Technology Category
- Sensors - Lidar & Lazer Scanners
Applicable Industries
- Aerospace
- Automotive
Applicable Functions
- Maintenance
- Quality Assurance
Use Cases
- Additive Manufacturing
- Experimentation Automation
Services
- Testing & Certification
About The Customer
Sintavia is a global leader in independent metal additive manufacturing, supporting critical industries such as Aerospace & Defense, Oil & Natural Gas, Automotive, and Ground Power Generation. The company is committed to parameter optimization and quality serial production of metal parts that meet or exceed the exacting standards of these industries. Sintavia possesses unique in-house capabilities, including six high-speed printers from four of the largest global OEMs, a hot isostatic press, a vacuum heat treatment furnace, an industrial CT scanner, a wire EDM, a full complement of mechanical testing equipment, a full metallurgical laboratory, and a micro powder lab. This allows Sintavia to optimize parameters, serially manufacture, and audit quality much faster than any of its competitors.
The Challenge
Sintavia, a global leader in independent metal additive manufacturing, faced the challenge of proving the ability to additively manufacture optimized aerospace replacement parts. The goal was to exceed the existing part’s mechanical and operational properties while decreasing the overall weight. The company aimed to produce optimized designs of aerospace brackets that meet or exceed the existing bracket’s mechanical properties while reducing the overall weight of the parts. The component selected for this challenge was an aftermarket aviation part for a low pressure turbine, used 12 times on each engine.
The Solution
To address the challenge, Sintavia utilized a combination of concept generation with solidThinking Inspire and manufacturing with SLM 280 machine. The process began with capturing the geometry of the original part using a blue light scanner, followed by creating a high-fidelity CAD model to the exact specs of the original geometry. The team then determined all of the loading conditions that the part would incur during its usage and applied these to the model. Multiple optimization iterations were run on the part, including multiple rounds with modified design spaces, testing of different compression, factory of safety, etc. Finite element analysis (FEA) was then run on the results to compare and determine the best optimization iteration to move forward with. Once a final Inspire optimization result was selected, the team used the PolyNURBS tools inside of solidThinking Evolve to refine the optimization into its final geometry. The final optimized geometry was created using Sintavia's SLM Systems’ 280 twin laser machine, coupled with Inconel 718 powder.
Operational Impact
Quantitative Benefit
Case Study missing?
Start adding your own!
Register with your work email and create a new case study profile for your business.
Related Case Studies.
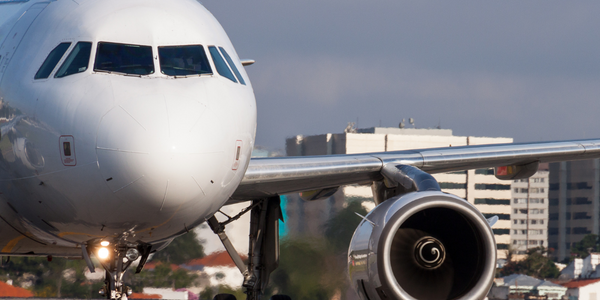
Case Study
Airbus Soars with Wearable Technology
Building an Airbus aircraft involves complex manufacturing processes consisting of thousands of moving parts. Speed and accuracy are critical to business and competitive advantage. Improvements in both would have high impact on Airbus’ bottom line. Airbus wanted to help operators reduce the complexity of assembling cabin seats and decrease the time required to complete this task.
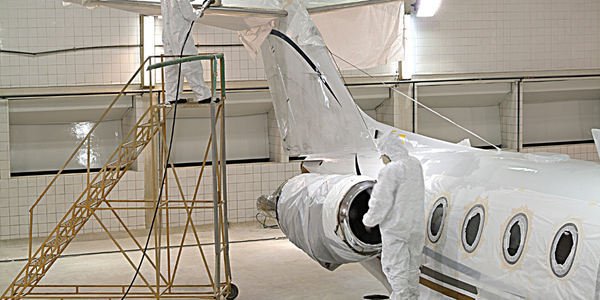
Case Study
Aircraft Predictive Maintenance and Workflow Optimization
First, aircraft manufacturer have trouble monitoring the health of aircraft systems with health prognostics and deliver predictive maintenance insights. Second, aircraft manufacturer wants a solution that can provide an in-context advisory and align job assignments to match technician experience and expertise.
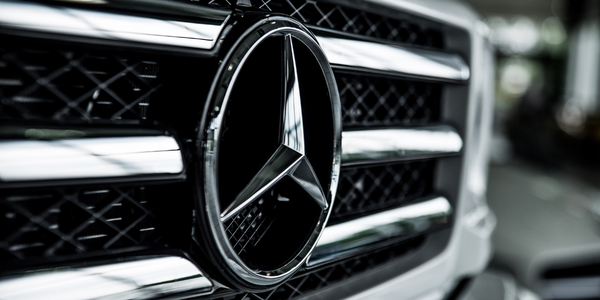
Case Study
Integral Plant Maintenance
Mercedes-Benz and his partner GAZ chose Siemens to be its maintenance partner at a new engine plant in Yaroslavl, Russia. The new plant offers a capacity to manufacture diesel engines for the Russian market, for locally produced Sprinter Classic. In addition to engines for the local market, the Yaroslavl plant will also produce spare parts. Mercedes-Benz Russia and his partner needed a service partner in order to ensure the operation of these lines in a maintenance partnership arrangement. The challenges included coordinating the entire maintenance management operation, in particular inspections, corrective and predictive maintenance activities, and the optimizing spare parts management. Siemens developed a customized maintenance solution that includes all electronic and mechanical maintenance activities (Integral Plant Maintenance).
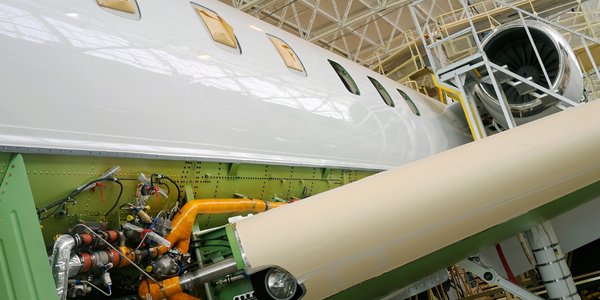
Case Study
Aerospace & Defense Case Study Airbus
For the development of its new wide-body aircraft, Airbus needed to ensure quality and consistency across all internal and external stakeholders. Airbus had many challenges including a very aggressive development schedule and the need to ramp up production quickly to satisfy their delivery commitments. The lack of communication extended design time and introduced errors that drove up costs.