Technology Category
- Functional Applications - Computerized Maintenance Management Systems (CMMS)
- Functional Applications - Inventory Management Systems
Applicable Industries
- Life Sciences
Applicable Functions
- Maintenance
- Procurement
Use Cases
- Service Parts Management
- Time Sensitive Networking
Services
- System Integration
About The Customer
Cerapedics is a global ortho-biologics company that is revolutionizing bone repair with its bone-graft technology. The company's products are used in more than 4 million annual orthopedics, trauma, spine, and interventional procedures around the world. The company faced a challenge in managing its inventory of over 750 spare parts, which was time-consuming and labor-intensive. John Espinosa, the Maintenance Manager at Cerapedics, recognized the need for a more efficient system and worked with eMaint to implement their industry-leading CMMS software.
The Challenge
Cerapedics, a global bone-graft technology company, was facing a significant challenge in managing their inventory of over 750 spare parts. The company needed a system that would allow for efficient and strategic spare parts management. The existing system was time-consuming and labor-intensive, with workers spending valuable time navigating the inventory to find the right part for the right equipment. The company recognized the need for part tagging, location tracking, and a central organizing system for the storeroom. The challenge was to develop a system that would not only streamline the process but also ensure that critical spares were readily available during maintenance emergencies.
The Solution
John Espinosa, the Maintenance Manager at Cerapedics, worked with eMaint to implement their industry-leading Computerized Maintenance Management System (CMMS) software. The eMaint CMMS allowed for the organization and tracking of Cerapedics’ spare parts, establishing a streamlined and standardized system that saved the team time and labor. The system made finding critical spares during maintenance crises a simple process of searching the eMaint spare parts database. The solution also integrated with Cerapedics’ purchasing system, allowing for easy creation of purchase orders and fulfillment of invoices. The eMaint Parts Reorder list provided visibility into parts that were running low, enabling proactive management of the inventory.
Operational Impact
Quantitative Benefit
Case Study missing?
Start adding your own!
Register with your work email and create a new case study profile for your business.
Related Case Studies.
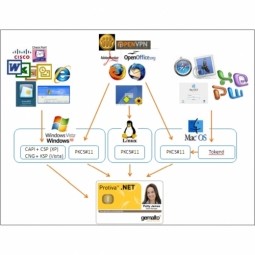
Case Study
Corporate Identity Solution Adds Convenience to Beckman Coulter
Beckman Coulter wanted to implement a single factor solution for physical and remote logical access to corporate network. Bechman Coulter's users were carrying smart card badges for doors, but also needed a one-time password token to access to our corporate network when they were not in the office. They wanted to simplify the process.
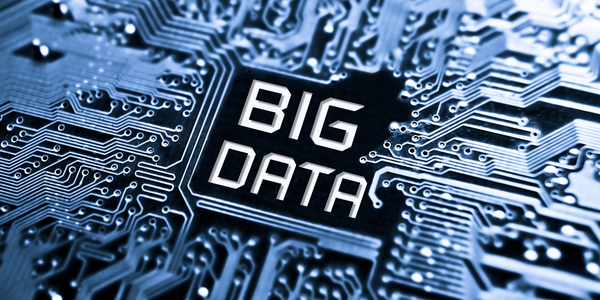
Case Study
Embracing Business Success in Real Time
· Increase control over growing Big Data to improve business decisions · Manage data for 28,000 biotechnology stockkeeping units in the fields of microbiology, molecular biology, animal cell cultures, plant tissue cultures, and lab ware for laboratory chemicals · Accelerate report generation and analysis with real-time data
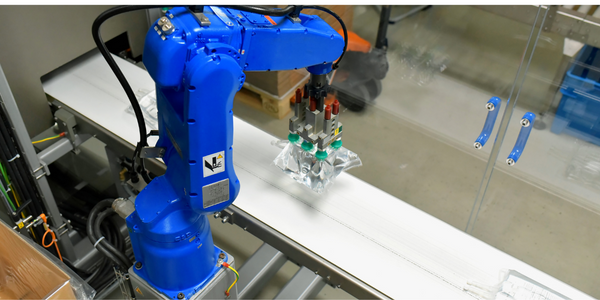
Case Study
Flow Robotics: Scaling Up Production and Accelerating Product Development with IoT
Flow Robotics, a Danish manufacturer, developed flowbot™ ONE pipetting robots to alleviate the strain on bioanalysts in life-science laboratories and hospitals across Europe. These robots were designed to automate part of the testing process, speeding up the time it takes to produce results and reducing pressure on staff. However, the company faced challenges in scaling up production and accelerating product development. High workloads and physically challenging conditions have long been an issue for laboratory professionals. Flow Robotics estimates that around half of medical lab technicians carry out the same arm movements for at least a quarter of their working day. The American Society for Clinical Pathology reported that 85% of laboratory professionals feel burnt out; 36% struggle with inadequate staffing; and 32% face a heavy workload and pressure to complete all testing on time.
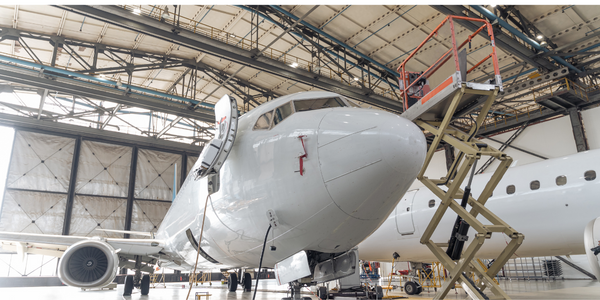
Case Study
Revolutionizing Aerospace Industry with 3D Printing: A 63% Lighter Titanium Part
GE Aviation, a renowned name in the aerospace industry, recognized the potential of 3D printing technology in transforming the sector. The primary challenge was to reduce the weight of the aerospace parts, which would directly impact the fuel costs. A lighter airplane would mean lower fuel consumption, leading to cost savings and a smaller carbon footprint. However, achieving this weight reduction without compromising the strength and functionality of the parts was a significant challenge. Traditional manufacturing methods were not able to provide the desired weight reduction while maintaining the required stiffness and strength of the parts. The challenge was to find a solution that could create strong, light, and functional aerospace parts.
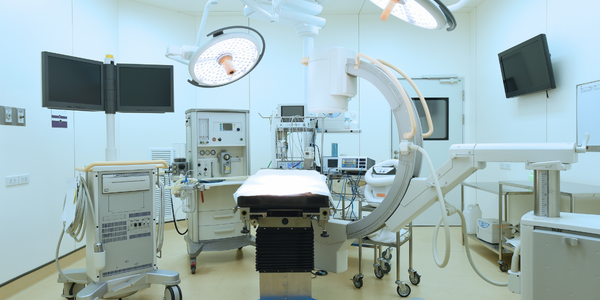
Case Study
Material Intelligence at Ethicon: Sustaining Medical Device Manufacturability and Improving Patient Care
Ethicon, a world-class medical devices company, faced several challenges in its operations. The rapid selection of manufacturing materials compliant in global markets was critical to assure patients, practitioners, and purchasing organizations of the biocompatibility of their medical devices. Ensuring supply chain continuity and minimizing risks of obsolescence for medical devices due to regulatory changes were also crucial in meeting Ethicon’s ongoing commitment to maintaining patient care. Furthermore, the engineers at Ethicon were developing the next generation of medical devices and needed to access historical material data to accelerate new product development. The process of centralizing and digitalizing its materials information was a significant challenge that Ethicon needed to overcome.
Case Study
IWT's Transformation: Customizing with Efficiency in IoT
IWT, a company specializing in the design, manufacture, and installation of washing systems for the life sciences and pharmaceutical industries, faced a significant challenge in managing its wide product portfolio. The company manufactures 45 different models, 60% of which are customized to some degree. This high level of customization, combined with limited production quantities, necessitated a controlled process for managing the release of engineering changes. The goal was to achieve efficiency, reduce process time, and better coordinate production throughout the organization. The need for strict compliance in heavily regulated industries further complicated the situation. IWT's existing PLM journey with Dassault Systèmes’ SOLIDWORKS for 3D CAD and Enovia for managing CAD data and Bills of Materials (BOMs) was proving inadequate. The system had limited part classification, no workflow, and no tool to ensure data consistency. The management of non-CAD documents was also a challenge, with information often difficult to find and access.