Technology Category
- Analytics & Modeling - Digital Twin / Simulation
- Robots - Autonomous Guided Vehicles (AGV)
Applicable Industries
- Automotive
- Life Sciences
Applicable Functions
- Product Research & Development
- Quality Assurance
Use Cases
- Virtual Reality
- Virtual Training
Services
- Testing & Certification
- Training
About The Customer
CalsonicKansei North America (CKNA) is part of the global automotive parts manufacturer, CalsonicKansei Corporation based in Japan. The company creates a wide range of automotive components including interior cockpits and center consoles. CKNA aims to develop high-end, innovative products and to continuously improve cost competitiveness. To achieve these goals, they are continuously evolving and improving their development processes. Computer aided engineering (CAE) plays a huge role in this capability. The use of CAE results in improved quality as well as reduced timing.
The Challenge
CalsonicKansei North America (CKNA), a part of the global automotive parts manufacturer, CalsonicKansei Corporation based in Japan, was facing a challenge with squeak and rattle (S&R) in vehicle interiors. This issue was affecting the quality of their products and customer satisfaction. Despite being experienced in modern Computer Aided Engineering (CAE) techniques, CKNA had not fully explored the potential of using simulation technologies to investigate S&R issues before physical hardware production. Squeak and rattle are two phenomena which occur when two parts of an assembly are in relative motion due to a specific excitation load. The lack of knowledge in S&R methodology was preventing early issue detection, leading to inefficiencies in product completion and potential warranty claims.
The Solution
CKNA approached Altair ProductDesign (PD) for training on the Squeak & Rattle Director (SnRD), a comprehensive set of software automations that rapidly identify and analyze design alternatives to eliminate the root causes of squeak and rattle in assemblies. Over time, the companies decided to work together to achieve more significant progress. Altair was able to offer the SnRD as well as insight into the methodology of squeak and rattle to better help CKNA correlate their simulation results with the actual performance of the products being developed. Altair provided perspective on the prerequisites required for such analyses, including which modeling techniques should be used, how to increase the fidelity of the finite element (FE) models, what kinds of loads should be applied, which methods are appropriate for correlation and prediction, etc. This collaboration resulted in a joint cockpit project, where each step of the modeling, simulation and test results analysis was completed hand-in-hand by the two companies.
Operational Impact
Quantitative Benefit
Case Study missing?
Start adding your own!
Register with your work email and create a new case study profile for your business.
Related Case Studies.
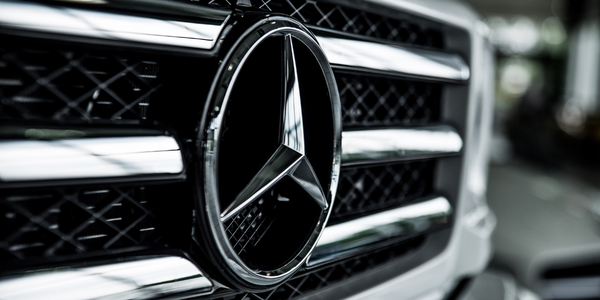
Case Study
Integral Plant Maintenance
Mercedes-Benz and his partner GAZ chose Siemens to be its maintenance partner at a new engine plant in Yaroslavl, Russia. The new plant offers a capacity to manufacture diesel engines for the Russian market, for locally produced Sprinter Classic. In addition to engines for the local market, the Yaroslavl plant will also produce spare parts. Mercedes-Benz Russia and his partner needed a service partner in order to ensure the operation of these lines in a maintenance partnership arrangement. The challenges included coordinating the entire maintenance management operation, in particular inspections, corrective and predictive maintenance activities, and the optimizing spare parts management. Siemens developed a customized maintenance solution that includes all electronic and mechanical maintenance activities (Integral Plant Maintenance).

Case Study
Monitoring of Pressure Pumps in Automotive Industry
A large German/American producer of auto parts uses high-pressure pumps to deburr machined parts as a part of its production and quality check process. They decided to monitor these pumps to make sure they work properly and that they can see any indications leading to a potential failure before it affects their process.