Customer Company Size
Large Corporate
Region
- Europe
Country
- Denmark
Product
- QlikView
- QlikView Server
- QlikView Publisher
Tech Stack
- IBM System i (AS/400)
- Generic Reporting System
Implementation Scale
- Enterprise-wide Deployment
Impact Metrics
- Productivity Improvements
- Customer Satisfaction
Technology Category
- Analytics & Modeling - Real Time Analytics
Applicable Industries
- Automotive
Applicable Functions
- Sales & Marketing
Use Cases
- Supply Chain Visibility
- Predictive Maintenance
Services
- System Integration
- Training
About The Customer
Scania Denmark A/S is a world leader in the sales and service of heavy trucks and buses. The company has a market share of about 30% in Denmark, which means there are over 16,000 vehicles that need servicing at regular intervals at the 31 service stations located around the country. The company's organization is widely spread and uses a number of different applications on different platforms, including generic reporting systems. It was important for Scania to quickly retrieve and compile all necessary information, and train its organization to use this information proactively.
The Challenge
Scania Denmark, a world leader in the sales and service of heavy trucks and buses, faced several challenges. The company needed to improve coordination between sales, finance, service, production, and shipping. The production team required visibility into product performance, usage, and service. The IT staff was under pressure from producing multiple reports on IBM System i (AS/400) information. Scania Denmark was using a number of different applications on different platforms, including generic reporting systems. It was crucial for Scania to quickly retrieve and compile all necessary information, and train its organization to use this information proactively.
The Solution
Scania Denmark deployed QlikView to 150 employees across 5 functional areas. With QlikView pulling data from various IBM System i (AS/400) applications, Scania Denmark analyzes information on sales, production, shipping, and product performance – all focused on improving the company’s financial performance and competitive positioning. With QlikView Server and Publisher, Scania Denmark employees work from a single version of the truth through a common dashboard. The exact data required can be extracted from an AS/400 system in a structured way. Fields can now be named in plain English when loading data. QlikView also highlights incorrect data in the database. Errors such as incorrectly registered vehicles, or vehicles registered more than once are seen instantly.
Operational Impact
Case Study missing?
Start adding your own!
Register with your work email and create a new case study profile for your business.
Related Case Studies.
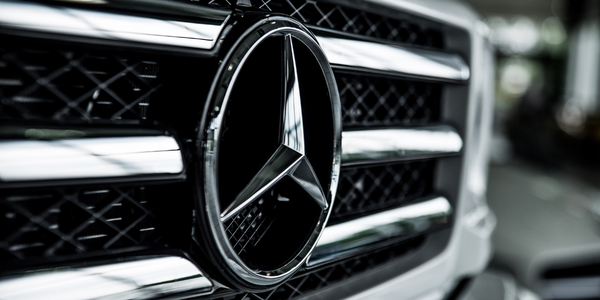
Case Study
Integral Plant Maintenance
Mercedes-Benz and his partner GAZ chose Siemens to be its maintenance partner at a new engine plant in Yaroslavl, Russia. The new plant offers a capacity to manufacture diesel engines for the Russian market, for locally produced Sprinter Classic. In addition to engines for the local market, the Yaroslavl plant will also produce spare parts. Mercedes-Benz Russia and his partner needed a service partner in order to ensure the operation of these lines in a maintenance partnership arrangement. The challenges included coordinating the entire maintenance management operation, in particular inspections, corrective and predictive maintenance activities, and the optimizing spare parts management. Siemens developed a customized maintenance solution that includes all electronic and mechanical maintenance activities (Integral Plant Maintenance).

Case Study
Monitoring of Pressure Pumps in Automotive Industry
A large German/American producer of auto parts uses high-pressure pumps to deburr machined parts as a part of its production and quality check process. They decided to monitor these pumps to make sure they work properly and that they can see any indications leading to a potential failure before it affects their process.