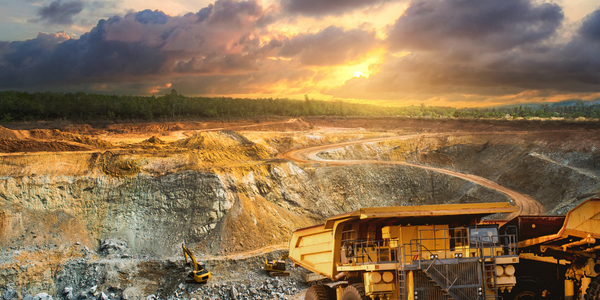
Technology Category
- Sensors - Environmental Sensors
Applicable Industries
- Oil & Gas
- Retail
Applicable Functions
- Product Research & Development
Use Cases
- Inventory Management
- Perimeter Security & Access Control
Services
- System Integration
The Customer
Suncor
About The Customer
Suncor is one of Canada’s largest integrated energy companies, specializing in the extraction of oil sand and its subsequent upgrading and refining into high-quality oil products. Headquartered in Calgary, Alberta, Suncor markets finished products to industrial and commercial customers, along with retail customers through their network of more than 1,500 Petro-Canada gas stations. Suncor’s Fort Hills mine is an open-pit truck and shovel mine that was commissioned in 2018 and capable of extracting 154,000 tons of oil sands per hour, producing 194,000 barrels of bitumen per day.
The Challenge
Suncor, one of Canada’s largest integrated energy companies, faced a significant challenge at their Fort Hills mine. Upon completion of commissioning in 2018, the control room operators were dealing with alarm loads 30 times higher than those recommended by alarm management standards and best practices. These alarm loads, combined with frequent alarm floods caused by plant upsets, resulted in significant operator overload. This increased the risk of safety, environmental, and production-related incidents at the site. The alarm system was overactive, causing a high level of stress and potential for error among the operators. The challenge was to reduce the alarm load to manageable levels and ensure the safety and efficiency of the operations.
The Solution
To address the alarm overload, Suncor initiated an alarm system improvement initiative. They elected to follow a process in-line with standards, specifically ANSI/ISA-18.2-2016, Management of Alarm Systems for the Process Industries. The first stage of this process was to develop an Alarm Philosophy that documented the intended approach to alarm management for the Fort Hills site. The process of identifying alarms as immediate candidates for rationalization, along with the actual rationalization, detailed design, and implementation of alarm changes was enabled by a combination of formalized processes and supporting software tools - in this case, the Honeywell Forge Alarm Management suite. A multi-disciplinary team was formed, and daily meetings were held to identify the top five most frequently occurring alarms. As alarm system performance improved, meetings were reduced from daily, to twice weekly, and eventually to weekly. The use of the Honeywell Forge Alarm Management suite of products was central to this process, enabling the rapid identification, investigation, and subsequent rationalization and implementation of changes to reduce bad actors, alarm floods, stale alarms, and shelved alarms.
Operational Impact
Quantitative Benefit
Case Study missing?
Start adding your own!
Register with your work email and create a new case study profile for your business.
Related Case Studies.
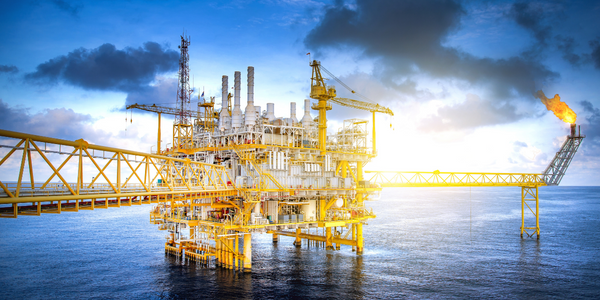
Case Study
Taking Oil and Gas Exploration to the Next Level
DownUnder GeoSolutions (DUG) wanted to increase computing performance by 5 to 10 times to improve seismic processing. The solution must build on current architecture software investments without sacrificing existing software and scale computing without scaling IT infrastructure costs.
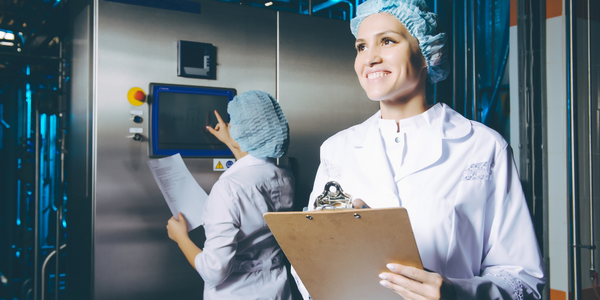
Case Study
Remote Wellhead Monitoring
Each wellhead was equipped with various sensors and meters that needed to be monitored and controlled from a central HMI, often miles away from the assets in the field. Redundant solar and wind generators were installed at each wellhead to support the electrical needs of the pumpstations, temperature meters, cameras, and cellular modules. In addition to asset management and remote control capabilities, data logging for remote surveillance and alarm notifications was a key demand from the customer. Terra Ferma’s solution needed to be power efficient, reliable, and capable of supporting high-bandwidth data-feeds. They needed a multi-link cellular connection to a central server that sustained reliable and redundant monitoring and control of flow meters, temperature sensors, power supply, and event-logging; including video and image files. This open-standard network needed to interface with the existing SCADA and proprietary network management software.
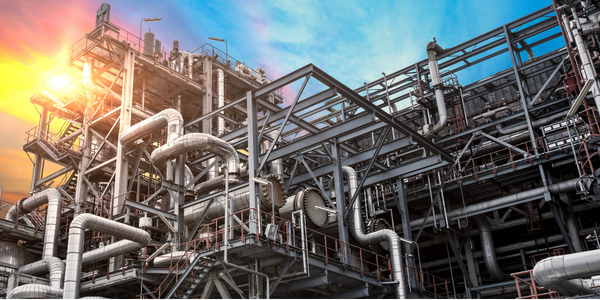
Case Study
Refinery Saves Over $700,000 with Smart Wireless
One of the largest petroleum refineries in the world is equipped to refine various types of crude oil and manufacture various grades of fuel from motor gasoline to Aviation Turbine Fuel. Due to wear and tear, eight hydrogen valves in each refinery were leaking, and each cost $1800 per ton of hydrogen vented. The plant also had leakage on nearly 30 flare control hydrocarbon valves. The refinery wanted a continuous, online monitoring system that could catch leaks early, minimize hydrogen and hydrocarbon production losses, and improve safety for maintenance.