Technology Category
- Networks & Connectivity - Gateways
- Platform as a Service (PaaS) - Application Development Platforms
Applicable Industries
- Automotive
- Cement
Applicable Functions
- Maintenance
Use Cases
- Onsite Human Safety Management
- Vehicle Telematics
Services
- Cloud Planning, Design & Implementation Services
- System Integration
About The Customer
Summit Materials is a leading integrated construction materials solution provider with a vision to be the most socially-responsible company in the market. The company operates across 22 U.S. states and British Columbia, Canada, with 400 sites, 4,000 vehicles, and 12 operating companies. Summit Materials is committed to achieving net-zero emissions by 2050 and has an ongoing ESG initiative aimed at a 75% reduction in emissions across their business. They place a large focus on monitoring fuel usage and idling across their fleet to improve miles per gallon.
The Challenge
Summit Materials, a leading integrated construction materials solution provider, faced challenges in achieving their Environmental, Social, and Governance (ESG) goals due to decentralized solutions for telematics, safety, and site visibility. This decentralization led to gaps in their data and reporting, hindering their progress towards their ambitious safety and sustainability goals. The company's vast operations, spanning 22 U.S. states and British Columbia, Canada, made it difficult to track progress against their goals. They needed a technology partner that could consolidate their over-the-road fleet safety, emissions, and fuel consumption data into a single platform, improving visibility across their distributed operations.
The Solution
Summit Materials partnered with Samsara to leverage their Connected Operations Cloud. This allowed Summit to consolidate their technology providers, improve data accuracy, and decrease preventable accidents. They implemented Samsara AI Dash Cams, which led to a significant increase in driver engagement and safety. The company was able to quickly retrieve incident footage, train drivers on safe driving practices, and reward drivers with the best Safety Scores across regions. Summit also used Samsara Vehicle Gateways to accurately record emissions figures and set meaningful targets, saving significant costs in fuel. They further consolidated their operational data via integrations using the Samsara open API. Additionally, Summit used Samsara Site Cameras and Site Gateways to extend outdoor visibility, helping to keep workers safe in the field.
Operational Impact
Quantitative Benefit
Case Study missing?
Start adding your own!
Register with your work email and create a new case study profile for your business.
Related Case Studies.
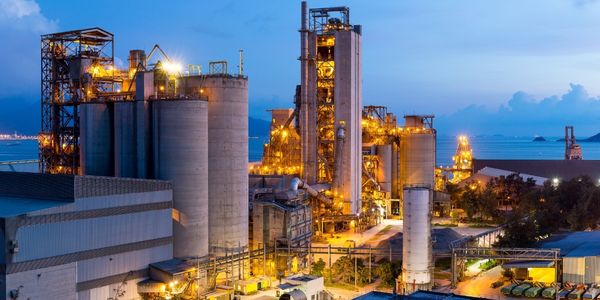
Case Study
System 800xA at Indian Cement Plants
Chettinad Cement recognized that further efficiencies could be achieved in its cement manufacturing process. It looked to investing in comprehensive operational and control technologies to manage and derive productivity and energy efficiency gains from the assets on Line 2, their second plant in India.
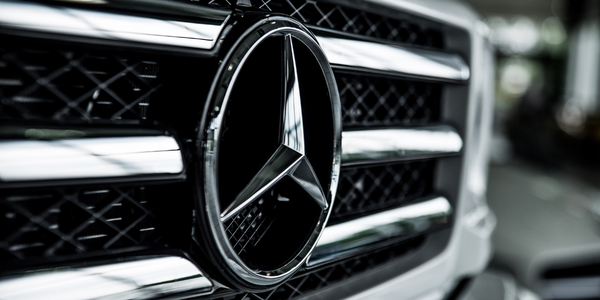
Case Study
Integral Plant Maintenance
Mercedes-Benz and his partner GAZ chose Siemens to be its maintenance partner at a new engine plant in Yaroslavl, Russia. The new plant offers a capacity to manufacture diesel engines for the Russian market, for locally produced Sprinter Classic. In addition to engines for the local market, the Yaroslavl plant will also produce spare parts. Mercedes-Benz Russia and his partner needed a service partner in order to ensure the operation of these lines in a maintenance partnership arrangement. The challenges included coordinating the entire maintenance management operation, in particular inspections, corrective and predictive maintenance activities, and the optimizing spare parts management. Siemens developed a customized maintenance solution that includes all electronic and mechanical maintenance activities (Integral Plant Maintenance).

Case Study
Monitoring of Pressure Pumps in Automotive Industry
A large German/American producer of auto parts uses high-pressure pumps to deburr machined parts as a part of its production and quality check process. They decided to monitor these pumps to make sure they work properly and that they can see any indications leading to a potential failure before it affects their process.