Technology Category
- Infrastructure as a Service (IaaS) - Hybrid Cloud
- Infrastructure as a Service (IaaS) - Private Cloud
Applicable Industries
- Automotive
- Cement
Applicable Functions
- Quality Assurance
Use Cases
- Manufacturing Process Simulation
- Transportation Simulation
Services
- Cloud Planning, Design & Implementation Services
About The Customer
Subaru is a global manufacturer of automobiles and aircraft, with a strong focus on safety and human-oriented manufacturing. The company's roots are in aviation, but its automotive division has evolved to become its core business. Subaru is committed to delivering value to its customers by continually improving and refining its designs. The company's goal is to achieve zero fatal traffic accidents by 2030. Over the past decade, Subaru has already halved the number of fatal and serious injuries per million vehicles sold. To further this initiative, Subaru must continue to innovate and ensure high collision safety, which requires conducting CAE simulations using high-performance computing (HPC).
The Challenge
Subaru, a global automobile and aircraft manufacturer, is committed to achieving zero fatal traffic accidents by 2030. To reach this goal, the company needs to continually innovate and ensure high collision safety, which requires conducting Computer-Aided Engineering (CAE) simulations using High-Performance Computing (HPC). Subaru had been maintaining its own HPC environment near its main manufacturing facility in Japan’s Gunma prefecture. However, as the computational processing requirements for simulation increased, the team faced a shortage of power and space for expansion. They started using a private cloud located in a remote data center in Tokyo, which required a dedicated line for user access. Due to the high cost, they decided to evaluate public cloud options and sought recommendations from the Japan Automobile Manufacturers Association’s cloud working group.
The Solution
After evaluating various factors such as cost, performance, security, ease of use, and expert support, Subaru chose Oracle Cloud Infrastructure (OCI) with workload management by Altair® PBS Professional®, a solution they were already familiar with and trusted. PBS Professional comes with a built-in GUI that allows users to extend their HPC resources and utilize dynamic cloud bursting for peak-time workloads. Subaru confirmed that calculation processing wouldn’t be compromised by a move to the cloud, and they optimized their new environment to ensure efficient performance. The migration of its collision and fluid simulation environment to OCI was a large-scale operation completed in around six weeks, significantly shorter than the 3-4 months it would typically take to expand an on-premises HPC environment. The team also reduced the amount of data transfer required by setting up remote preprocessing.
Operational Impact
Quantitative Benefit
Case Study missing?
Start adding your own!
Register with your work email and create a new case study profile for your business.
Related Case Studies.
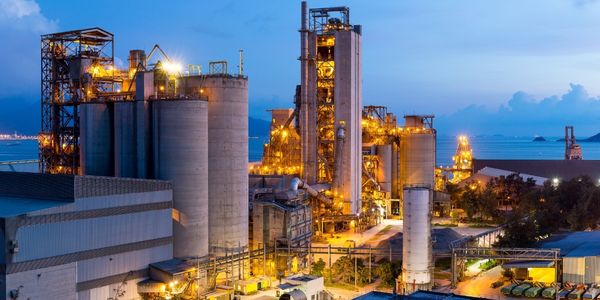
Case Study
System 800xA at Indian Cement Plants
Chettinad Cement recognized that further efficiencies could be achieved in its cement manufacturing process. It looked to investing in comprehensive operational and control technologies to manage and derive productivity and energy efficiency gains from the assets on Line 2, their second plant in India.
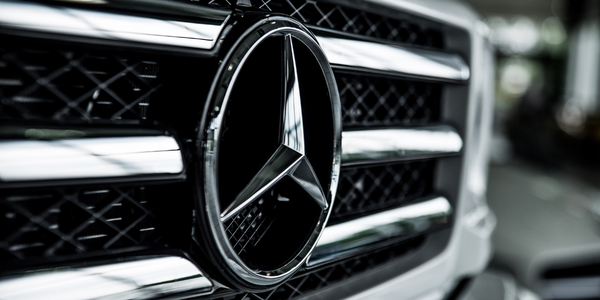
Case Study
Integral Plant Maintenance
Mercedes-Benz and his partner GAZ chose Siemens to be its maintenance partner at a new engine plant in Yaroslavl, Russia. The new plant offers a capacity to manufacture diesel engines for the Russian market, for locally produced Sprinter Classic. In addition to engines for the local market, the Yaroslavl plant will also produce spare parts. Mercedes-Benz Russia and his partner needed a service partner in order to ensure the operation of these lines in a maintenance partnership arrangement. The challenges included coordinating the entire maintenance management operation, in particular inspections, corrective and predictive maintenance activities, and the optimizing spare parts management. Siemens developed a customized maintenance solution that includes all electronic and mechanical maintenance activities (Integral Plant Maintenance).

Case Study
Monitoring of Pressure Pumps in Automotive Industry
A large German/American producer of auto parts uses high-pressure pumps to deburr machined parts as a part of its production and quality check process. They decided to monitor these pumps to make sure they work properly and that they can see any indications leading to a potential failure before it affects their process.