of data, including field maintenance, material consumption, and machine usage, which is then transferred to central Oracle databases.
The Challenge
JSW, a multi-billion dollar company, is a key player in India’s steel, energy, cement, and infrastructure industries. The company's steel manufacturing is spread across multiple plants, each housing dozens of machines with numerous sensors tracking multiple data points and supplying event data every 2-3 seconds. This data includes field maintenance, material consumption, and machine usage. Although the data is saved in each machine’s database and transferred to the central Oracle databases, the process had significant issues. Each machine used its own data protocols, making the data transfer processes 'closed' and lacking a standard way of reporting errors. As a result, some errors went unnoticed for a long time, leading to financial losses. For instance, the production of metal with incorrect dimensions could go unnoticed, resulting in significant waste and financial loss.
The Solution
JSW implemented OpenLegacy’s platform to generate microservice-based APIs that encapsulated the processes of transferring data between the machines and the central Oracle database. OpenLegacy generates standard Java code that is easily extended in any development environment, giving JSW's developers full flexibility to handle exceptions and errors with any level of granularity. They could, for example, send an email to a team when detecting one type of error, or simply log an error message for a less critical error type. Furthermore, JSW wanted to programmatically surface errors from the shop floor in their SAP ECC Quality Control module. OpenLegacy enabled this integration quickly and easily by supporting seamless data transfer from the sensors to the Oracle databases and to SAP.
Operational Impact
Quantitative Benefit
Case Study missing?
Start adding your own!
Register with your work email and create a new case study profile for your business.
Related Case Studies.
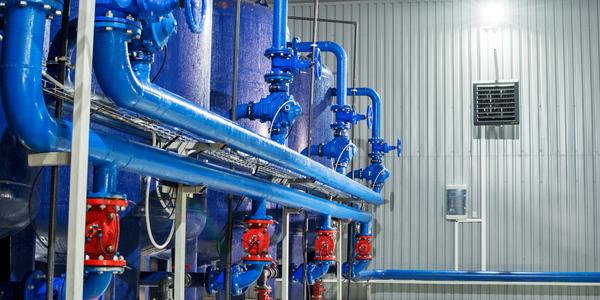
Case Study
Smart Water Filtration Systems
Before working with Ayla Networks, Ozner was already using cloud connectivity to identify and solve water-filtration system malfunctions as well as to monitor filter cartridges for replacements.But, in June 2015, Ozner executives talked with Ayla about how the company might further improve its water systems with IoT technology. They liked what they heard from Ayla, but the executives needed to be sure that Ayla’s Agile IoT Platform provided the security and reliability Ozner required.
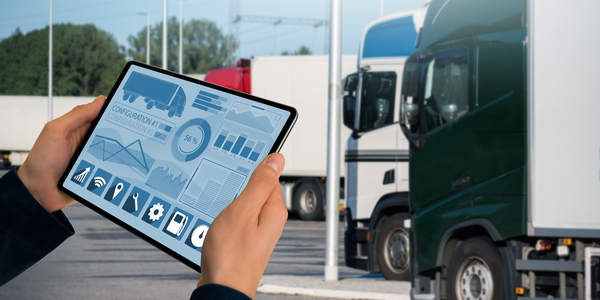
Case Study
IoT enabled Fleet Management with MindSphere
In view of growing competition, Gämmerler had a strong need to remain competitive via process optimization, reliability and gentle handling of printed products, even at highest press speeds. In addition, a digitalization initiative also included developing a key differentiation via data-driven services offers.
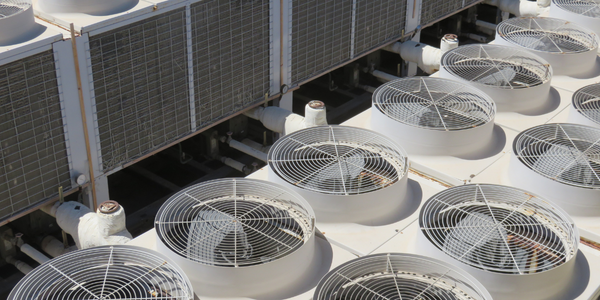
Case Study
Predictive Maintenance for Industrial Chillers
For global leaders in the industrial chiller manufacturing, reliability of the entire production process is of the utmost importance. Chillers are refrigeration systems that produce ice water to provide cooling for a process or industrial application. One of those leaders sought a way to respond to asset performance issues, even before they occur. The intelligence to guarantee maximum reliability of cooling devices is embedded (pre-alarming). A pre-alarming phase means that the cooling device still works, but symptoms may appear, telling manufacturers that a failure is likely to occur in the near future. Chillers who are not internet connected at that moment, provide little insight in this pre-alarming phase.
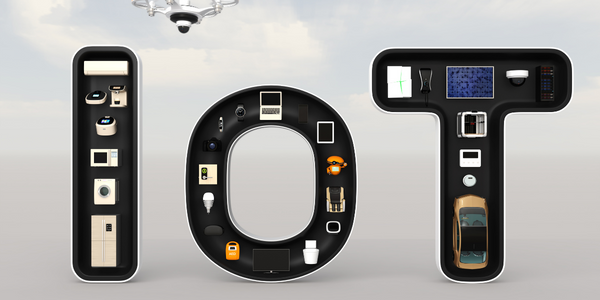
Case Study
Premium Appliance Producer Innovates with Internet of Everything
Sub-Zero faced the largest product launch in the company’s history:It wanted to launch 60 new products as scheduled while simultaneously opening a new “greenfield” production facility, yet still adhering to stringent quality requirements and manage issues from new supply-chain partners. A the same time, it wanted to increase staff productivity time and collaboration while reducing travel and costs.
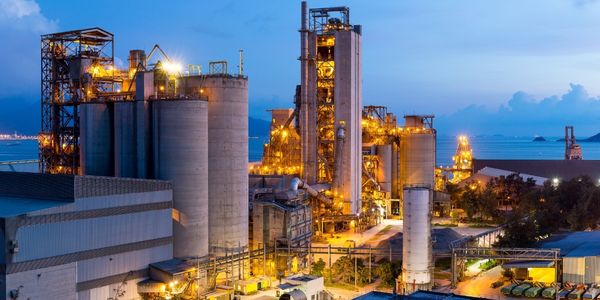
Case Study
System 800xA at Indian Cement Plants
Chettinad Cement recognized that further efficiencies could be achieved in its cement manufacturing process. It looked to investing in comprehensive operational and control technologies to manage and derive productivity and energy efficiency gains from the assets on Line 2, their second plant in India.
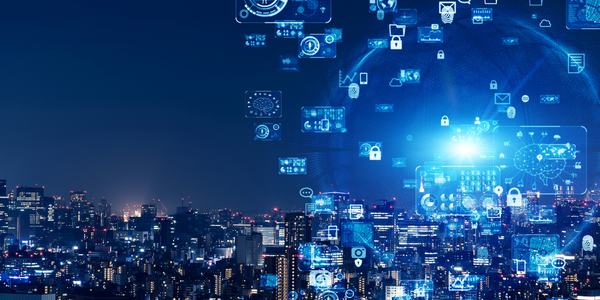
Case Study
Integration of PLC with IoT for Bosch Rexroth
The application arises from the need to monitor and anticipate the problems of one or more machines managed by a PLC. These problems, often resulting from the accumulation over time of small discrepancies, require, when they occur, ex post technical operations maintenance.