Toll Ensures Operational Efficiency for Its Rescue Helicopter Fleet with Honeywell Inventory Control Solutions
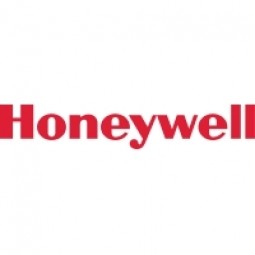
Customer Company Size
Large Corporate
Region
- Asia
- Pacific
Country
- Australia
Product
- Honeywell PC42t desktop printer
- Honeywell CK3X handheld computer
Tech Stack
- Barcode Scanning
- Inventory Management
Implementation Scale
- Enterprise-wide Deployment
Impact Metrics
- Productivity Improvements
- Customer Satisfaction
Technology Category
- Functional Applications - Inventory Management Systems
- Functional Applications - Remote Monitoring & Control Systems
Applicable Industries
- Transportation
- Healthcare & Hospitals
Applicable Functions
- Maintenance
- Logistics & Transportation
Use Cases
- Inventory Management
- Fleet Management
- Remote Asset Management
Services
- System Integration
- Hardware Design & Engineering Services
About The Customer
Toll Helicopters, headquartered in Australia, has been providing safe and reliable helicopter services for over ten years. Their services include emergency medical service, search and rescue operations, passenger transfer, and logistics support. The integrated team comprises pilots, aircrew, helicopter engineers, safety managers, trainers, and inventory and aviation management specialists with extensive civil and military helicopter experience. Toll operates globally and is contracted to manage the New South Wales (NSW) Ambulance Aeromedical Rescue Helicopter Service, which is based out of Sydney, Wollongong, Orange, and Canberra. The fleet includes eight AgustaWestland 139 (AW139) helicopters, which are crucial for connecting rural communities and regional health emergencies to metropolitan health services.
The Challenge
Toll Helicopters, contracted to operate the New South Wales (NSW) Ambulance Aeromedical Rescue Helicopter Service, needed an efficient inventory management and maintenance system for its helicopter base. The fleet, consisting of eight AgustaWestland 139 (AW139) helicopters, provides critical services such as emergency medical service, search and rescue operations, and passenger transfer. The challenge was to find a smart, compact, and easy-to-use solution that would enhance accuracy, efficiency, and productivity while providing a good return on investment.
The Solution
Honeywell provided an inventory solution that includes the PC42t desktop printer and the CK3X handheld computer. When a helicopter part arrives at the aeromedical base, a specific label is created by the PC42t desktop printer and placed on the part. The part is then scanned by the CK3X handheld computer and assigned a location label to ensure it can be quickly found when needed. This system not only helps in locating spare parts but also provides visibility on when common helicopter parts are running low and need to be reordered. The PC42t desktop printer is quiet, reliable, and fits seamlessly into the existing printing environment, while the CK3X handheld computer enhances accuracy and productivity with its sleek, easy-to-carry design. The rugged and versatile CK3X adapts to almost all working conditions and temperatures, making it an ideal choice for the demanding environment of helicopter maintenance.
Operational Impact
Case Study missing?
Start adding your own!
Register with your work email and create a new case study profile for your business.
Related Case Studies.
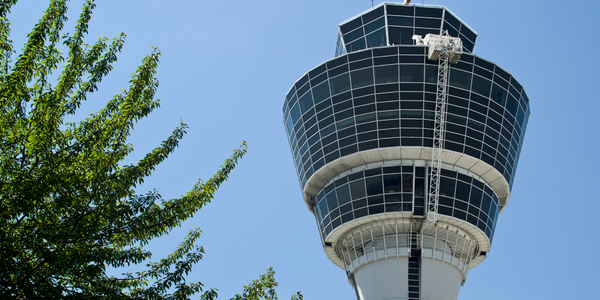
Case Study
Airport SCADA Systems Improve Service Levels
Modern airports are one of the busiest environments on Earth and rely on process automation equipment to ensure service operators achieve their KPIs. Increasingly airport SCADA systems are being used to control all aspects of the operation and associated facilities. This is because unplanned system downtime can cost dearly, both in terms of reduced revenues and the associated loss of customer satisfaction due to inevitable travel inconvenience and disruption.
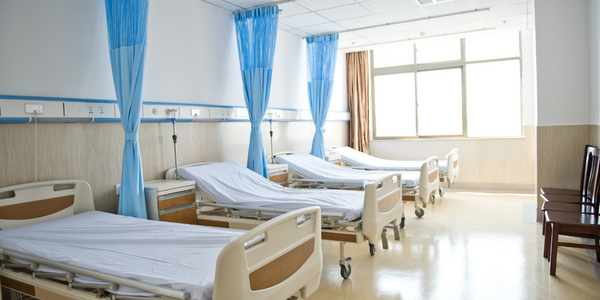
Case Study
Hospital Inventory Management
The hospital supply chain team is responsible for ensuring that the right medical supplies are readily available to clinicians when and where needed, and to do so in the most efficient manner possible. However, many of the systems and processes in use at the cancer center for supply chain management were not best suited to support these goals. Barcoding technology, a commonly used method for inventory management of medical supplies, is labor intensive, time consuming, does not provide real-time visibility into inventory levels and can be prone to error. Consequently, the lack of accurate and real-time visibility into inventory levels across multiple supply rooms in multiple hospital facilities creates additional inefficiency in the system causing over-ordering, hoarding, and wasted supplies. Other sources of waste and cost were also identified as candidates for improvement. Existing systems and processes did not provide adequate security for high-cost inventory within the hospital, which was another driver of cost. A lack of visibility into expiration dates for supplies resulted in supplies being wasted due to past expiry dates. Storage of supplies was also a key consideration given the location of the cancer center’s facilities in a dense urban setting, where space is always at a premium. In order to address the challenges outlined above, the hospital sought a solution that would provide real-time inventory information with high levels of accuracy, reduce the level of manual effort required and enable data driven decision making to ensure that the right supplies were readily available to clinicians in the right location at the right time.
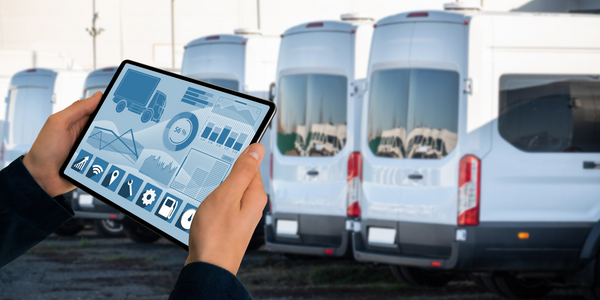
Case Study
IoT-based Fleet Intelligence Innovation
Speed to market is precious for DRVR, a rapidly growing start-up company. With a business model dependent on reliable mobile data, managers were spending their lives trying to negotiate data roaming deals with mobile network operators in different countries. And, even then, service quality was a constant concern.
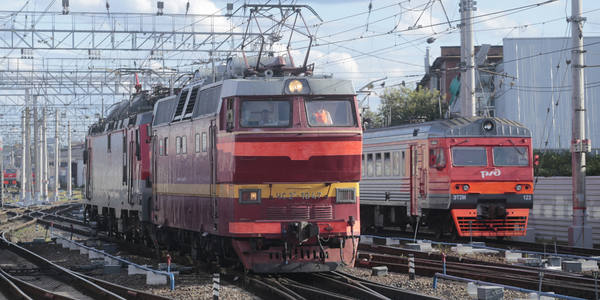
Case Study
Digitize Railway with Deutsche Bahn
To reduce maintenance costs and delay-causing failures for Deutsche Bahn. They need manual measurements by a position measurement system based on custom-made MEMS sensor clusters, which allow autonomous and continuous monitoring with wireless data transmission and long battery. They were looking for data pre-processing solution in the sensor and machine learning algorithms in the cloud so as to detect critical wear.
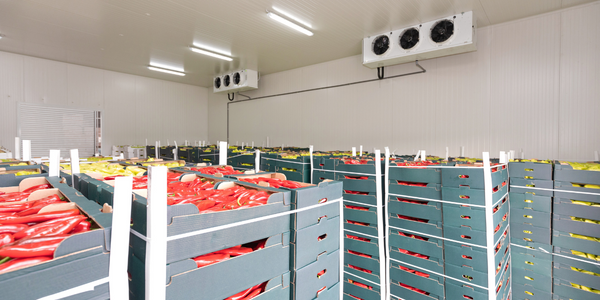
Case Study
Cold Chain Transportation and Refrigerated Fleet Management System
1) Create a digital connected transportation solution to retrofit cold chain trailers with real-time tracking and controls. 2) Prevent multi-million dollar losses due to theft or spoilage. 3) Deliver a digital chain-of-custody solution for door to door load monitoring and security. 4) Provide a trusted multi-fleet solution in a single application with granular data and access controls.
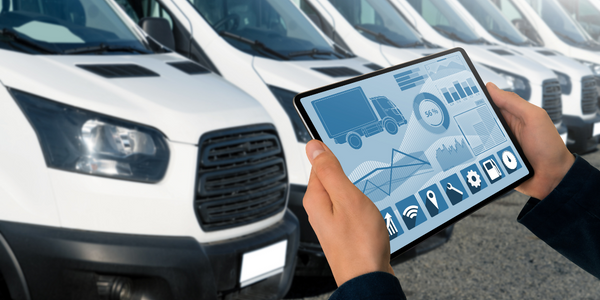
Case Study
Vehicle Fleet Analytics
Organizations frequently implement a maintenance strategy for their fleets of vehicles using a combination of time and usage based maintenance schedules. While effective as a whole, time and usage based schedules do not take into account driving patterns, environmental factors, and sensors currently deployed within the vehicle measuring crank voltage, ignition voltage, and acceleration, all of which have a significant influence on the overall health of the vehicle.In a typical fleet, a large percentage of road calls are related to electrical failure, with battery failure being a common cause. Battery failures result in unmet service agreement levels and costly re-adjustment of scheduled to provide replacement vehicles. To reduce the impact of unplanned maintenance, the transportation logistics company was interested in a trial of C3 Vehicle Fleet Analytics.