Applicable Industries
- Automotive
- Packaging
Applicable Functions
- Product Research & Development
- Quality Assurance
Use Cases
- Construction Management
- Experimentation Automation
Services
- System Integration
- Testing & Certification
About The Customer
Robo-Technology GmbH is an innovative, medium-sized company with many years of experience in the integration of complex robotics. Their scope ranges from nanometers up to several meters. Their customers operate in various industries, including automotive, aviation, metrology, pharmaceutical, packaging, and semi-conductor. These customers have a high level of confidence in Robo-Technology GmbH, relying on them for the planning, development, design, manufacturing, and programming of automatic robotic systems.
The Challenge
Robo-Technology GmbH, a company that specializes in the planning, development, design, manufacturing, and programming of automatic robotic systems, faced a significant challenge. They were tasked with developing an ultrasonic testing system for helicopter parts, which could be up to 6 meters in length. The system required two synchronized 6-axis robots to carry out fast testing movements with high dynamic precision and synchronization. This demanded the highest construction standards, posing a significant challenge for the company. The complexity of the task was further compounded by the need to ensure the rigidity and vibration behavior of the system met the customer's demands.
The Solution
Robo-Technology GmbH tackled this challenge by carrying out the development in a consistent 3-D environment. From the earliest stages of product development, they utilized ANSYS Workbench to analyze the design as work progressed. This approach allowed them to guarantee that the rigidity and vibration behavior of the system would meet the customer's demands. By using this method, the risk for the involved project partners was substantially reduced. The use of ANSYS Workbench also enabled quick verification of the efficiency of new construction elements, leading to shorter development and design times and a considerable increase in quality.
Operational Impact
Quantitative Benefit
Case Study missing?
Start adding your own!
Register with your work email and create a new case study profile for your business.
Related Case Studies.
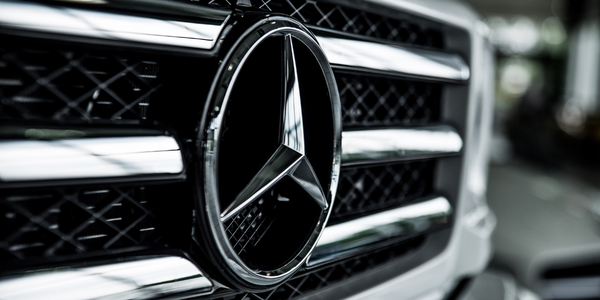
Case Study
Integral Plant Maintenance
Mercedes-Benz and his partner GAZ chose Siemens to be its maintenance partner at a new engine plant in Yaroslavl, Russia. The new plant offers a capacity to manufacture diesel engines for the Russian market, for locally produced Sprinter Classic. In addition to engines for the local market, the Yaroslavl plant will also produce spare parts. Mercedes-Benz Russia and his partner needed a service partner in order to ensure the operation of these lines in a maintenance partnership arrangement. The challenges included coordinating the entire maintenance management operation, in particular inspections, corrective and predictive maintenance activities, and the optimizing spare parts management. Siemens developed a customized maintenance solution that includes all electronic and mechanical maintenance activities (Integral Plant Maintenance).

Case Study
IoT Data Analytics Case Study - Packaging Films Manufacturer
The company manufactures packaging films on made to order or configure to order basis. Every order has a different set of requirements from the product characteristics perspective and hence requires machine’s settings to be adjusted accordingly. If the film quality does not meet the required standards, the degraded quality impacts customer delivery causes customer dissatisfaction and results in lower margins. The biggest challenge was to identify the real root cause and devise a remedy for that.

Case Study
Monitoring of Pressure Pumps in Automotive Industry
A large German/American producer of auto parts uses high-pressure pumps to deburr machined parts as a part of its production and quality check process. They decided to monitor these pumps to make sure they work properly and that they can see any indications leading to a potential failure before it affects their process.