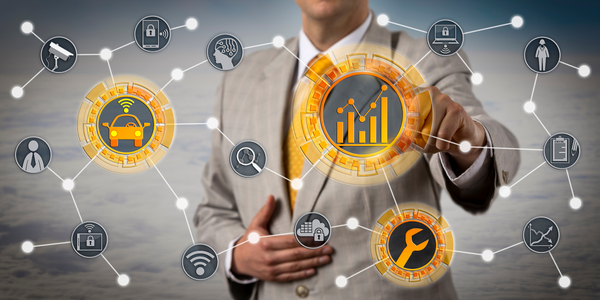
Technology Category
- Functional Applications - Computerized Maintenance Management Systems (CMMS)
- Networks & Connectivity - Cellular
Applicable Industries
- Equipment & Machinery
- Mining
Applicable Functions
- Maintenance
- Product Research & Development
Use Cases
- Driver Performance Monitoring
- Usage-Based Insurance
Services
- Hardware Design & Engineering Services
- System Integration
The Customer
Terex Corporation
About The Customer
Terex Corporation is a global manufacturer of lifting and material processing products and services. They deliver lifecycle solutions that maximize customer return on investment. Major Terex brands include Terex, Genie, Powerscreen, and Demag. Terex solutions serve a broad range of industries, including construction, infrastructure, manufacturing, shipping, transportation, refining, energy, utilities, quarrying, and mining. Terex offers financial products and services to assist in the acquisition of Terex equipment through Terex Financial Services. Powerscreen and Terex Finlay, brands of the Terex Corporation, are world leaders in the design, production, and supply of mobile, heavy-duty crushing and screening equipment for use in mining, quarrying, construction, demolition, and recycling.
The Challenge
Terex Corporation, a global manufacturer of lifting and material processing products, identified a unique opportunity to differentiate their product and enhance customer experience by integrating telematics technology into their crushing and screening equipment. These machines, which are highly specialized and valued in the hundreds of thousands of dollars, operate in harsh and often remote environments. The setup and tuning requirements for these machines vary from site to site, as no two ores or rocks are identical. Failure to properly tune these machines can result in the final processed material not meeting the desired specification. The cost, complexity, and remote nature of crushing and screening operations made a compelling case for the introduction of telematics. Terex aimed to provide the market with innovative features and add more value to their product.
The Solution
Terex partnered with ORBCOMM, a global leader in IoT solutions, for an intensive 18-month project to develop a customized end-to-end telematics solution. The solution included a cloud platform for data analytics and reporting, robust tracking and monitoring hardware, and 24/7 global connectivity over cellular and satellite networks. Users now have instant access to comprehensive global data on equipment location, start and stop times, fuel consumption, tonnages, cone settings, wear rates, operating hours, maintenance, service status, and more. The system generates pre-set alarms, alerts, and error messages, enabling prompt response to production and machine issues. Users are also notified automatically when their machines are operated outside of set hours and location. Since the initial deployment, ORBCOMM has added highly specialized features, such as sensors that measure wear and tear on critical parts and accurately predict when they are due for replacement.
Operational Impact
Quantitative Benefit
Case Study missing?
Start adding your own!
Register with your work email and create a new case study profile for your business.
Related Case Studies.
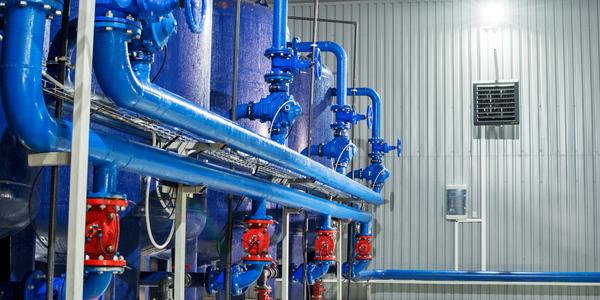
Case Study
Smart Water Filtration Systems
Before working with Ayla Networks, Ozner was already using cloud connectivity to identify and solve water-filtration system malfunctions as well as to monitor filter cartridges for replacements.But, in June 2015, Ozner executives talked with Ayla about how the company might further improve its water systems with IoT technology. They liked what they heard from Ayla, but the executives needed to be sure that Ayla’s Agile IoT Platform provided the security and reliability Ozner required.
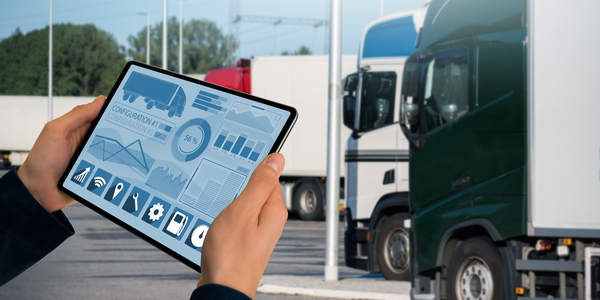
Case Study
IoT enabled Fleet Management with MindSphere
In view of growing competition, Gämmerler had a strong need to remain competitive via process optimization, reliability and gentle handling of printed products, even at highest press speeds. In addition, a digitalization initiative also included developing a key differentiation via data-driven services offers.
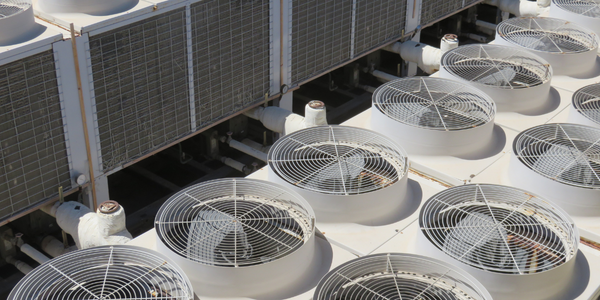
Case Study
Predictive Maintenance for Industrial Chillers
For global leaders in the industrial chiller manufacturing, reliability of the entire production process is of the utmost importance. Chillers are refrigeration systems that produce ice water to provide cooling for a process or industrial application. One of those leaders sought a way to respond to asset performance issues, even before they occur. The intelligence to guarantee maximum reliability of cooling devices is embedded (pre-alarming). A pre-alarming phase means that the cooling device still works, but symptoms may appear, telling manufacturers that a failure is likely to occur in the near future. Chillers who are not internet connected at that moment, provide little insight in this pre-alarming phase.
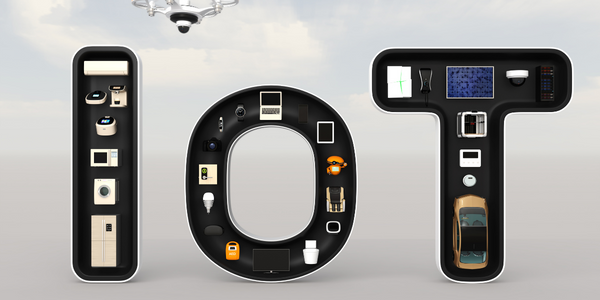
Case Study
Premium Appliance Producer Innovates with Internet of Everything
Sub-Zero faced the largest product launch in the company’s history:It wanted to launch 60 new products as scheduled while simultaneously opening a new “greenfield” production facility, yet still adhering to stringent quality requirements and manage issues from new supply-chain partners. A the same time, it wanted to increase staff productivity time and collaboration while reducing travel and costs.
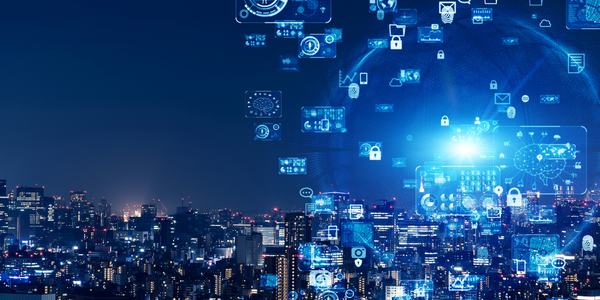
Case Study
Integration of PLC with IoT for Bosch Rexroth
The application arises from the need to monitor and anticipate the problems of one or more machines managed by a PLC. These problems, often resulting from the accumulation over time of small discrepancies, require, when they occur, ex post technical operations maintenance.
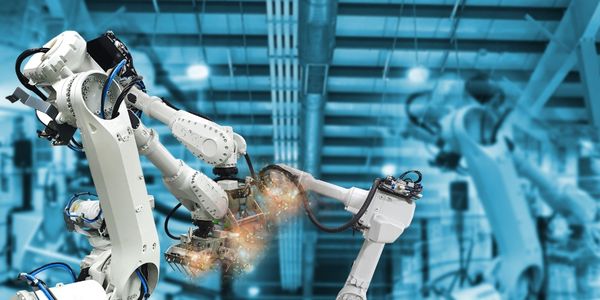
Case Study
Robot Saves Money and Time for US Custom Molding Company
Injection Technology (Itech) is a custom molder for a variety of clients that require precision plastic parts for such products as electric meter covers, dental appliance cases and spools. With 95 employees operating 23 molding machines in a 30,000 square foot plant, Itech wanted to reduce man hours and increase efficiency.