Technology Category
- Other - Battery
- Processors & Edge Intelligence - Microcontrollers & Printed Circuit Boards
Applicable Industries
- Automotive
- Electronics
Applicable Functions
- Product Research & Development
- Quality Assurance
Use Cases
- Additive Manufacturing
- Manufacturing Process Simulation
Services
- Hardware Design & Engineering Services
About The Customer
Samsung SDI, headquartered in South Korea, is a global market leader in the high technology and environmental battery industry. With a 40-year history, Samsung SDI has evolved from vacuum tubes to large plasma display panels (PDPs), to high-tech cathode ray tubes (CRTs) and digital displays. Today, Samsung SDI is a top player as an energy and materials provider of rechargeable batteries for the IT, automotive, energy storage systems (ESS), and electronic material industries. The company recently transitioned to the electronic materials business, requiring a different approach to new electronic designs and related printed circuit board (PCB) manufacturing technologies.
The Challenge
Samsung SDI, a global leader in the high technology and environmental battery industry, faced several challenges when transitioning to the electronic materials business. The company had to shift from digital display control circuits to battery control circuits, necessitating a new approach to electronic designs and related printed circuit board (PCB) manufacturing technologies. A robust solution for PCB design review and verification was required for both existing and new products. Additionally, after acquiring a significant player in the automotive battery pack business, Samsung SDI needed a solution that could establish and deploy PCB design review and verification where the design rules and user environment were centrally managed.
The Solution
Samsung SDI evaluated Altair PollEx for PCB design review (PCB Modeler) and verification (PCB Verification), focusing on the supported design rules for manufacturing (DFM) and design for electrical engineering (DFE). The goal was to manage and enhance the process from design to manufacturing. PollEx's user-friendly collaboration capabilities allowed teams of PCB designers, hardware engineers, test engineers, and manufacturing engineers to communicate overseas. Samsung SDI required a solution that could be used by all branch locations while allowing the design rules and verification environment to be centrally managed. Altair worked closely with Samsung SDI engineers to ensure the PCB verification solution could be used for existing and new products with different verification requirements. After two months, Samsung SDI had an efficient collaboration environment with PCB verification capabilities that could be used by multiple teams.
Operational Impact
Quantitative Benefit
Case Study missing?
Start adding your own!
Register with your work email and create a new case study profile for your business.
Related Case Studies.
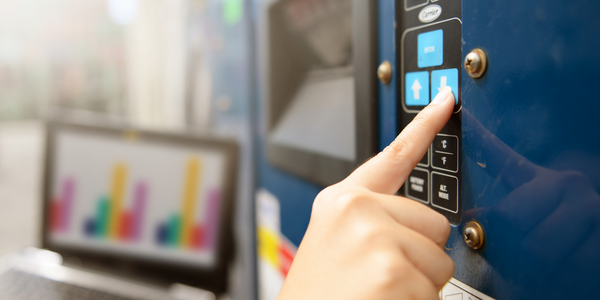
Case Study
Remote Temperature Monitoring of Perishable Goods Saves Money
RMONI was facing temperature monitoring challenges in a cold chain business. A cold chain must be established and maintained to ensure goods have been properly refrigerated during every step of the process, making temperature monitoring a critical business function. Manual registration practice can be very costly, labor intensive and prone to mistakes.
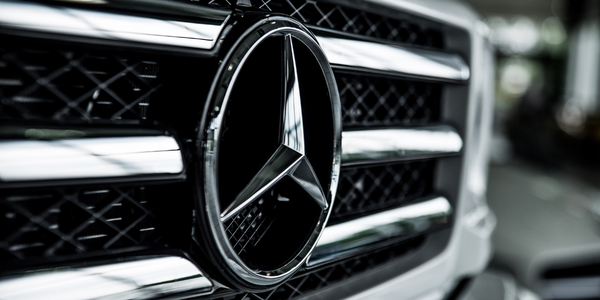
Case Study
Integral Plant Maintenance
Mercedes-Benz and his partner GAZ chose Siemens to be its maintenance partner at a new engine plant in Yaroslavl, Russia. The new plant offers a capacity to manufacture diesel engines for the Russian market, for locally produced Sprinter Classic. In addition to engines for the local market, the Yaroslavl plant will also produce spare parts. Mercedes-Benz Russia and his partner needed a service partner in order to ensure the operation of these lines in a maintenance partnership arrangement. The challenges included coordinating the entire maintenance management operation, in particular inspections, corrective and predictive maintenance activities, and the optimizing spare parts management. Siemens developed a customized maintenance solution that includes all electronic and mechanical maintenance activities (Integral Plant Maintenance).