San Pellegrino Group Keeps the Water Flowing Thanks to a Consumer Goods Solution from Intermec by Honeywell
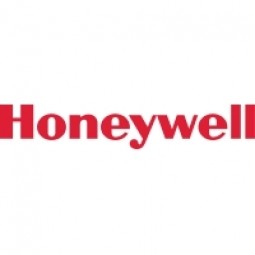
Customer Company Size
Large Corporate
Region
- Europe
Country
- Italy
Product
- Intermec by Honeywell SF51
Tech Stack
- Barcode Scanning
- Data Collection
Implementation Scale
- Enterprise-wide Deployment
Impact Metrics
- Productivity Improvements
- Customer Satisfaction
- Digital Expertise
Technology Category
- Functional Applications - Inventory Management Systems
- Functional Applications - Remote Monitoring & Control Systems
Applicable Industries
- Consumer Goods
Applicable Functions
- Sales & Marketing
- Warehouse & Inventory Management
Use Cases
- Inventory Management
- Remote Asset Management
- Track & Trace of Assets
Services
- System Integration
- Training
About The Customer
The San Pellegrino Group is Italy’s leading producer and distributor of bottled water and drinks. The company promotes its products through a tailored sales network and supplies numerous bars and restaurants with cold drinks cabinets on a free loan basis. These cabinets are used to display and store San Pellegrino products, ensuring visibility and availability to end consumers. The company has a strong focus on maintaining the quality and consistency of its product displays to enhance customer experience and drive sales. With a significant presence in the Italian market, San Pellegrino aims to win over end consumers by offering the right type of drink at the right moment in various retail settings.
The Challenge
The San Pellegrino Group faced the challenge of ensuring the efficient replenishment of its external sales channels, which include bars, restaurants, and other refreshment outlets across Italy. The company needed a system to monitor and manage the stock in cold drinks cabinets provided on a free loan to these outlets. The primary issues were ensuring that the cabinets were used exclusively for San Pellegrino products, maintaining an ideal stock structure that matched the demand of different areas, and collecting accurate data for sales analysis. The traditional methods of dealing with wholesalers were no longer sufficient as the company shifted focus to winning over end consumers directly in various retail environments.
The Solution
To address these challenges, San Pellegrino implemented the Intermec by Honeywell SF51 scanner. This small, ergonomic, and lightweight scanner can be clipped to a belt, allowing area promoters to scan all necessary information quickly and efficiently during their monthly visits to sales outlets. The SF51 scanner enables promoters to check the status of the cold drinks cabinets, ensure they are stocked according to corporate guidelines, and record data for sales analysis. The scanner also provides proof of the promoter's visit by logging the scanned data. This innovative system not only helps in monitoring the usage of the cabinets but also ensures that the stock is well-structured and meets the typical demand of different areas. The SF51 scanner has been well received by the network for its practicality, ease of use, and ability to collect accurate data without input or transcription errors.
Operational Impact
Case Study missing?
Start adding your own!
Register with your work email and create a new case study profile for your business.
Related Case Studies.
.png)
Case Study
Improving Vending Machine Profitability with the Internet of Things (IoT)
The vending industry is undergoing a sea change, taking advantage of new technologies to go beyond just delivering snacks to creating a new retail location. Intelligent vending machines can be found in many public locations as well as company facilities, selling different types of goods and services, including even computer accessories, gold bars, tickets, and office supplies. With increasing sophistication, they may also provide time- and location-based data pertaining to sales, inventory, and customer preferences. But at the end of the day, vending machine operators know greater profitability is driven by higher sales and lower operating costs.
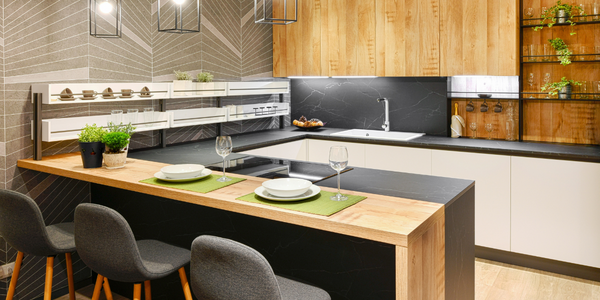
Case Study
Series Production with Lot-size-1 Flexibility
Nobilia manufactures customized fitted kitchens with a lot size of 1. They require maximum transparency of tracking design data and individual processing steps so that they can locate a particular piece of kitchen furniture in the sequence of processes.
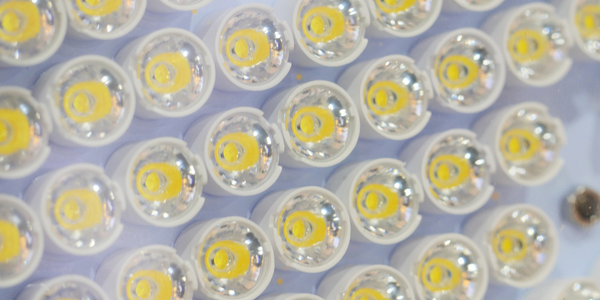
Case Study
American Eagle Achieves LEED with GE LED Lighting Fixtures
American Eagle Outfitters (AEO) was in the process of building a new distribution center. The AEO facility management team decided to look at alternate options for lighting layout that could provide energy and maintenance savings. AEO would need a full-time maintenance employee just to replace burned-out fluorescent tubes.
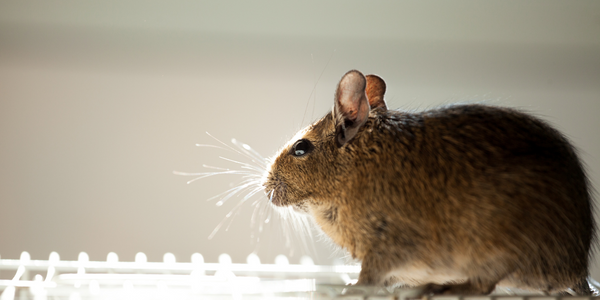
Case Study
Revolutionizing Rodent Control
From pet- and child-safe traps, to touch-free and live-catch rodent control solutions, Victor continues to stay committed to producing superior products that meet the varying needs of today’s pest control professionals. And, with a long standing history supporting customers in the food processing, service, and retail settings, Victor knew that strict regulations were costing organizations thousands of dollars in excess overhead trying to manage their rodent-control solutions. Trap inspections in these environments are often difficult and time consuming, requiring personnel to manually check a trap’s status multiple times per day, amounting to over six hours of manual labor. Victor is looking for an innovative way to increase operational efficiencies with the use of technology.