Technology Category
- Application Infrastructure & Middleware - Data Exchange & Integration
- Application Infrastructure & Middleware - Middleware, SDKs & Libraries
Applicable Functions
- Human Resources
- Warehouse & Inventory Management
Use Cases
- Inventory Management
- Picking, Sorting & Positioning
Services
- System Integration
About The Customer
SCARPA is a global manufacturer and distributor of high-quality footwear for various outdoor activities such as mountaineering, trekking, hiking, alpine running, climbing, and skiing. The company was founded in the Italian Alps and has seen significant growth over the years. As part of its growth strategy, SCARPA has been upgrading its technical infrastructure, including replacing its legacy, open-source web storefront with a more powerful and modern Magento platform. Despite its global reach, SCARPA operates with a small team and has been using NetSuite for nearly a decade to manage its operations.
The Challenge
SCARPA, a global manufacturer and distributor of performance-driven footwear, was facing significant challenges in managing its growing operations. The company had been using NetSuite for nearly a decade and had recently upgraded its web storefront to the Magento platform. However, the migration from its legacy storefront necessitated the automation of its order-to-cash processes by connecting Magento and NetSuite. The custom integration that was in place proved to be unreliable, often causing delays, errors, and a lack of inventory visibility. This situation was further exacerbated by the fact that the team had to prioritize human resources to deal with customer orders, causing other critical areas of the business to be neglected.
The Solution
To address these challenges, SCARPA decided to automate its processes with Celigo’s Magento-NetSuite Integration App. This solution was designed to reduce errors, increase efficiency, and improve the customer experience by providing a better way to integrate Magento and NetSuite. Celigo’s prebuilt integration flows allowed the SCARPA team to replace the previous custom integration quickly, a critical factor considering the small size of SCARPA’s operations team, which did not include an in-house developer. The integration with Celigo has significantly improved the company’s efficiency and customer response, freeing up the team to focus on larger, more strategic initiatives.
Operational Impact
Case Study missing?
Start adding your own!
Register with your work email and create a new case study profile for your business.
Related Case Studies.
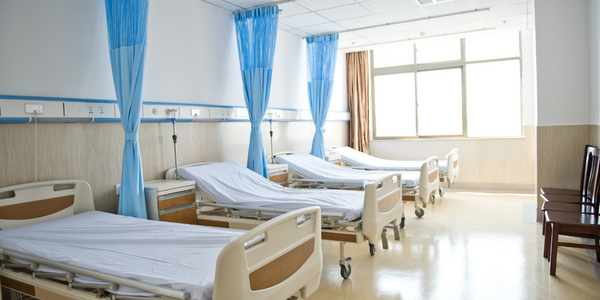
Case Study
Hospital Inventory Management
The hospital supply chain team is responsible for ensuring that the right medical supplies are readily available to clinicians when and where needed, and to do so in the most efficient manner possible. However, many of the systems and processes in use at the cancer center for supply chain management were not best suited to support these goals. Barcoding technology, a commonly used method for inventory management of medical supplies, is labor intensive, time consuming, does not provide real-time visibility into inventory levels and can be prone to error. Consequently, the lack of accurate and real-time visibility into inventory levels across multiple supply rooms in multiple hospital facilities creates additional inefficiency in the system causing over-ordering, hoarding, and wasted supplies. Other sources of waste and cost were also identified as candidates for improvement. Existing systems and processes did not provide adequate security for high-cost inventory within the hospital, which was another driver of cost. A lack of visibility into expiration dates for supplies resulted in supplies being wasted due to past expiry dates. Storage of supplies was also a key consideration given the location of the cancer center’s facilities in a dense urban setting, where space is always at a premium. In order to address the challenges outlined above, the hospital sought a solution that would provide real-time inventory information with high levels of accuracy, reduce the level of manual effort required and enable data driven decision making to ensure that the right supplies were readily available to clinicians in the right location at the right time.

Case Study
DHL Supply Chain Growing Use of AR Glasses
A picker with an RF scanner is constantly looking at the gun to get pick commands, hitting the confirm button and doing things in sequential fashion which is time consuming. Warehouse operations costs add up to 20% of the total logistics costs for DHL.
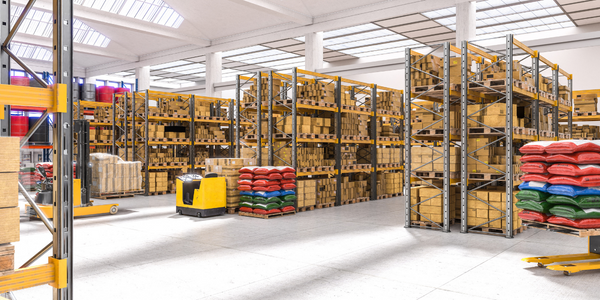
Case Study
Hardware Retailer Uses Data Warehouse to Track Inventory
Ace tracked which products retailers ordered, when they were ordered and shipped. However, the company could not track or forecast actual sales. Data used for reporting was up to a one-week old, owing to performance and data cleansing issues. Requirement to integrate wholesale and inventory data with POS data to help drive key business decisions, improve category management, lower inventory costs and optimize pricing. Reliance on custom coding to integrate POS data was excessively resource intensive and led to major performance constraints.
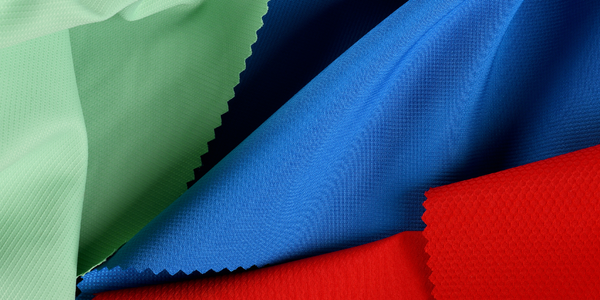
Case Study
Remake Enterprise-to-production System
The client was running a legacy material flow tracking system and wanted to replace the system with a more effective one as the system was increasingly expensive to maintain and support and also was not extendable. The client's IT landscape was filled with modern applications and it was difficult to interface the material flow tracking system with modern applications.