Technology Category
- Application Infrastructure & Middleware - Event-Driven Application
Applicable Industries
- Aerospace
- Healthcare & Hospitals
Use Cases
- Time Sensitive Networking
- Warehouse Automation
Services
- Cloud Planning, Design & Implementation Services
About The Customer
LifeFlight is an Australian aero-medical retrieval service and charity, established in 1986. Its mission is to save lives, speed recovery, and serve the community by providing the highest standard of rapidly deploying critical care. LifeFlight flies medical teams throughout the country to provide quicker medical treatment. It also transports patients to appropriate hospitals for care and upskills area first responders to better equip them to manage complex medical emergencies. As LifeFlight's flight missions increased each year, it needed a solution that could integrate with their existing systems and accelerate processes.
The Challenge
LifeFlight, an Australian aero-medical retrieval service and charity, faced a significant challenge as their flight missions increased annually. The organization had many necessary processes in place to save lives, but there was room for improvement, particularly in technology. Different departments within LifeFlight began seeking their own ways to enhance efficiency, including purchasing individual software. This led to a situation where siloed systems blocked visibility, and a lack of integration slowed down processes. The need for an organization-wide change was evident, as a few lost seconds could mean the difference between life and death in their line of work.
The Solution
LifeFlight decided to invest in Nintex K2 Cloud to better manage the many moving parts within the organization's various departments and divisions. The focus was on LifeFlight's emergency response center, where a demo of K2 Cloud was shown to the manager to gain buy-in. The solution was a new unified aircraft tasking application that automated manual, repetitive tasks that had previously been consuming valuable time and attention. This application was designed to integrate with existing systems, streamline processes, and make real-time information accessible and visible to all departments, thereby creating efficiency across the organization.
Operational Impact
Quantitative Benefit
Case Study missing?
Start adding your own!
Register with your work email and create a new case study profile for your business.
Related Case Studies.
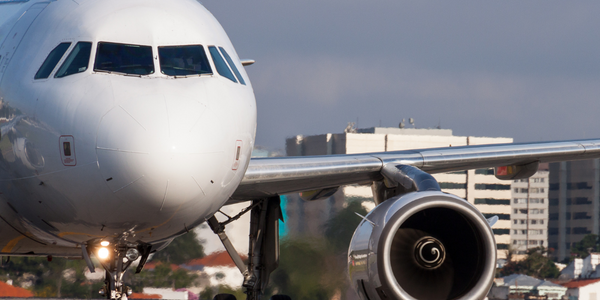
Case Study
Airbus Soars with Wearable Technology
Building an Airbus aircraft involves complex manufacturing processes consisting of thousands of moving parts. Speed and accuracy are critical to business and competitive advantage. Improvements in both would have high impact on Airbus’ bottom line. Airbus wanted to help operators reduce the complexity of assembling cabin seats and decrease the time required to complete this task.
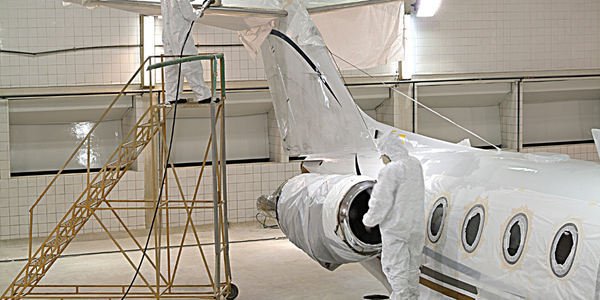
Case Study
Aircraft Predictive Maintenance and Workflow Optimization
First, aircraft manufacturer have trouble monitoring the health of aircraft systems with health prognostics and deliver predictive maintenance insights. Second, aircraft manufacturer wants a solution that can provide an in-context advisory and align job assignments to match technician experience and expertise.
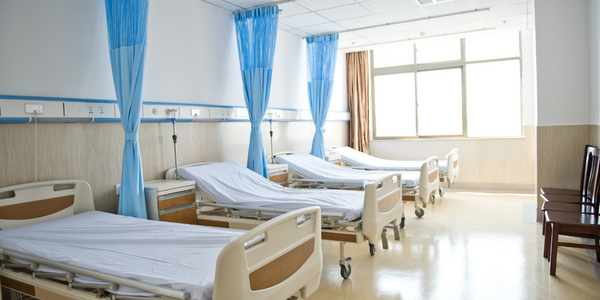
Case Study
Hospital Inventory Management
The hospital supply chain team is responsible for ensuring that the right medical supplies are readily available to clinicians when and where needed, and to do so in the most efficient manner possible. However, many of the systems and processes in use at the cancer center for supply chain management were not best suited to support these goals. Barcoding technology, a commonly used method for inventory management of medical supplies, is labor intensive, time consuming, does not provide real-time visibility into inventory levels and can be prone to error. Consequently, the lack of accurate and real-time visibility into inventory levels across multiple supply rooms in multiple hospital facilities creates additional inefficiency in the system causing over-ordering, hoarding, and wasted supplies. Other sources of waste and cost were also identified as candidates for improvement. Existing systems and processes did not provide adequate security for high-cost inventory within the hospital, which was another driver of cost. A lack of visibility into expiration dates for supplies resulted in supplies being wasted due to past expiry dates. Storage of supplies was also a key consideration given the location of the cancer center’s facilities in a dense urban setting, where space is always at a premium. In order to address the challenges outlined above, the hospital sought a solution that would provide real-time inventory information with high levels of accuracy, reduce the level of manual effort required and enable data driven decision making to ensure that the right supplies were readily available to clinicians in the right location at the right time.
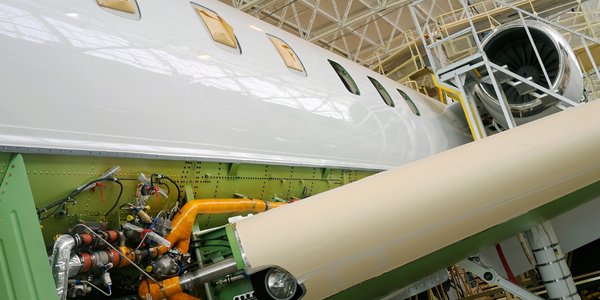
Case Study
Aerospace & Defense Case Study Airbus
For the development of its new wide-body aircraft, Airbus needed to ensure quality and consistency across all internal and external stakeholders. Airbus had many challenges including a very aggressive development schedule and the need to ramp up production quickly to satisfy their delivery commitments. The lack of communication extended design time and introduced errors that drove up costs.
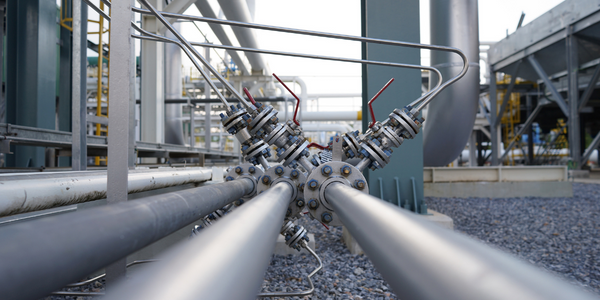
Case Study
Gas Pipeline Monitoring System for Hospitals
This system integrator focuses on providing centralized gas pipeline monitoring systems for hospitals. The service they provide makes it possible for hospitals to reduce both maintenance and labor costs. Since hospitals may not have an existing network suitable for this type of system, GPRS communication provides an easy and ready-to-use solution for remote, distributed monitoring systems System Requirements - GPRS communication - Seamless connection with SCADA software - Simple, front-end control capability - Expandable I/O channels - Combine AI, DI, and DO channels